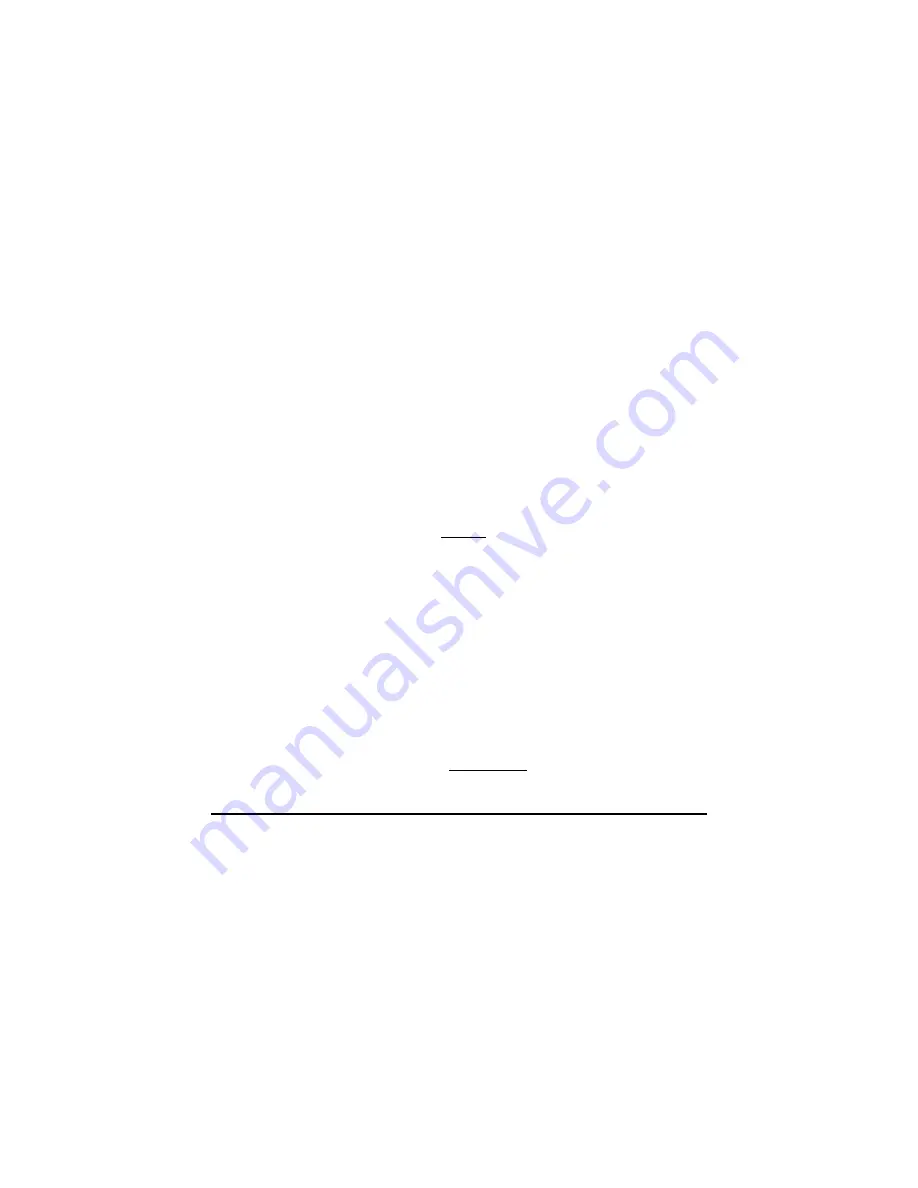
Appendix E, Enhanced serial port communication protocol
ENHANCED SERIAL PORT COMMUNICATION PROTOCOL
This enhanced serial port protocol is only available with Enhanced Remote Panel 332 version
1.10 or later.
A short description of the original communication is described in the Enhanced Remote Display
section of the manual. It explains how to use the simple commands which use a question mark
symbol (?) or a dollar sign symbol ($) to request information from the RS232 or RS422/485
ports of the Enhanced Remote Panel. This is still a valid form of communication with either of
these ports. The configuration of the serial ports are still fixed at 9600, 8 bits, no parity, two stop
bits.
Although the original type of communication is very simple, it has some drawbacks. One of
these shortcomings is the fact that there is no data validation within the structure of the protocol
and as a result, characters could be lost from time to time.
As more customers requested the ability to acquire data serially from our instruments for their
Data Acquisition and Handling Systems, we went back to the format used on some of the older
equipment designed by our engineers. It consists of four values separated by commas ending in
a ‘Carriage-Return’ and ‘Line-Feed’. The first and third values must match exactly. The second
and fourth values must also match exactly. If
either
of these two conditions are not met, then the
Enhanced Remote Panel will ignore the data stream as an input. In a similar manner, a DAS
should ignore any data streams which do not have matching pairs.
A typical command or data stream would look like the following:
“first value”, “second value”, “first value repeated”, “second value repeated”<CR> <LF>
There are two types of functions which can be sent to the Enhanced Remote Panel using this
format. One function is a more robust and error free way in which to request data. The other
function is the ability to command and control calibrations and initiate other modes of operation.
It is important to note that program parameters
CANNOT
be modified from the serial ports.
MATCHED PAIR DATA REQUEST PROTOCOL FOR A DAS
To request data in the matched pair format, use the following command line:
990 “variable number”, 990, “variable number”<CR> <LF>
The “variable number” is the same number designation used to number the variables in the
original protocol. A list of the variable numbers can be obtained from the Enhanced Remote
Panel by using the original 255? command. An example is included later in this appendix.
E-1
Summary of Contents for ULTRAFLOW 150
Page 2: ...DOCUMENT NO 1900 0100 01 REV E ...
Page 24: ...ULTRAFLOW 150 GAS FLOW AND TEMPERATURE MONITOR This page intentionally left blank 4 6 ...
Page 75: ...SECTION 7 0 INSTALLATION This page intentionally left blank 7 7 ...
Page 76: ......
Page 85: ...SECTION 8 0 SYSTEM CALIBRATION AND ADJUSTMENT This page intentionally left blank 8 9 ...
Page 86: ......
Page 89: ...APPENDIX A SITE SPECIFICATION DATA SHEETS ...
Page 90: ...ULTRAFLOW 150 GAS FLOW AND TEMPERATURE MONITOR This page intentionally left blank ...
Page 95: ...APPENDIX B MAINTENANCE CHECK SHEETS ...
Page 96: ... This page intentionally left blank ...
Page 101: ...APPENDIX C SPARE PARTS ...
Page 102: ... This page intentionally left blank ...
Page 105: ......
Page 106: ...APPENDIX D DRAWINGS ...
Page 107: ... This page intentionally left blank ...
Page 108: ......
Page 109: ......
Page 110: ......
Page 111: ......
Page 112: ......
Page 113: ......
Page 114: ......
Page 115: ......
Page 116: ......
Page 117: ......
Page 118: ......
Page 119: ......
Page 120: ......
Page 121: ......
Page 122: ......
Page 123: ......
Page 124: ......
Page 125: ......
Page 126: ......
Page 127: ......
Page 128: ......
Page 129: ......
Page 130: ......
Page 131: ......
Page 132: ......
Page 133: ......
Page 134: ......
Page 135: ......
Page 136: ......
Page 137: ......
Page 138: ......
Page 139: ......
Page 140: ......
Page 141: ......
Page 142: ......
Page 143: ......
Page 144: ...APPENDIX E ENHANCED SERIAL PORT COMMUNICATION PROTOCOL ...