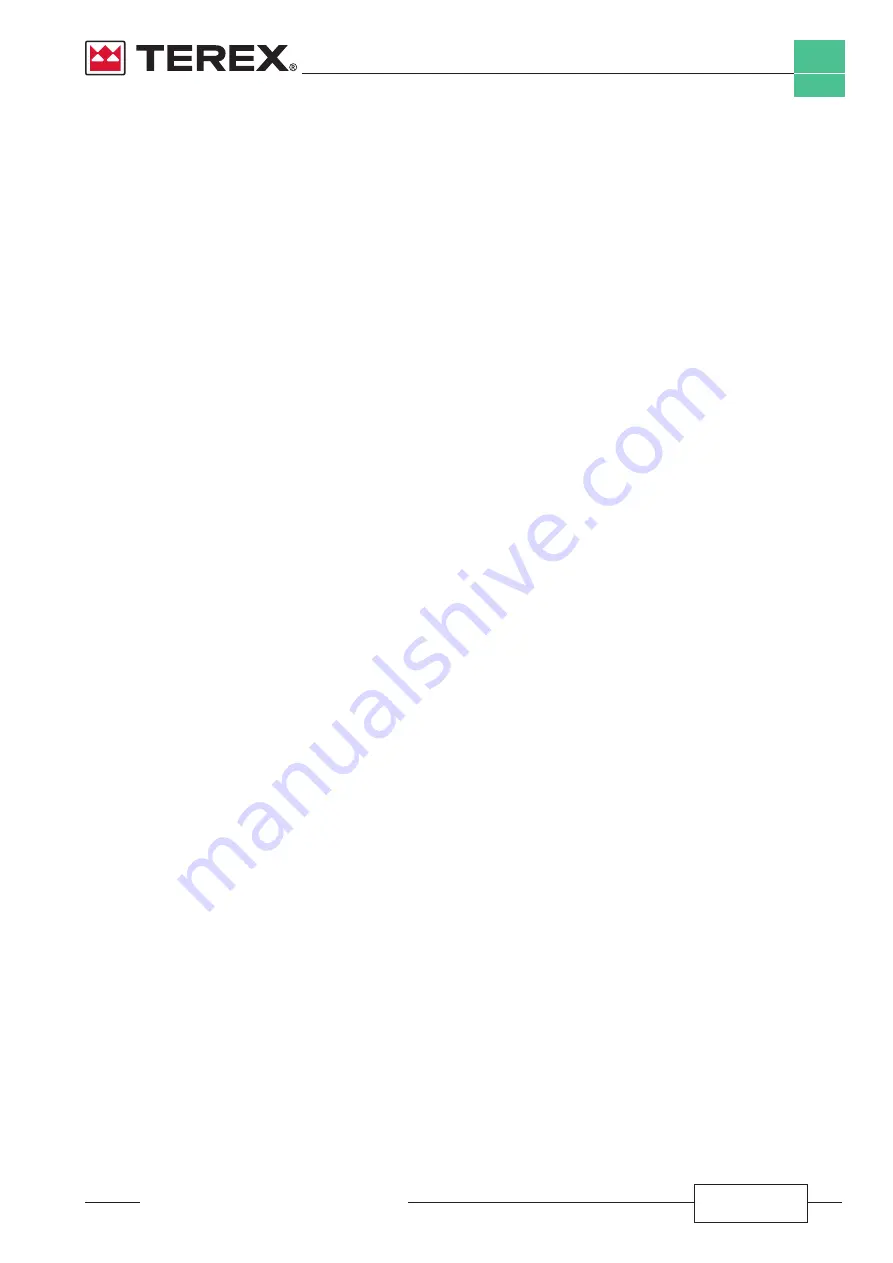
Document 57.4402.9200 - 1
st
Edition 10/2006
INDEX
iii
TELELIFT 3713 SX
INTRODUCTION
cavitation circuit of the automatic fork levelling system.
The hydraulic energy produced by the drive pump (
)
is converted into mechanical power by a closed-loop
hydrostatic motor, model Bosch-Rexroth A6VM107 (
)
equipped with adjustment valve of DA1 type and with
flush valve for reducing the max temperatures inside
the drive circuit. The max displacement of this bent-axis
motor is 107 cm
3
/rev. The motor is directly flanged to
the Dana single-speed reduction gear, which, at its turn,
is directly fixed with brackets to the rear axle (
0
). The
mechanical torque at the gearbox output is transmitted
to the front axle (
4
) and the rear axle (
0
), both model
212 manufactured by Dana, through Cardan shafts.
The hydraulic drive (
14
) of “load sensing” type with
a displacement of 315 cm
3
/rev., receives oil from the
priority line of the pump (
4
) in relation to the “load sensing”
signal sent by the hydraulic drive and connected to such
pump with function of pilot signal.
In this way, the input
flow to the hydraulic drive is exactly the one needed for
the instantaneous steering functions; any excess flow of
the pump is available for the functions of the telescopic
boom.
The steering circuit is protected against input
overpressures by a pressure reducing valve set at 140
bar.
On the two delivery lines to the steering cylinders
there are other two pressure reducing valves with anti-
shock function set at 200 bar.
These two valves are
intended to limit possible shocks on the steering wheel
due to overstress on the steering cylinders. The three
pressure reducing valves are installed in the hydraulic
drive (
14
) and cannot be regulated from the outside.
The steering circuit is completed by the front steering
cylinder (
15
), the rear steering cylinder (
16
) (these
cylinders being integral part of the front axle (
4
) and
the rear axle (
0
) respectively) and by a 4-way/3-
position solenoid valve (
17
) for the selection of the three
different steer modes (rear wheels straight, co-ordinate
front/rear steering and independent front/rear steering).
When the solenoid valve (
17
) is not energised, the front
steering cylinder is fed by the hydraulic drive and the
rear cylinder is blocked. When one magnet or the other
of the solenoid valve (
17
) is energised, the chambers of
the cylinders are connected in a different manner thus
causing the desired effect on the steering mode.
The
Walvoil 6-section valve block of mechanical type (
1
)
receives oil from the secondary line of the pump (
4
)
and feeds all the movements of the telescopic boom,
as well as the outriggers and the chassis sway function.
This monoblock valve is the 6-way type, with oil which
flows through the main valve when the controls are not
activated, and then to the tank. When the mechanical
lever controls are activated, the movement of the main
valve sliders chokes the oil flow, thus producing the
necessary pressure for the control of the activated
function. Each of the 6 sections of the main valve control
a specific function of the machine (lifting/lowering,
attachment holding plate rotation, boom extension/
Summary of Contents for Telelift 3713 SX
Page 4: ...Courtesy of Crane Market...