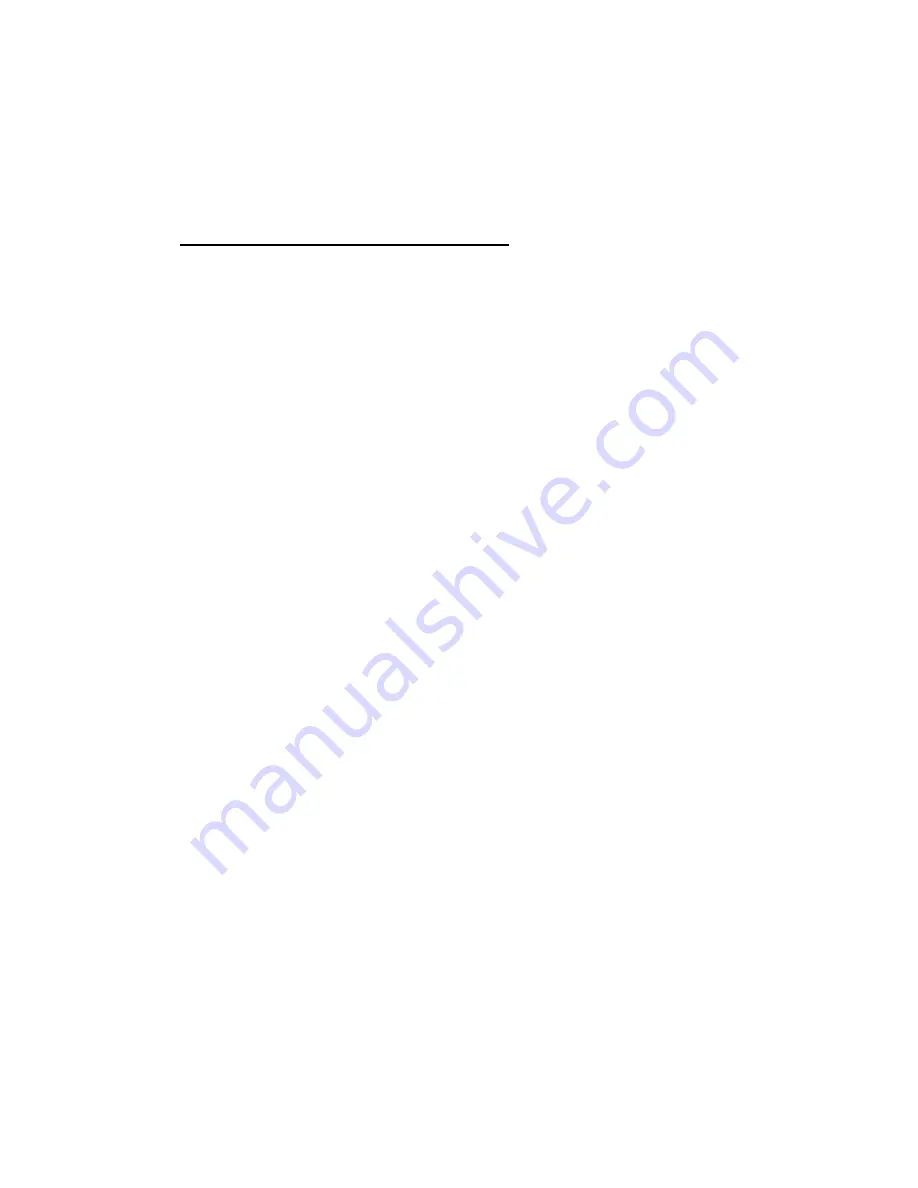
SECTION 7.0, INSTALLATION
the expected life of the purge motor by causing early bearing failure. The
hazards and limitations placed on service personnel would also reduce the
basic reliability of the monitoring system.
