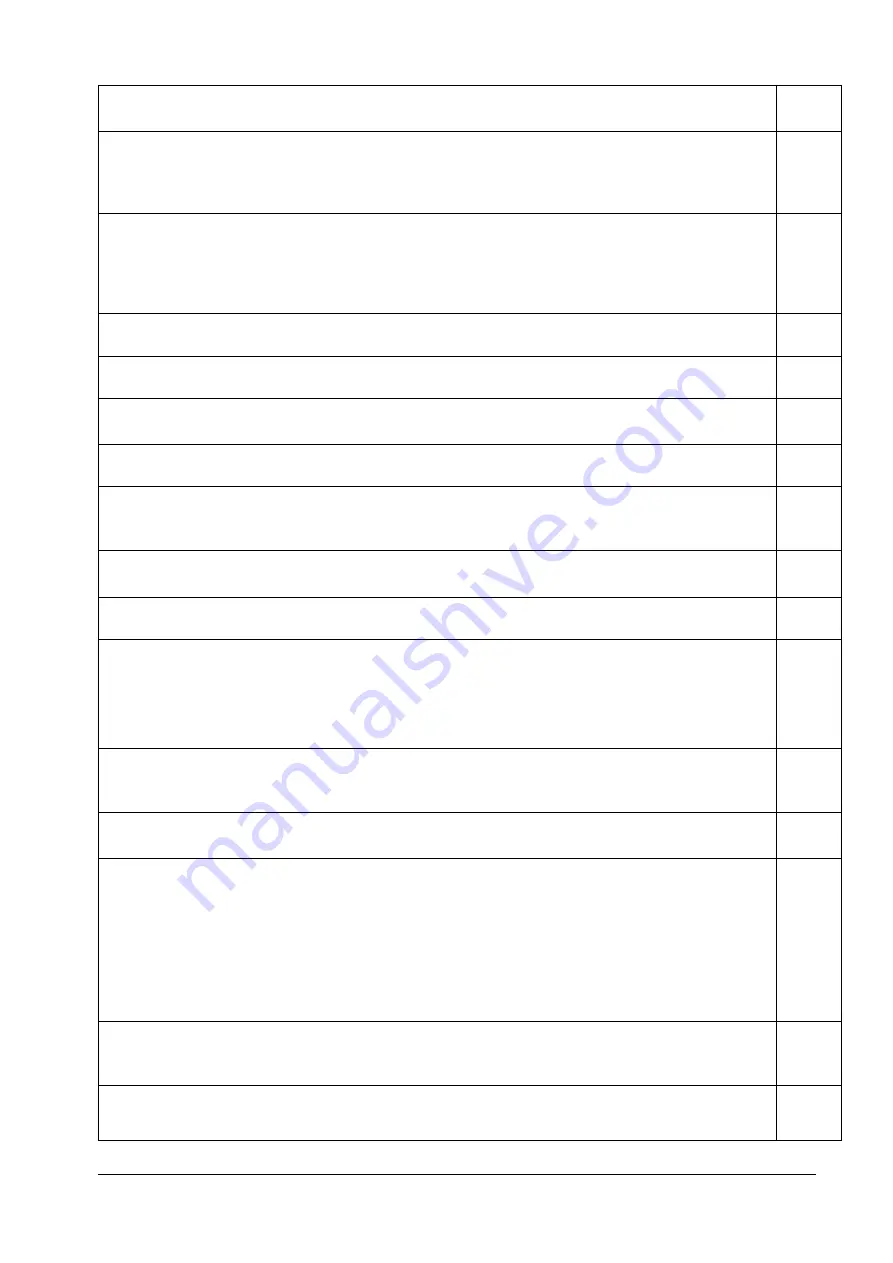
24
XYZ Machine Tools Ltd
TRAK
2
OP
Installation, Maintenance, Service & Part List Manual
2. Attach rear panel which contains air regulator, pressure sensor and ATC solenoid and make all
connections.
□
3. Visually inspect the electrical supply cable going into the electrical cabinet. Visually verify the
wiring is correct per our wiring diagram and the voltage is between 380 and 415 volts. Have the
customer resolve any voltage discrepancies coming into the machine. Do not turn on machine if
voltage is outside of ranges listed above.
□
4. Move the wires on the transformer depending on the incoming voltage coming into the machine.
Adjusting the input wires to the transformer will control the 115 and 220 volt outputs from the
transformer (there is no adjustment on the secondary side of the transformer). In any case
measure the output voltage from the transformer to confirm the reading is 115 ±5volts. Note any
discrepancies that you see.
□
5. Clean the machine if needed and remove any remaining protective grease or oil.
□
6. Re-attach the Z cable carrier if it has been disconnected for shipping purposes.
□
7. Remove the tape that is holding a plug in the network port. The networking plug is found on
the upper sheet metal on the right side of the machine.
□
8. Connect the electrical and air supplies. Turn on the power to the machine.
□
9. Press the servo on button to make sure the axis motors are activated. The screen should
change from saying SERVO OFF to SERVO ON. The lube pump should also cycle 1 time when the
SERVO ON button is pressed.
□
10. Remove the head support bracket and parts used to hold the ATC in place. WARNING! Refer
to section 3.2 before proceeding. Install the door handle on front door.
□
11. Check that the air pressure regulator is set to 90 psi
□
12. Press SET HOME to home machine.
Did the X axis home properly?
Did the Y axis home properly?
Did the Z axis home properly?
□
13. Adjust leveling feet to achieve good spindle tram. We recommend the tram be checked each
time the machine moves around the shop. Make sure the leveling feet are threading into the
spacer blocks so the machine sits about 140mm off the ground.
□
14. In DRO mode, turn the spindle on and then turn the coolant pump on by pressing the coolant
AUX button.
□
15. Go to DRO mode and move each axis in a positive direction.
Select the X axis, does the spindle head move to the right when turning EHW CW?
Select the Y axis, does the saddle move toward the operator when turning the EHW CW?
Select the Z axis, does the head move up when turning the EHW CW?
Check that 1 click of the EHW in 0.020” mode is 0.5mm.
(use Service Code 66 to select metric mode)
□
16. Double check the motor index angle for each axis using service code 505. If this needs to be
modified, then the ATC tool change locations and ball lock location may need to be reset in services
codes 520 and 500 respectively.
□
17. Final test each axis by jogging (turning EHW) at 0.020” speed into the soft limits. Verify the
machine does not hit the hard stop on the machine. Re-adjust limit switch cam if it does. Service
Code 500 and 520 may need to be performed if major adjustments have been made to the X and Y
□
Summary of Contents for TRAK 2OP M11 Mill
Page 9: ...5 XYZ Machine Tools Ltd TRAK 2OP Installation Maintenance Service Part List Manual...
Page 10: ...6 XYZ Machine Tools Ltd TRAK 2OP Installation Maintenance Service Part List Manual...
Page 11: ...7 XYZ Machine Tools Ltd TRAK 2OP Installation Maintenance Service Part List Manual...
Page 12: ...8 XYZ Machine Tools Ltd TRAK 2OP Installation Maintenance Service Part List Manual...
Page 13: ...9 XYZ Machine Tools Ltd TRAK 2OP Installation Maintenance Service Part List Manual...
Page 130: ...1 14 15 1 8 15 12 15 14...