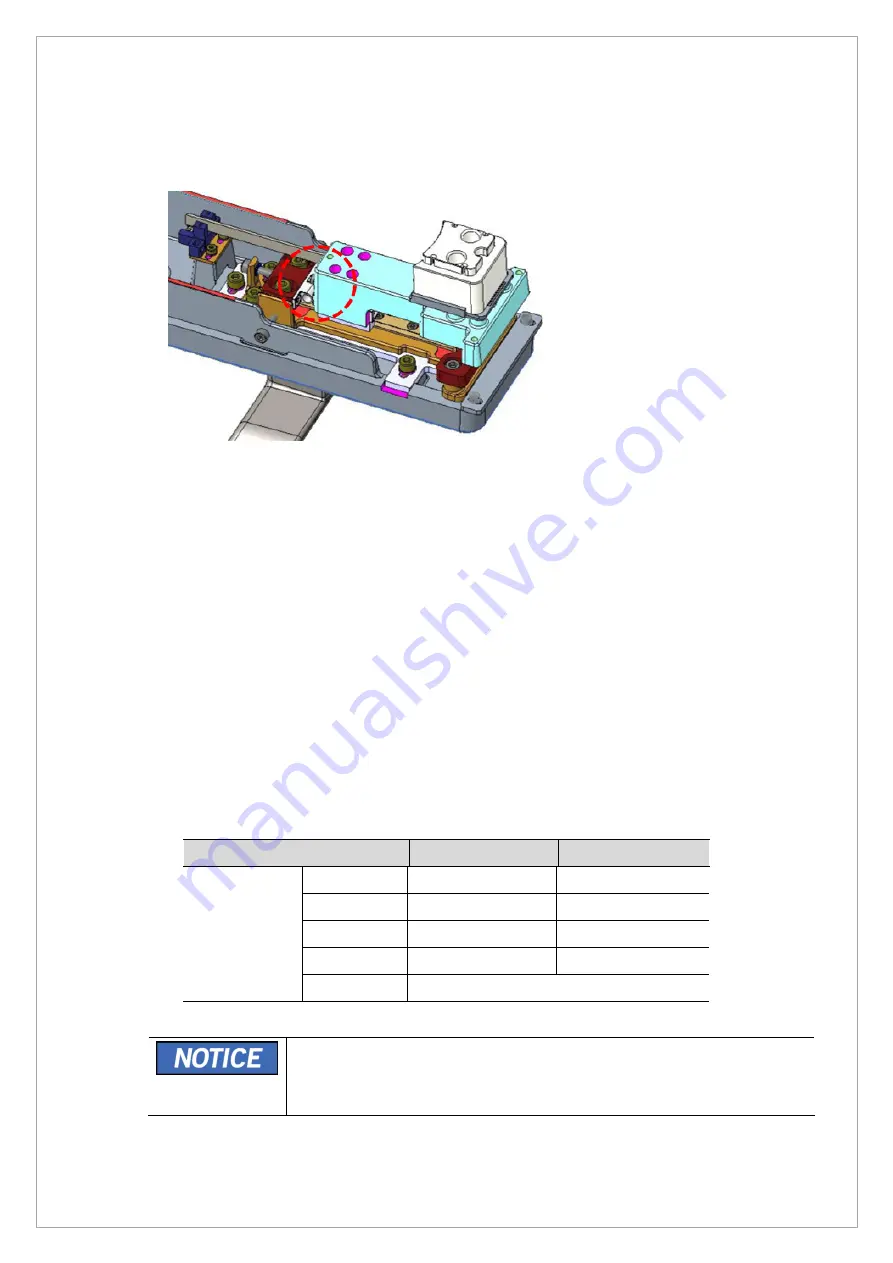
Page
131
of
244
4.2.
Equipment default values
4.2.1.
Bite location (PANO mode)
1. Move the bite position according to the Modality as shown in the image above.
2. PANO Mode: The position combined with the stopper in the direction (Left side) of the colum
4.3.
PANO Sensor Calibration
To optimize PANO image quality in the equipment, the operator should perform the Sensor setting &
calibration operation according to the following procedures.
Regular Sensor Calibration check-up is recommended to perform for image optimization against
temperature and humidity variation.
4.3.1.
PANO Sensor Calibration Standard
•
PANO Sensor Dark Calibration Standard Value
-
Dark data file median value:
700 ~ 2300
•
PANO Sensor Bright Calibration Standard Value
※
Bright standard value: 5 points with Cu 1 mm filter
Bright
Min
Max
Median value
Cal Point 1
50
80
Cal Point 2
80
200
Cal Point 3
200
400
Cal Point 4
400
600
Cal Point 5
600 ~
From the achieved PANO Sensor Bright Calibration data file, the 1 Point
Bright Data file and 5 Point Bright data file should meet the standard
value. Other results from different points Bright Datafile can be varied by
characteristics of each sensor.
Summary of Contents for A9 PHT-30CSS
Page 1: ...vatech A9 Technical manual Model PHT 30CSS Version 1 01 English...
Page 12: ...Page 11 of 244 1 2 1 Vertical Frame Part...
Page 22: ...Page 21 of 244 1 2 3 5 Generator DG 07E22T2...
Page 26: ...Page 25 of 244...
Page 27: ...Page 26 of 244...
Page 30: ...Page 29 of 244 1 3 3 Sensor Part Connection Diagram...
Page 31: ...Page 30 of 244 1 3 4 CEPH SENSOR Part Connection Diagram...
Page 32: ...Page 31 of 244 1 3 5 Connection Diagram Total assembly...
Page 43: ...Page 42 of 244 16 Loosen ten bolts as shown in the image below...
Page 112: ...Page 111 of 244 5 Click the V Vol button Click the Ready button...
Page 180: ...Page 179 of 244 10 Select 50 in the M box and click the center of the flat washer...
Page 209: ...Page 208 of 244 8 5 Appendix 8 5 1 Main MCU Board Parameters...
Page 244: ...vatech A9 www vatech com...