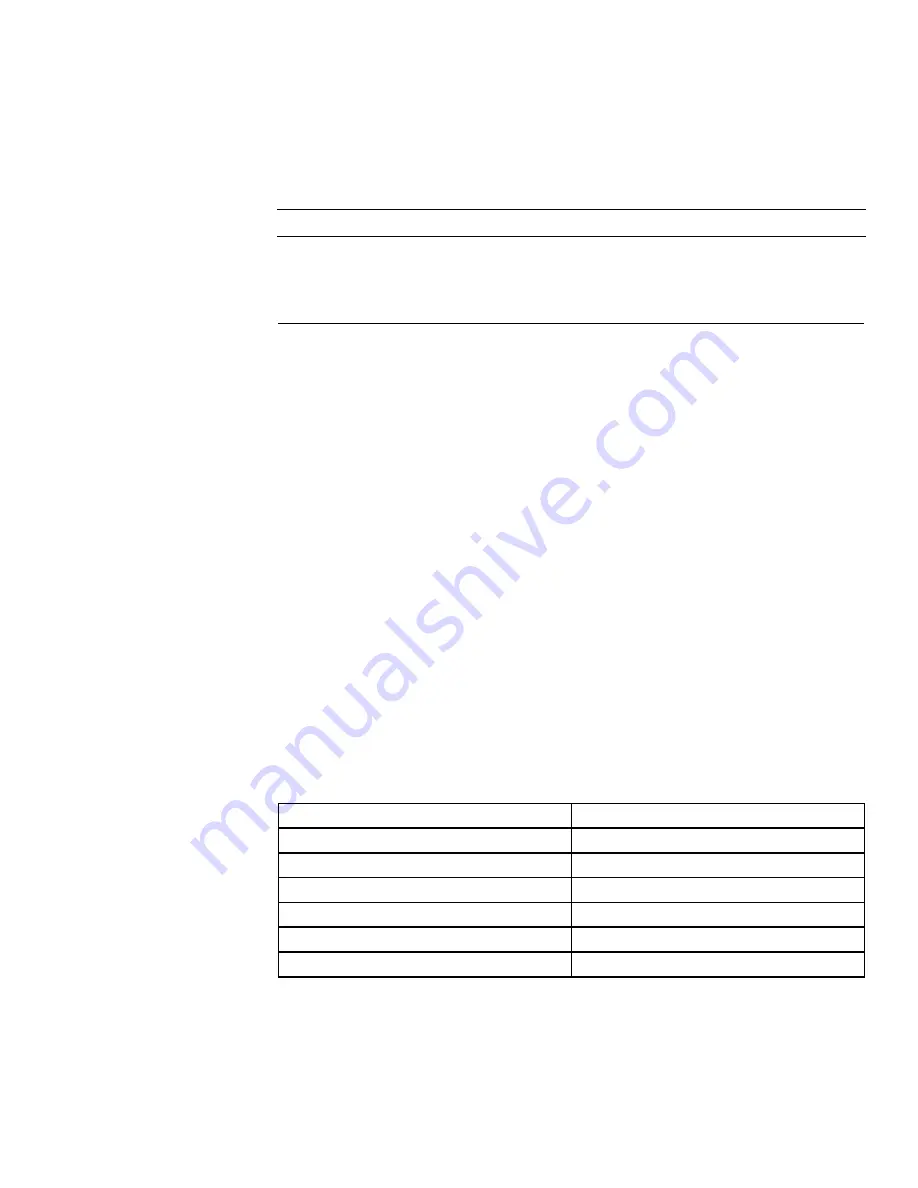
Installing an Adjustable Fitting (continued)
2. To help prevent a hydraulic leak, replace the O-ring when you open the
connection.
3. Lightly lubricate the O-ring with clean hydraulic fluid. Ensure that the threads
of the fitting are clean with no lubricant applied.
4. Turn back the locknut as far as possible. Ensure that the back-up washer is
not loose and it is pushed up as far as possible (Step 1 in
IMPORTANT
Before installing the fitting into the port, determine the material of
which the port is made. Installing a fitting into an aluminum port
requires a reduced installation torque.
5. Install the adjustable fitting into the port by hand until the washer contacts the
face of the port (Step 2 in
).
6. If the adjustable fitting needs to align with another component, rotate the fitting
counterclockwise until it is aligned to the desired position (Step 3 in
). Do not rotate the adjustable fitting more than 1 turn counterclockwise.
7. Hold the fitting in the correct alignment with a wrench and use a torque
wrench and tighten the fitting to the recommended torque value within the
specified range of torque values; refer to the
Fitting Installation Torque Table
(page 4–7)
. This tightening procedure requires a drive-adapter wrench (e.g.,
crowfoot wrench).
Note:
It may be necessary to use a drive-adapter wrench (e.g., crowfoot
wrench) to install a hydraulic fitting; refer to
When Using a Drive-Adapter Wrench (page 2–5)
.
8. If a torque wrench is not available or if space at the port prevents the use
of a torque wrench, use the alternative procedure
given below;
A. Hold the fitting in the correct alignment with a wrench and, if the port
material is steel, tighten the locknut with a second wrench to the listed
FFFT (Step 4 in
B. If the port material is aluminum, tighten the fitting to 60% of the listed
FFFT; refer to the
Flat From Finger Tight Table (page 4–9)
.
Flat From Finger Tight Table
Size
FFFT
4 (1/4 inch nominal hose or tubing)
1.00 ± 0.25
6 (3/8 inch)
1.50 ± 0.25
8 (1/2 inch)
1.50 ± 0.25
10 (5/8 inch)
1.50 ± 0.25
12 (3/4 inch)
1.50 ± 0.25
16 (1 inch)
1.50 ± 0.25
Traction Unit Operator's Manual
The
Traction Unit Operator's Manual
provides information regarding the
operation, general maintenance procedures, and maintenance intervals for your
machine. Refer to the
Traction Unit Operator's Manual
for additional information
when servicing the machine.
Groundsmaster 7210
Page 4–9
Hydraulic System: General Information
16222SL Rev C
Summary of Contents for Groundsmaster 7210
Page 4: ...NOTES Revision History Page 4 Groundsmaster 7210 16222SL Rev C...
Page 32: ...Specifications and Maintenance Special Tools Page 2 16 Groundsmaster 7210 16222SL Rev C...
Page 60: ...Diesel Engine Service and Repairs Page 3 28 Groundsmaster 7210 16222SL Rev C...
Page 196: ...Hydraulic System Service and Repairs Page 4 136 Groundsmaster 7210 16222SL Rev C...
Page 304: ...Chassis Service and Repairs Page 6 42 Groundsmaster 7210 16222SL Rev C...
Page 327: ...Drawing 105 7260 Rev E Sheet 1 16222SL Rev C Page A 3 Hydraulic Schematic g186843...
Page 328: ...Page A 4 16222SL Rev C Drawing 119 4372 Rev C Sheet 1 Electrical Schematic Platform g186842...
Page 329: ...Drawing 119 4377 Rev C Sheet 1 16222SL Rev C Page A 5 Electrical Schematic Engine g186841...
Page 336: ...Page A 12 16222SL Rev C Drawing 119 4386 Rev A Sheet 1 Wire Harness Drawing Cab Power g186851...
Page 342: ......