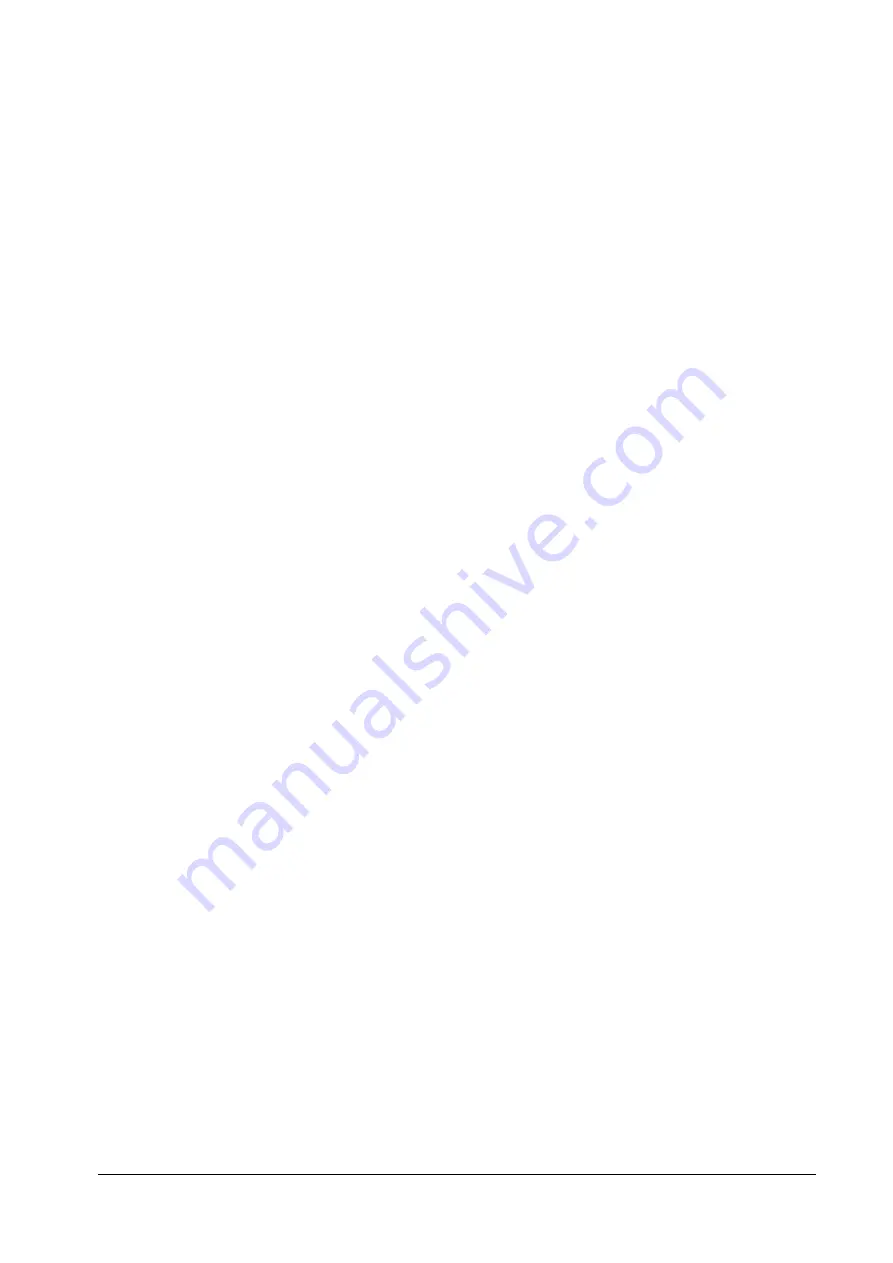
72
XYZ Machine Tools Ltd
TRAK
2
OP
Installation, Maintenance, Service & Part List Manual
124 - SPINDLE ERROR - The spindle did not orient correctly
. - When the spindle is commanded to
orient, the control waits for the spindle to stop and checks the encoder position. If the encoder position
does not match the value that was entered in Service Code 510 (within about 1/2° or 6 encoder counts),
then orientation will fail. Also, the orientation must happen within 12 seconds and the spindle must come
to a complete stop.
126 - TOOL CLAMP ERROR - The spindle is in the unclamped position and needs to be clamped
to proceed.
