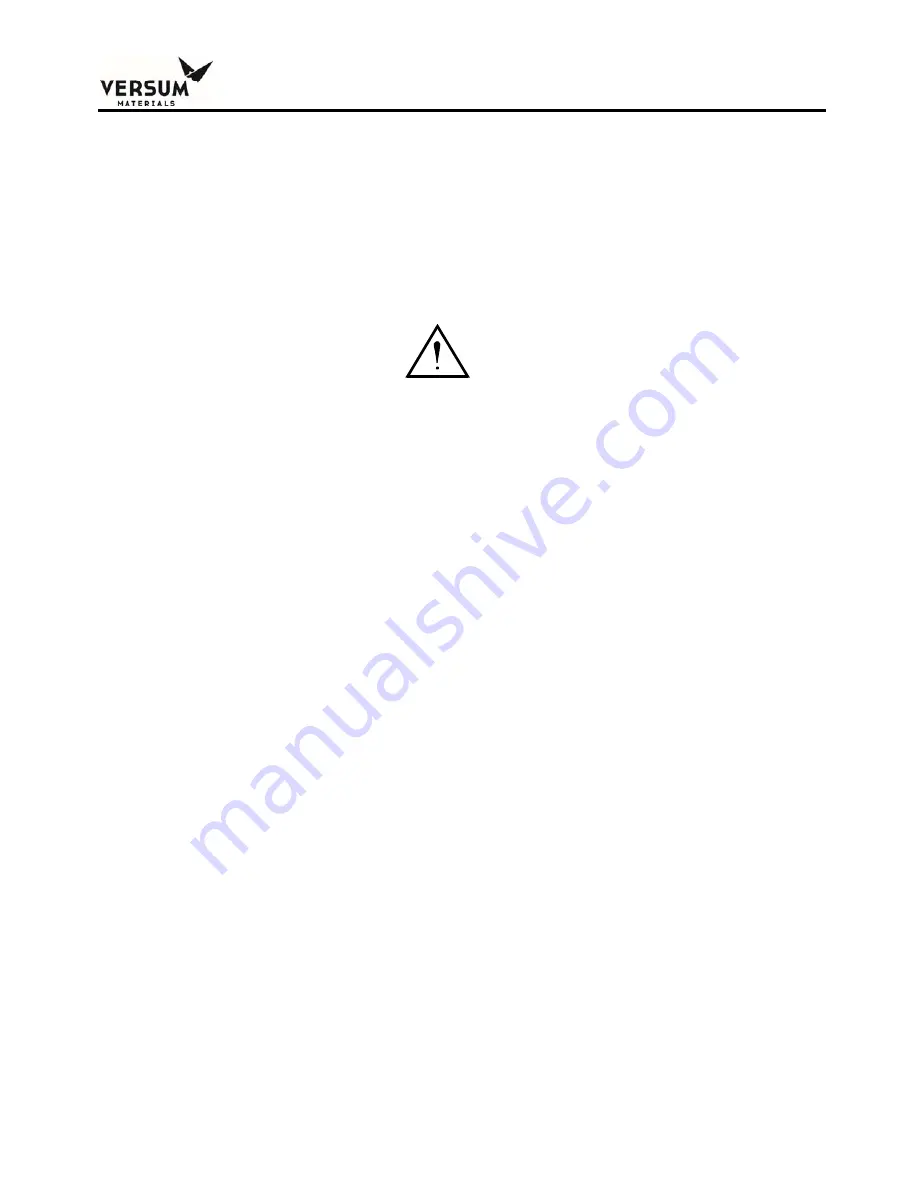
MNL000421.doc
Revision 00
08/26/2016
© Versum Materials, Inc. as of the revision and date shown. All rights reserved.
Confidential and Proprietary Data
Page
-
1
Chapter
3
VaporGuard® Absolute Control System for use with
Trans-LC™
WARNING
Only the VG300W/N are intended for use with Trans-LC™
3.1 VaporGuard® Manufactured for Use of Trans-LC™
The default configuration for a VG300W/N VaporGuard® is for the use of Trans-LC™.
The corresponding model number from the existing ATCS design are the
ATCS 15-TLC
and ATCS 15-TLCHFCK
models. The main difference between this model and the
others is the over-temperature protection circuit and lower heater/cooler power limits.
The over-temp interlock is a hard-wired interlock and is factory set. The software for
this model will only allow the set point to be adjusted on the front display or remotely to
a maximum value of 22ºC (
ATCS 15-TLCHFCK maximum set point to 20).
The temperature alarm window is programmable from the user interface. The
temperature PID control loop has been improved overall from the existing ATCS design
for all models.
The LED on-time is adjustable via the user interface in increments of seconds up to