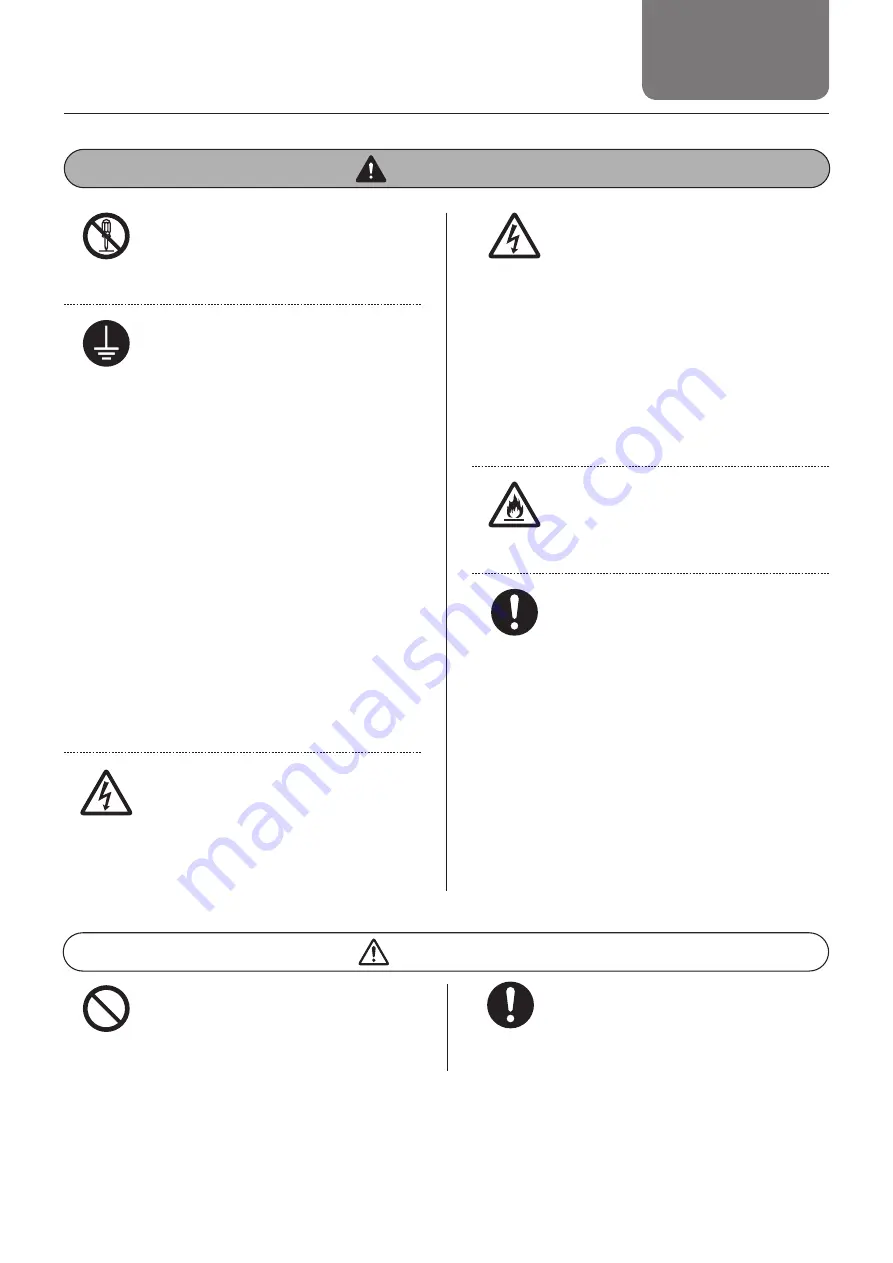
3. Wiring
3-2
TNU
Do not extend or shorten the pro-
vided cables.
Doing so may cause malfunctions or
impair the performance.
Be sure to perform single-point
ground for the FG terminal of this
product.
Connect the grounding electrode
according to the laws, ordinances,
and regulations applied in respec-
tive regions and countries.
Fault or electric leakage may cause an
electric shock.
Do not ground the earth to the fol-
lowing locations:
Gas pipe…Explosion or fire may oc-
cur.
Conductor rod or telephone line…
It poses a danger in the event of
ground discharge.
Water line…It causes an electric
shocks. In addition, the earth does
not function if its middle section is
made of plastic.
Do not change the wiring or re-
move/insert the cables and con-
nectors while the devices are en-
ergized.
Doing so may cause abnormal opera-
tion, fault and electric shock.
Do not
disassemble
Provide
grounding
connection
Do not damage, tuck, place a
heavy object on or apply excessive
stress on the cable.
Doing so may cause an electric shock.
Do not touch the energized parts
within the product.
Doing so may cause an electric shock.
The wiring works must be per-
formed by electric work experts.
Failure to do so may cause an electric
shock.
Be careful to wire the power con-
nectors properly.
Otherwise, fault, fire, or injury may re-
sult.
Perform wiring as described in
this manual.
Otherwise, you may be injured due to
malfunction.
The TACnet cable is not a robot
cable
.
Fix the cable before using it.
Caution –
Flammable
Obligatory
WARNING
1.
How to wire
Caution -
Electrical shock
Caution -
Electrical shock
Do not connect to TNU and TJU or
network devices other than TSC,
TLC, and THC.
Doing so may cause damage or fault.
Do not connect the CN5 (1) pin (S1)
to TSC and TLC.
Doing so may disable the emergency
stop and cause damage or fault.
CAUTION
Prohibited
Obligatory
www.thk.ru
тел. +7(499) 703-39-86