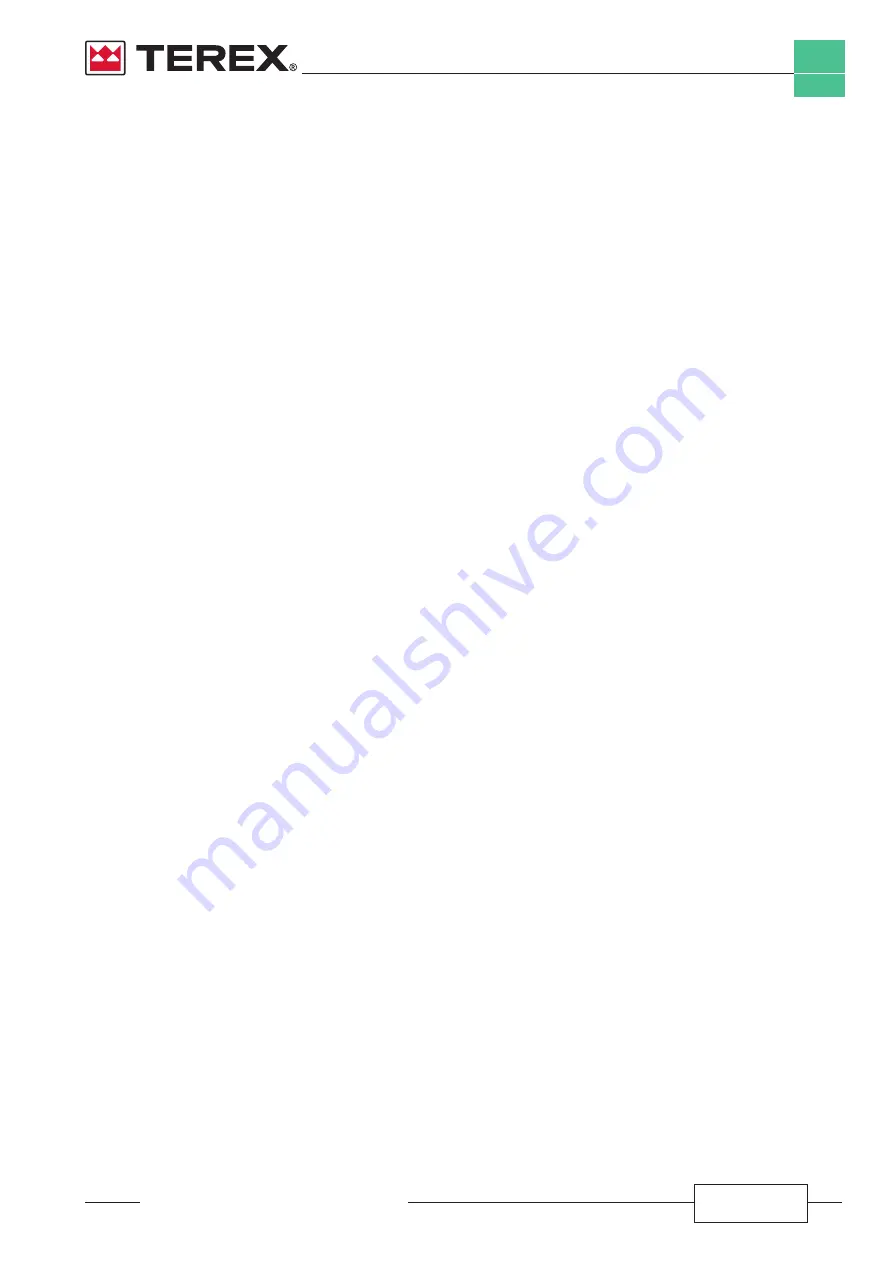
Document 57.4402.9200 - 1
st
Edition 10/2006
INDEX
v
TELELIFT 3713 SX
INTRODUCTION
circuit during the boom lifting/lowering phases and in all
cases of overload on the attachment holding frame (for
instance, in the case of use of the bucket).
Section 2 of the main valve (
1
) controls the telescopic
boom lifting cylinder (
9
) through the longitudinal
displacement of the main lever placed in the driving
cab. This cylinder has one single-acting compensation
valve (
8
) with safety function.
Section 3 of the main valve controls the chassis sway
cylinders (
41
) mounted on the left and right sides of the
machine, anchored to the front axle and equipped with
a double-acting compensation valve (
4
) serving also
as a safety valve, through the lateral displacement of
the special lever installed in the driving place.
Section 4 of the control valve controls the attachment
locking cylinder (
40
) through the lateral displacement of
the special lever placed in the driving place. This cylinder
has a double one-way valve (
9
) with hydraulic release
and safety function. On the feeding lines of this cylinder,
there are two quick-fit connectors for the connection of
the hydraulic lines to the optional attachments which
need hydraulic power for their operation (ex. hydraulic
winch and maintenance jib, mixing bucket, etc.). In
the model dealt with in this manual, this function is
optional.
Section 5 of the main valve controls the left outrigger
cylinder (
4
) equipped with double-acting compensation
valve (
5
) serving also as a safety valve, through the
lateral displacement of the special lever placed in the
driving place.
Section 6 of the main valve controls the right outrigger
cylinder (
6
) equipped with double-acting compensation
valve (
7
) serving also as a safety valve, through the
lateral displacement of the special lever placed in the
driving place.
All the sections of the main valve (
1
) are equipped with
a micro-switch which senses and transmits a special ON/
OFF signal when the relevant slider is activated. Such
signals are used by the operating logic of the system
protecting the machine in case of loss of stability (LMI).
The SAFIM S6 servo-assisted braking system with
pedal (
18
) receives oil from pump (
5
) and uses this oil
to pressurise a hydraulic accumulator (
19
) connected to
the same system. The oil at pressure contained in this
accumulator is then used to operate the service brake
placed inside the front axle (
4
). The fill valve inside
the braking system takes the flow from the feeding line
so the pressure on the accumulator line reaches the
calibration value of the cutout valve set at 150 bar. When
this pressure is reached, the valve gradually releases
all the flow through port B to the radiator fan motor.
The brake pedal installed in the driving place, which
is an integral part of the S6 servo-assisted braking
system, is connected to a slider of proportional type
which controls the service brake line. In relation to the
stroke of this slider, a gradual communication between
Summary of Contents for Telelift 3713 SX
Page 4: ...Courtesy of Crane Market...