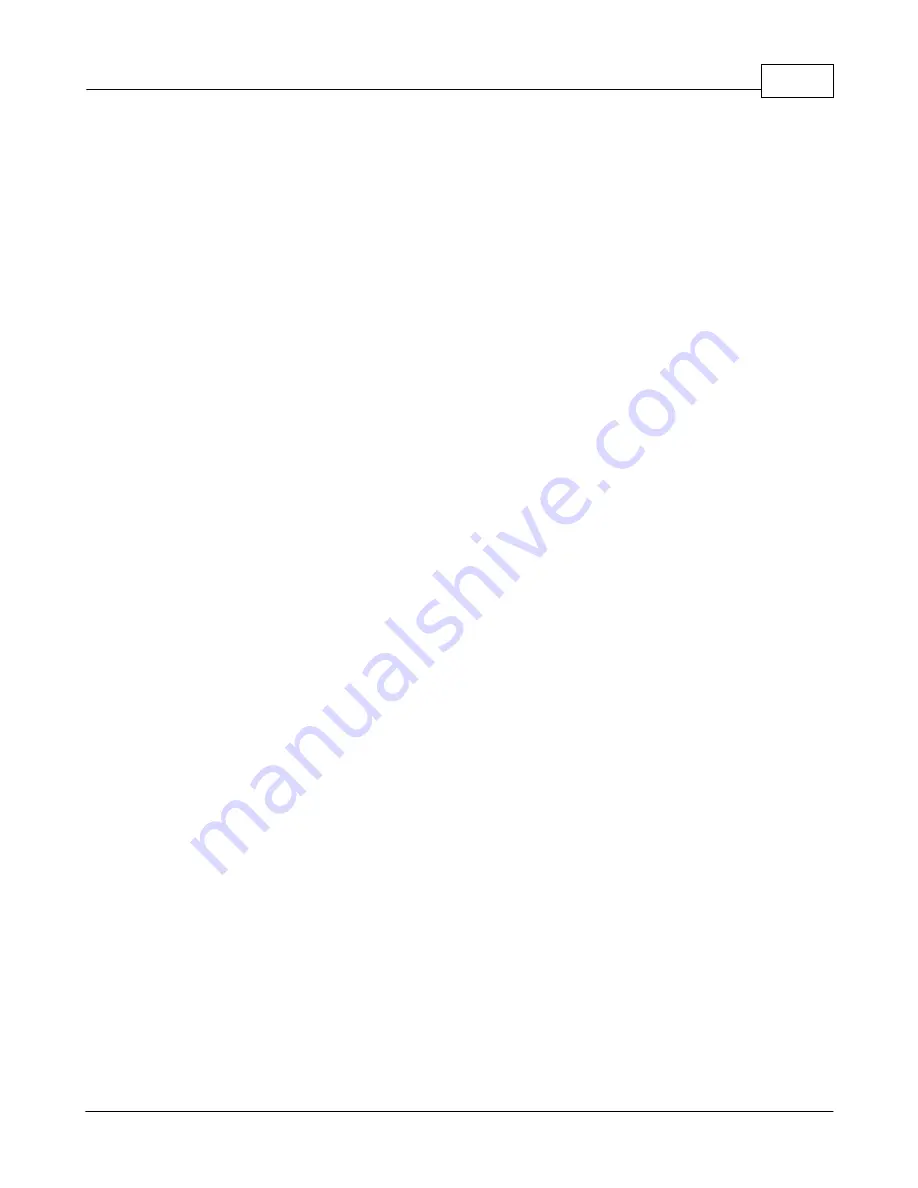
Operations
171
© 2006 Vision Engraving Systems
different sized engraving cutters, be sure to assign each cutter to a unique color. You will
then be able to use the
Engrave By Color
command to output the job one color at a time.
As a general rule, never set the fill color to be the same as the outline color of the object
being filled. Vision Pro will automatically offset the cutter when generating the fill pattern so
that the engraved output is exactly the same size as the original outlines. As an example, if
you selected a .020” engraving cutter to use for the fill, the fill pattern will be set inside the
edges of the original artwork by .010” (half the cutter width). This will allow the outside
cutting edge of the cutter to line up precisely with the original outline of the artwork. You can
see this onscreen by turning on the
Show Line Style
command under the
View
menu.
Inlay:
This section is used when creating inlayed objects. This option should normally not
be checked and the gap should be left at 0.
Fill Style: Important Field
- Vision Pro offers 6 unique fill styles to choose from. This
determines the path the cuter will take while creating the fill. For engraving, 2 of the choices
produce the best result:
1)
S-Sweep
- This is a basic connected hatch fill very useful when your artwork contains
large open areas to fill. When this is selected, you can define the angle of the hatch lines.
2)
Reverse Spiral
- This option directs the fill lines to attempt to follow the contour of the
artwork. This is useful when your artwork consists of more fine details or is mainly text
shapes. Both options have a check box for optimization, which will make the fill better
suited for engraving with a depth nose, and should normally be left checked on.
Fill Overlap: Important Field
- Two fields are shown for this value. This is the amount the
cutter overlaps the adjacent fill line. Think of this as the overlap you do with your lawn
mower when cutting the grass. The first field is that actual overlap measurement and the
second is the percentage of the cutter size. I recommend always using the second field and
setting this to about 15% - 20% for all fills. Feel free to experiment as needed. Higher
overlap values might give a better finish in the fill area at the expense of increased
engraving time.
Lead In and Cleanup Flange:
These fields are used for routing and machining and should
normally not be checked and all values set to 0.
When the fields are entered press OK to generate the fill. If you see gaps where the fill
routine did not complete the fill, undo the fill and try again with a smaller cutter. If everything
looks OK, your artwork is now ready to engrave in Vision Pro.
Creating Custom Vision Pro Drivers
It is sometimes helpful to create custom output drivers for different applications that need to
be engraved more then one time. It makes the setup time much less if you need to engrave
a similar item at a later date. The procedure below needs to be done only one time for each
custom driver that you would like to create.
In the example below, we will setup a custom driver to engrave the pen found in lesson 2 in
this document.
Install the pen holder and insert the pen into the holder per the steps in lesson 2 - engraving
pens.
Summary of Contents for MaxPro
Page 5: ...Chapter I ...
Page 11: ...Chapter II ...
Page 23: ...Configuration 19 2006 Vision Engraving Systems 3 Click on the IP Address tab ...
Page 60: ......
Page 61: ...Chapter III ...
Page 100: ...Vision MaxPro 96 2006 Vision Engraving Systems Mounting the item to be engraved ...
Page 179: ...Operations 175 2006 Vision Engraving Systems The Plot screen below will appear ...
Page 182: ......
Page 183: ...Chapter IV ...
Page 191: ...Chapter V ...
Page 202: ...Vision MaxPro 198 2006 Vision Engraving Systems W Windows 2000 15 Windows 98 18 Windows XP 12 ...
Page 203: ......