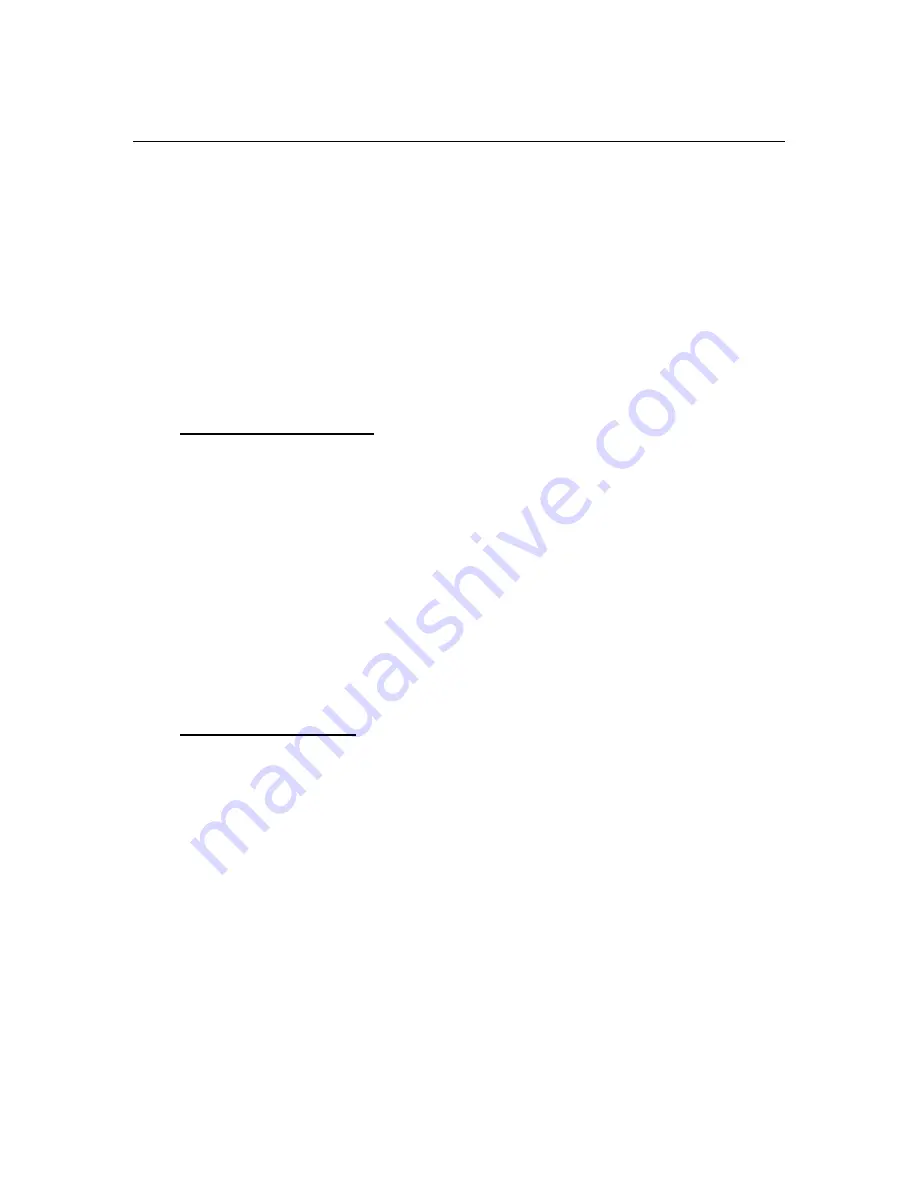
SECTION 9.0, MAINTENANCE
9.0 MAINTENANCE
In the long term, the reliability and accuracy of any continuous monitoring
system depends on the implementation of a conscientious regularly
scheduled maintenance program. If care is taken to perform simple
inspections and take corrective action as required, the Teledyne Monitor
Labs Ultraflow 150 system will provide accurate, reliable data to the user.
