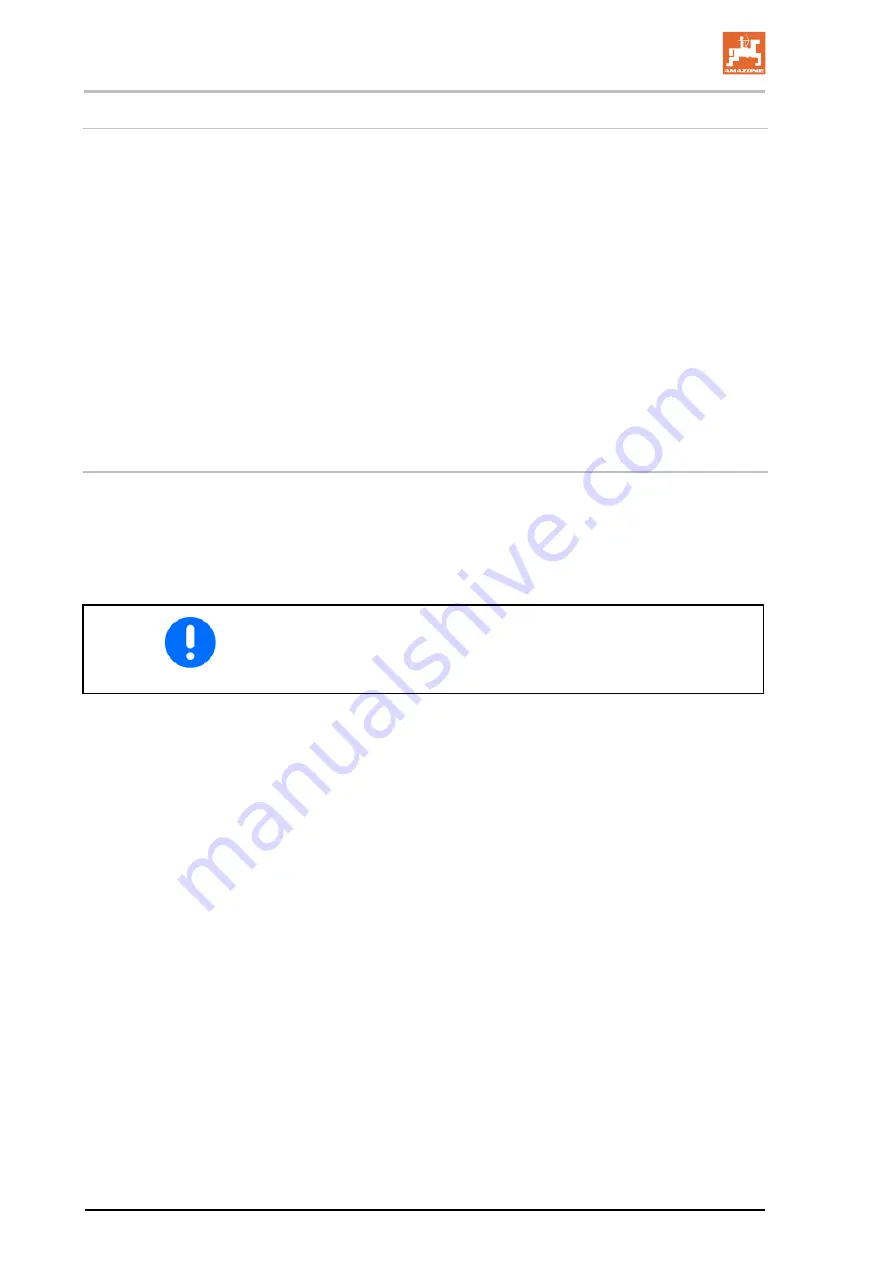
Cleaning, maintenance and repairs
General visual check
Carry out a general visual check of the brake system. Observe and
check the following criteria:
•
Piping, hose lines and hose couplings must not be externally
damaged or rusted.
•
Hinges, e.g. on fork heads, must be properly secured, easy to
move, and not worn out.
•
Ropes and cables
ο
Must be properly run.
ο
May not have any visible cracks.
ο
May not be knotted.
•
Check the piston stroke on the brake cylinders, and adjust as
necessary.
12.5.6.1 Checking the service brake system for safe operating condition (specialist workshop)
Have the safe operating condition of the service brake system
checked in a specialist workshop.
Piping, hose lines and hose couplings must not be externally dam-
aged or rusted.
In Germany Section 57 of the regulation BGV D 29 of the industrial
injuries mutual insurance organisation requires as follows:
the keeper has to have vehicles tested as required, however at least
once annually, by an expert as to their safe operating condition.
192
Cirrus BAH0049-1 09.14
Содержание Cirrus 3002
Страница 28: ...General Safety Instructions Fig 3 Fig 4 Fig 5 Fig 6 Fig 7 Fig 8 Fig 9 Fig 10 28 Cirrus BAH0049 1 09 14...
Страница 89: ...Structure and function Fig 95 Cirrus BAH0049 1 09 14 89...
Страница 136: ...Settings 8 10 1 136 Cirrus BAH0049 1 09 14...
Страница 206: ...Hydraulic system diagrams Fig 224 206 Cirrus BAH0049 1 09 14...
Страница 208: ...Hydraulic system diagrams Fig 225 208 Cirrus BAH0049 1 09 14...