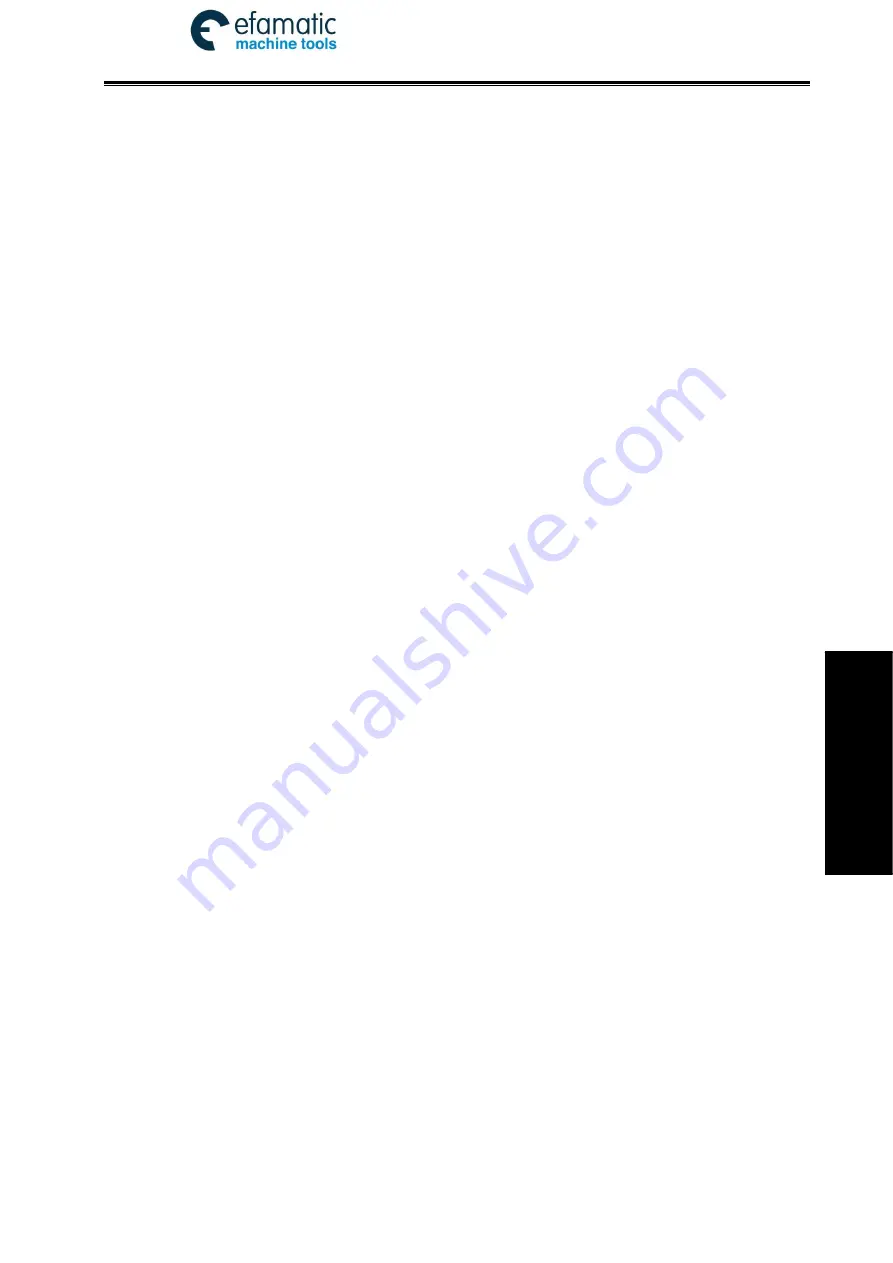
Official GSK Agents in South Africa
Tel: +27 11 626 2720, [email protected]
Chapter 4 Machine Debugging methods and Modes
489
Ⅲ
Connection
Basic parameters are needed to adjust the inverter:
CW or CCW code mode selection: it is determined by terminal VF;
Frequency setting mode selection: it is determined by terminal FR;
If the speed by programming is not consistent with that detected by the encoder, it can be
adjusted to be consistent with the actual one by adjusting the data parameter No.037
~
No.040.
Speed adjustment method: select the corresponding spindle gear, determine the data parameter
is 9999 as for this system gear, set the spindle override for 100%. Input spindle run command in MDI
mode to run the spindle: M03/M04 S9999, view the spindle speed shown on the right bottom of the
screen, then input the speed value displayed into the corresponding system parameter.
When entering S9999 code, the voltage should be 10V, S0 for 0V. If there is a voltage error,
adjust bit parameter No.021 and No.036 to correct the voltage offset value (corrected by
manufacturer, usually not needed).
For the current max. speed gear, if the analog voltage output by CNC is not 10V, set it for 10V by
adjusting the data parameter No.021; when the input speed is 0, if the spindle still slowly rotates, it
means the analog voltage output by CNC is higher than 0V, so set a smaller value for data parameter
No.036.
If the machine is not fixed with an encoder, the spindle speed can be detected by a speed
sensing instrument, input S9999 in MDI mode to set the speed value displayed by the instrument into
the data parameter No.037
~
No.040.
4.6.5 Spindle Speed Series Control
The spindle speed series control can be carried out by CNC parameter, directly control the
spindle servo drive unit to achieve the stepless speed by delivering the seires data from bus; the
relevant parameters to be adjusted are shown below:
The Bit 4 of the status parameter
№
001 equals to =1: Select the spindle speed analog voltage or
series control;
The Bit 7 of the status parameter
№
195 equals to 1: Select the spindle speed as the series
control;
Data parameters
№
037
~
№
040: The top speed of each step;
When the revolving speed specified by programming is inconsistent with the one of the encoder
detection, the specified speed becomes consistent with the actual one by adjusting the data
parameters
№
037
~
№
040.
Revolving speed adjustment method: Firstly, shift the spindle to the corresponding gears and
ensure that the corresponding gear data parameter for the system is 9999, adjust the spindle override
as 100%; Input the spindle operation command on the MDI interface and operate the M03/M04
S9999; secondly, observe the spindle speed on the right corner of the screen; lastly, input the
displayed revolving speed value to the corresponding data parameter of the gear.
When the machine tool does not install the encoder, it can be detected the spindle speed by
revolving speed sensor; MDI code inputs the S9999; Set the displayed revolving speed on its sensor
to the corresponding gear data parameters
№
037
~
№
040.
4.7 Backlash Offset
The X axis backlash offset value is input by diameter, Z axis backlash offset value is input by the
actual backlash which can be measured by a dial-indicator, a micrometer or a laser detector. Because
Содержание 980TDi
Страница 17: ...Official GSK Agents in South Africa Tel 27 11 626 2720 design efamatic com 1 Programming I Programming...
Страница 225: ...Official GSK Agents in South Africa Tel 27 11 626 2720 design efamatic com 209 Operation II Operation...
Страница 379: ...Official GSK Agents in South Africa Tel 27 11 626 2720 design efamatic com 363 Connection III Connection...
Страница 539: ...Official GSK Agents in South Africa Tel 27 11 626 2720 design efamatic com 523 IV Appendix IV Appendix...