7.3 EQUIPMENT MOUNTING CONSIDERATIONS
7.3.1 Flange and Mounting Tube Installation
Installation of the Teledyne Monitor Labs supplied mounting flange and
the user supplied mounting tube is the responsibility of the user. Consult
Teledyne Monitor Labs Drawing ULTRAFLOW 150 FLANGE
INSTALLATION for details. Care must be taken in reporting the
information requested by Teledyne Monitor Labs in the “Ultraflow 150
Installation Guide & Checklist”. This will ensure that sufficient
clearances exist to install and remove the Purge Nozzle Assemblies, which
house the transducers.
Additionally a Mounting Plate Alignment Tool may be purchased to help
maintain acceptable alignment tolerances between the two mounting tubes
during installation of the flange and mounting tubes. Installation of the
mounting tubes is best accomplished by first assembling the mounting
plate and mounting tube as a single unit in a welding shop where adequate
care can be taken to see that the plate and tube are square with one
another. Information on the diameter, length, and angle of the mounting
tubes is given on ULTRAFLOW 150 FLANGE INSTALLATION
drawing. This drawing also contains a number of calculations that must
be performed in order to accurately determine the angle and size of the
penetrations into the stack or duct. The actual penetrations should be
made with some additional clearance so that the prefabricated mounting
tube and plate may be inserted as a unit and temporarily held in place.
Insert one mounting tube first and secure it in place temporarily. Then
install the Mounting Plate Alignment Tool on the mounting plate.
Illuminate the opening on the opposite side of the stack so that it may be
seen through the alignment scope. Then shim or move the mounting tube
until the cross hair of the alignment scope falls in the center of the opening
on the opposite side of the stack. Temporarily secure this tube in place
with a tack weld or other means and then insert the other mounting tube
and plate assembly. Using the same procedures as just mentioned, install
the alignment scope on the second mounting tube and shim in place when
the alignment is correct. After both sides have been checked and require
no additional adjustments, secure both assemblies permanently using
grout, welds or other means appropriate to the particular construction.
On short path length installations (diagonal distances less than 25 feet)
mounting tube misalignment is not generally a critical problem because
the transmitted ultrasonic tone burst is relatively omni directional. As the
path length increases, the issue of signal strength becomes more
7-3
Summary of Contents for ULTRAFLOW 150
Page 2: ...DOCUMENT NO 1900 0100 01 REV E ...
Page 24: ...ULTRAFLOW 150 GAS FLOW AND TEMPERATURE MONITOR This page intentionally left blank 4 6 ...
Page 75: ...SECTION 7 0 INSTALLATION This page intentionally left blank 7 7 ...
Page 76: ......
Page 85: ...SECTION 8 0 SYSTEM CALIBRATION AND ADJUSTMENT This page intentionally left blank 8 9 ...
Page 86: ......
Page 89: ...APPENDIX A SITE SPECIFICATION DATA SHEETS ...
Page 90: ...ULTRAFLOW 150 GAS FLOW AND TEMPERATURE MONITOR This page intentionally left blank ...
Page 95: ...APPENDIX B MAINTENANCE CHECK SHEETS ...
Page 96: ... This page intentionally left blank ...
Page 101: ...APPENDIX C SPARE PARTS ...
Page 102: ... This page intentionally left blank ...
Page 105: ......
Page 106: ...APPENDIX D DRAWINGS ...
Page 107: ... This page intentionally left blank ...
Page 108: ......
Page 109: ......
Page 110: ......
Page 111: ......
Page 112: ......
Page 113: ......
Page 114: ......
Page 115: ......
Page 116: ......
Page 117: ......
Page 118: ......
Page 119: ......
Page 120: ......
Page 121: ......
Page 122: ......
Page 123: ......
Page 124: ......
Page 125: ......
Page 126: ......
Page 127: ......
Page 128: ......
Page 129: ......
Page 130: ......
Page 131: ......
Page 132: ......
Page 133: ......
Page 134: ......
Page 135: ......
Page 136: ......
Page 137: ......
Page 138: ......
Page 139: ......
Page 140: ......
Page 141: ......
Page 142: ......
Page 143: ......
Page 144: ...APPENDIX E ENHANCED SERIAL PORT COMMUNICATION PROTOCOL ...