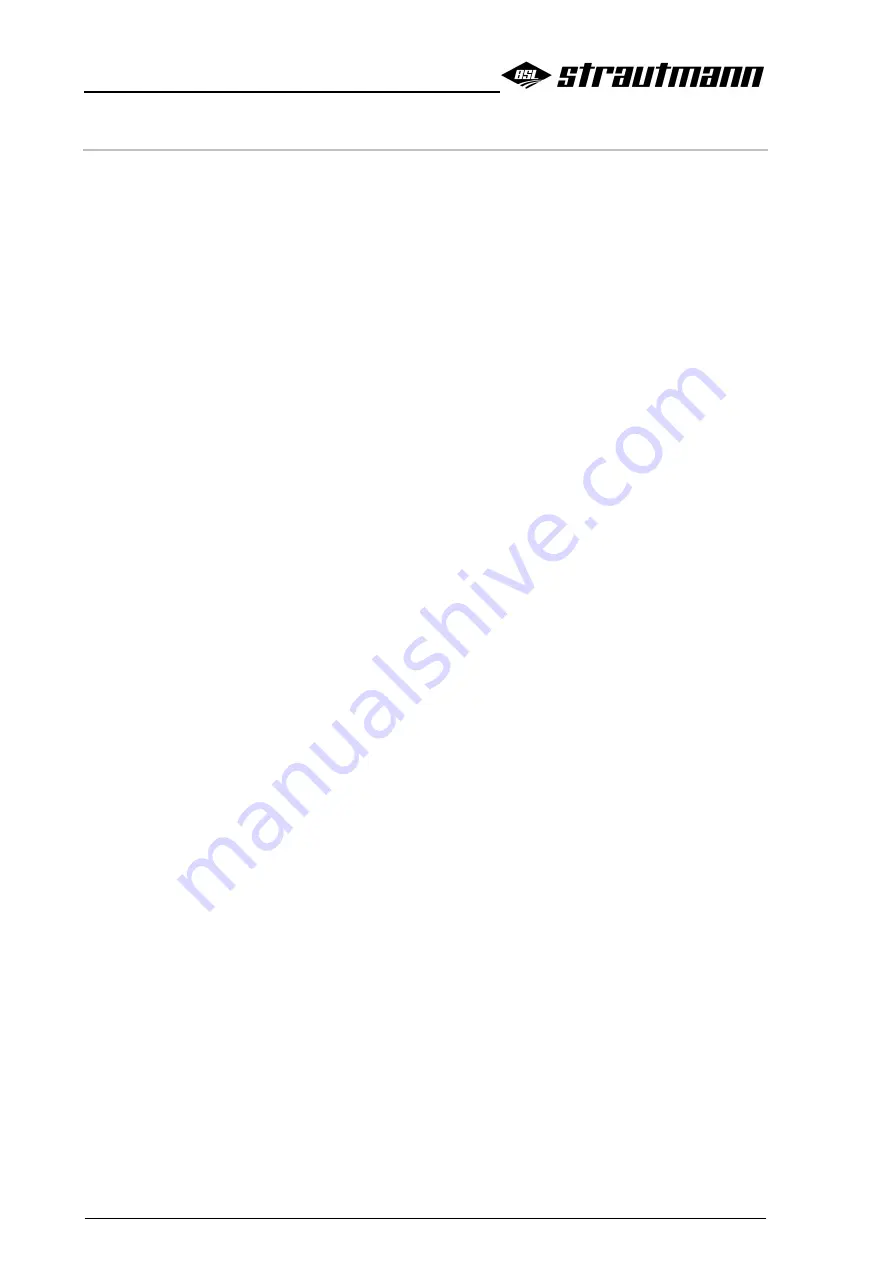
Foreword
4
Verti-Mix 951-1651, Verti-Mix 951-L, 1251-L, Verti-Mix 1501 D-3101 D 05.16
Foreword
Dear customer,
You have decided in favour of a quality product from the large B. Strautmann & Söhne GmbH u. Co.
KG product range. We thank you for the confidence you have shown in us.
Upon receipt of the machine, please check for transport damage or missing parts! Check the delivered
machine for its completeness, including the ordered optional extras, by means of the delivery note.
Only immediate complaints will give reason to compensation!
Read and observe these operating instructions and any other included operating instructions for
individual machine components before the first start-up; in case of doubt, the details and information
contained in such sub-supplier documentation shall prevail! In particular observe the safety
instructions, thus being able to fully benefit from the advantages of your recently acquired machine.
Please make sure that all operators of the machine have read these operating instructions before
starting the machine.
The machines are available with various optional extras. Due to the individual equipment of your
machine, not all descriptions included in these operating instructions apply to your machine. Optional
extras are marked in these operating instructions and are available at extra cost.
In case of any inquiries or problems, please refer to these operating instructions or call us.
Regular service and maintenance and timely replacement of worn-out or damaged parts will result in a
longer service life of your machine.