Check that air pressure is available and the limit switches are functioning properly. The tool
unclamp is either jammed or the limit switch is not functioning. Check the LED on the back of the control.
Use Service Code 521 to confirm proper inputs.
127 - TOOL UNCLAMP ERROR - The spindle is in the clamped position and needs to be
unclamped to proceed.
Check that air pressure is available and the limit switches are functioning
properly. - The tool unclamp is either jammed or the limit switch is not functioning. Check the LED on the
back of the control. Use Service Code 521 to confirm proper inputs.
128 - ATC ERROR - The ATC was commanded to home but it's not in the back position.
Manually move the ATC all the way back and then re-home the machine.
- This message happens
during homing. If the ATC is back, then the limit switch probably has moved or failed. Check the light on
the switch and the LED on the back of the control. Use Service Code 521 to confirm proper inputs.
129 - ATC ERROR
-
The ATC was commanded to move but its position is not known. Check that
air pressure is available and ATC limit switches are functioning properly.
- The ATC loses air
pressure, 24 volts or is not on the limit switch when the machine is disabled, it needs to be pushed back
and servos re-enabled. Even a very short loss of air pressure may cause this condition. The ATC must be
"homed" the first time after power-up when the axes are homed. The ATC must be on the back limit
switch, air pressure and 24 volts must be available, then the door must be closed and the GO button
pressed (to initiate homing).
131 - ATC ERROR - The ATC timed-out moving to the front. Check and make sure that there is
no excess of chips accumulated between the ATC and the back of the table, that air pressure is
available, and that the ATC limit switches are functioning properly.
- When moving forward, the
ATC did not detected the front limit switch. Check the light on the switch and the LED on the back of the
control. Use Service Code 521 to confirm proper inputs.
132 - ATC ERROR - The ATC was commanded to the back position, but the back limit switch is
not active. Check the limit switches.
- If the ATC is back then the limit switch probably has moved or
failed. Check the light on the switch and the LED on the back of the control. This error message may occur
during tool changes and tool loading/unloading.
139 - ATC ERROR - The ATC carrier is trying to move but the air pressure is too low. Check air
pressure and make sure it is set to the correct amount.
- If the ATC is commanded to move but
pressure was not available (for even a short time) this message may occur. During a tool change, when the
Tool Unclamp (draw-bar) actuator is activated to release the tool, the sudden drop in air pressure may
casue this problem; especially if the air pressure is set below 65 PSI. Check that the air pressure regulator
lower limit is properly adjusted and that the shop air supply is sufficiently high and has enough volume not
to cause a momentary drop in air pressure. Also, check that the air filter is not plugged up, if it looks dirty,
it may require cleaning or replacement.
208 - ATC ERROR - ATC limit switch failure. Both the front and the back switches are active at
the same time.
The ATC location is unknown. Check that both limit switches are functioning properly. -
During normal operation both switches should not be active. Check the lights on the switches and the LEDs
on the back of the control. Use Service Code 521 to confirm proper inputs.
216 - TOOL CLAMP ERROR - The tool clamp was actuated, but no air pressure is available.
Check air pressure.
- Check that the air pressure regulator is properly adjusted and that the shop air
supply is sufficiently high and has enough air flow not to cause a momentary drop in air pressure. If the air
supply pressure is Ok, check the air filter and make sure it is not excessively dirty.
217 - TOOL CLAMP ERROR - Both tool clamp and unclamp limit switches are active at the same
time. Check that both limit switches are functioning properly.
- During normal operation both
switches should not be active. Check the LEDs on the back of the control. Use Service Code 521 to confirm
proper inputs.
Summary of Contents for TRAK 2OP M11 Mill
Page 9: ...5 XYZ Machine Tools Ltd TRAK 2OP Installation Maintenance Service Part List Manual...
Page 10: ...6 XYZ Machine Tools Ltd TRAK 2OP Installation Maintenance Service Part List Manual...
Page 11: ...7 XYZ Machine Tools Ltd TRAK 2OP Installation Maintenance Service Part List Manual...
Page 12: ...8 XYZ Machine Tools Ltd TRAK 2OP Installation Maintenance Service Part List Manual...
Page 13: ...9 XYZ Machine Tools Ltd TRAK 2OP Installation Maintenance Service Part List Manual...
Page 130: ...1 14 15 1 8 15 12 15 14...