9.1 MAINTENANCE SCHEDULE
It must be noted that the conditions under which the monitoring system
operates varies widely from installation to installation. However,
Teledyne Monitor Labs has found the following schedule to be more than
adequate to provide high monitor availability.
9.1.1 After Initial Installation
Teledyne Monitor Labs recommends that the Purge Nozzle Assemblies be
removed from the mounting tubes for visual inspection approximately 30
days after installation and again at 30-day intervals for only the first 3
months of operation. This is a check to see that the purge air being
supplied to the Nozzle Assemblies is adequate and to confirm that the
normal maintenance schedule routine will be sufficient. During these
initial inspections, Teledyne Monitor Labs recommends that the "Teledyne
Monitor Labs Maintenance Check Sheets for the Ultraflow 150" be used
to record the data collected while performing this maintenance. The
“Teledyne Monitor Labs Maintenance Check Sheets for the Ultraflow
150” and Teledyne Monitor Labs “Procedure for Maintenance Check
Sheets for the Ultraflow 150” are located in Appendix B.
9.1.2 Normal Maintenance
Under normal circumstances, Teledyne Monitor Labs recommends that
the maintenance check be performed at least quarterly, but generally not
more often than every two months. The exception to this recommended
schedule would be if the initial inspections performed after installation
revealed that the ambient conditions of the monitor were so adverse that
they require the purge air filters to be changed more frequently.
Extremely dusty conditions in the area of the purge blower will cause the
inlet filter to clog, thus reducing the volume of the protective purge air.
Actual site experience must be used in order to develop an adequate
replacement schedule for the purge air filters.
It should be noted that in performing the maintenance on the flow system
that the monitor may remain on line and collecting data while performing
the check. The exception is when the Purge Nozzle Assemblies are
removed for inspection. Removal of the Purge Nozzle Assemblies will
9-1
Summary of Contents for ULTRAFLOW 150
Page 2: ...DOCUMENT NO 1900 0100 01 REV E ...
Page 24: ...ULTRAFLOW 150 GAS FLOW AND TEMPERATURE MONITOR This page intentionally left blank 4 6 ...
Page 75: ...SECTION 7 0 INSTALLATION This page intentionally left blank 7 7 ...
Page 76: ......
Page 85: ...SECTION 8 0 SYSTEM CALIBRATION AND ADJUSTMENT This page intentionally left blank 8 9 ...
Page 86: ......
Page 89: ...APPENDIX A SITE SPECIFICATION DATA SHEETS ...
Page 90: ...ULTRAFLOW 150 GAS FLOW AND TEMPERATURE MONITOR This page intentionally left blank ...
Page 95: ...APPENDIX B MAINTENANCE CHECK SHEETS ...
Page 96: ... This page intentionally left blank ...
Page 101: ...APPENDIX C SPARE PARTS ...
Page 102: ... This page intentionally left blank ...
Page 105: ......
Page 106: ...APPENDIX D DRAWINGS ...
Page 107: ... This page intentionally left blank ...
Page 108: ......
Page 109: ......
Page 110: ......
Page 111: ......
Page 112: ......
Page 113: ......
Page 114: ......
Page 115: ......
Page 116: ......
Page 117: ......
Page 118: ......
Page 119: ......
Page 120: ......
Page 121: ......
Page 122: ......
Page 123: ......
Page 124: ......
Page 125: ......
Page 126: ......
Page 127: ......
Page 128: ......
Page 129: ......
Page 130: ......
Page 131: ......
Page 132: ......
Page 133: ......
Page 134: ......
Page 135: ......
Page 136: ......
Page 137: ......
Page 138: ......
Page 139: ......
Page 140: ......
Page 141: ......
Page 142: ......
Page 143: ......
Page 144: ...APPENDIX E ENHANCED SERIAL PORT COMMUNICATION PROTOCOL ...