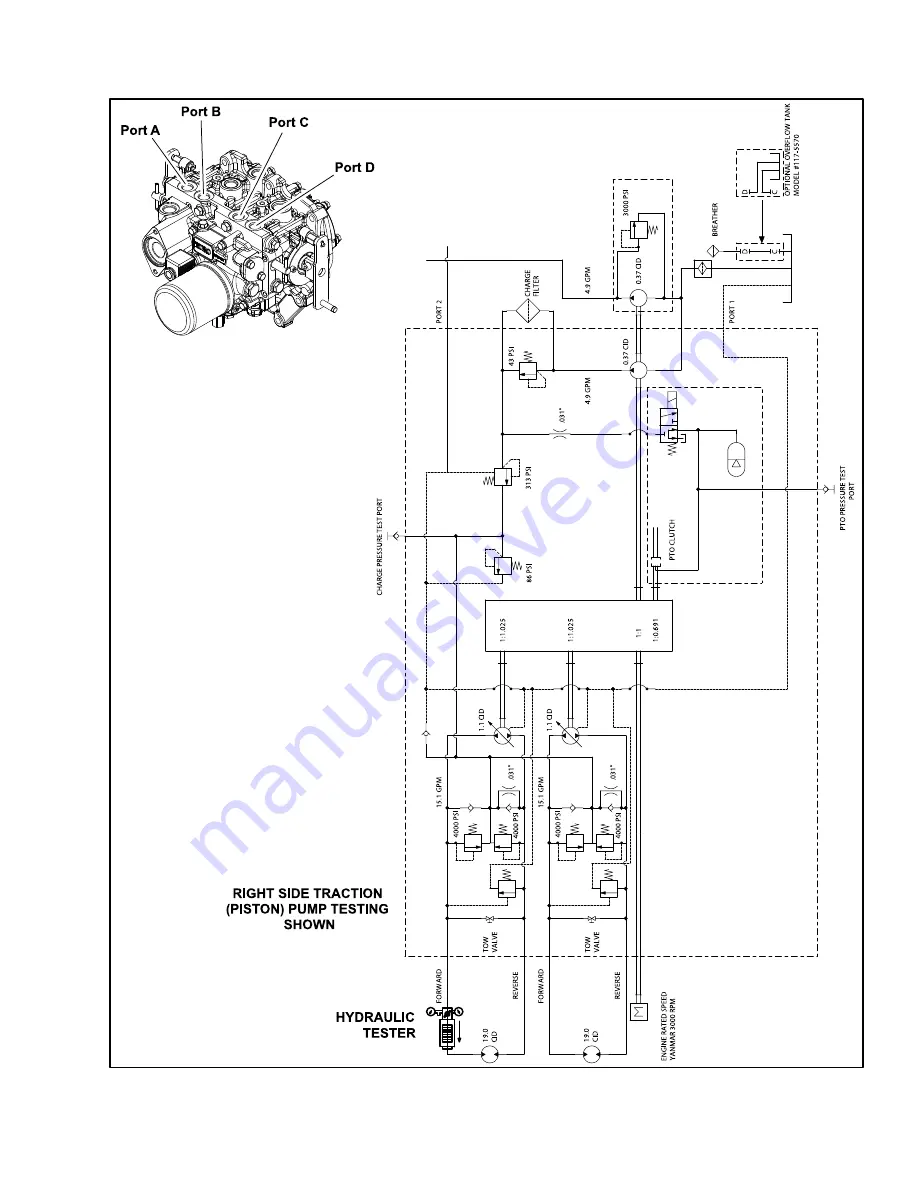
Testing the Transmission Piston Pump Flow (Using Tester with
Pressure Gauges and Flow Meter)
g187022
Figure 41
Groundsmaster 7210
Page 4–37
Hydraulic System: Testing the Hydraulic System
16222SL Rev C
Summary of Contents for Groundsmaster 7210
Page 4: ...NOTES Revision History Page 4 Groundsmaster 7210 16222SL Rev C...
Page 32: ...Specifications and Maintenance Special Tools Page 2 16 Groundsmaster 7210 16222SL Rev C...
Page 60: ...Diesel Engine Service and Repairs Page 3 28 Groundsmaster 7210 16222SL Rev C...
Page 196: ...Hydraulic System Service and Repairs Page 4 136 Groundsmaster 7210 16222SL Rev C...
Page 304: ...Chassis Service and Repairs Page 6 42 Groundsmaster 7210 16222SL Rev C...
Page 327: ...Drawing 105 7260 Rev E Sheet 1 16222SL Rev C Page A 3 Hydraulic Schematic g186843...
Page 328: ...Page A 4 16222SL Rev C Drawing 119 4372 Rev C Sheet 1 Electrical Schematic Platform g186842...
Page 329: ...Drawing 119 4377 Rev C Sheet 1 16222SL Rev C Page A 5 Electrical Schematic Engine g186841...
Page 336: ...Page A 12 16222SL Rev C Drawing 119 4386 Rev A Sheet 1 Wire Harness Drawing Cab Power g186851...
Page 342: ......