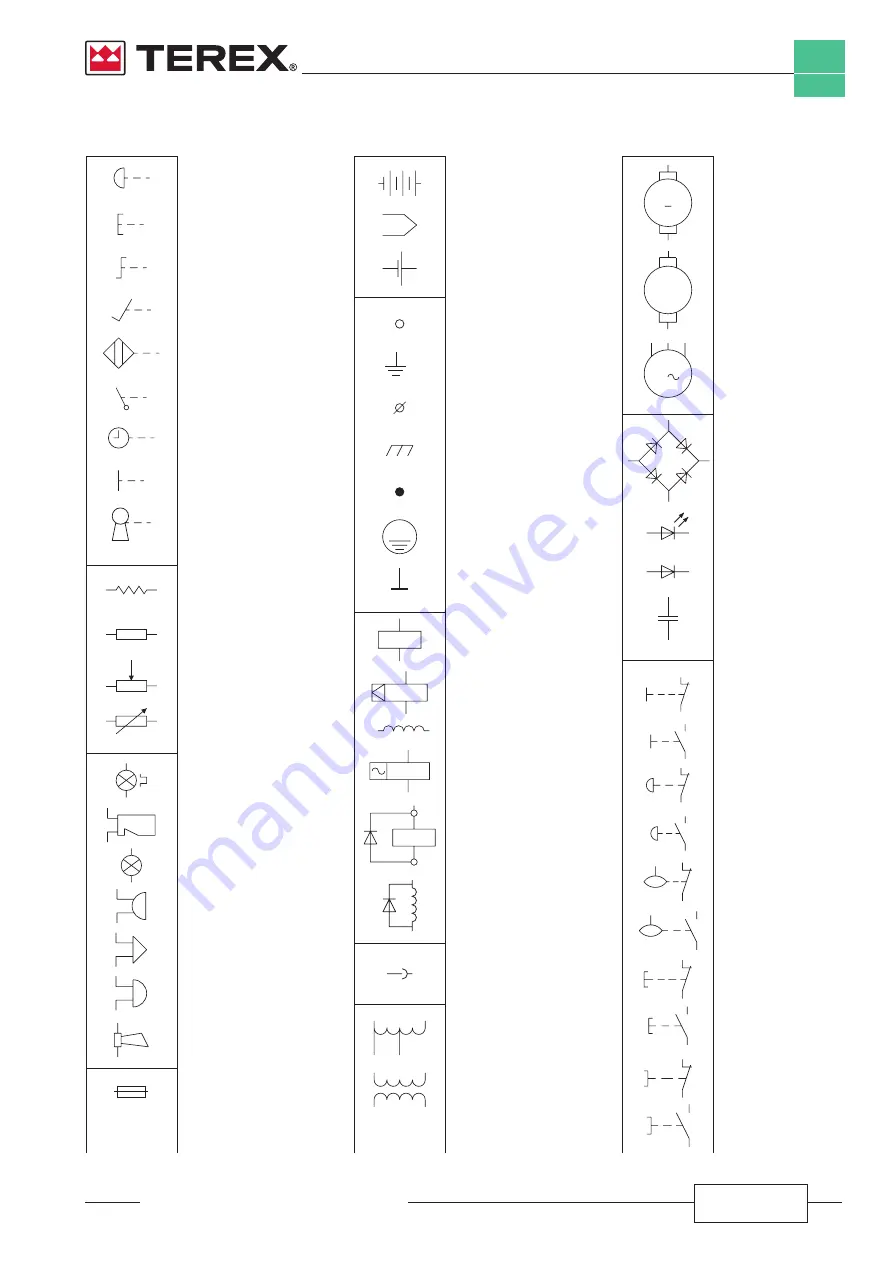
6
9
INDEX
TELELIFT 3713 SX
SCHEMATICS
Document 57.4402.9200 - 1
st
Edition 10/2006
6.
ELECTRICAL SYMBOLS
Emergency controls
ACTUATORS
Pushbutton control
Rotary control
Pedal control
Proximity control
Lever control
Timed control
Mechanical/manual control
Key control
Resistance
RESISTANCES
Resistor
Potentiometer
Variable resistance
Intermittent lamp
SIGNALS
Whistle
Lamp
Buzzer
Siren
Bell
Horn
Horizontal fuse
FUSES AND RELAYS
Relay
Battery
ACCUMULATORS
Thermocouple
Element
Ring
TERMINALS AND GROUNDS
Ground
Terminal
Ground to frame
Knot
Protection ground
Frame ground 2
Coil
COILS
Mechanical coupling coil
Winding
A/C coil
Coil with diode
Winding with diode
Connector
CONNECTORS
Auto-transformer
STATIC APPLICATIONS
Transformer
Motor
DYNAMIC
APPLICATIONS
M
G
Generator
M
3
As_3p_motor
Rectifier
ELECTRONIC PARTS
-
+
Light-emitting diode
Diode
Condenser
Manual NC contact
PUSHBUTTONS
Manual NO contact
NC mushroom-head
pushbutton
NO mushroom-head
pushbutton
NC level
NO level
Pushbutton with NC
return
Pushbutton with NO
return
NC tie-rod
NO tie-rod
Summary of Contents for Telelift 3713 SX
Page 4: ...Courtesy of Crane Market...