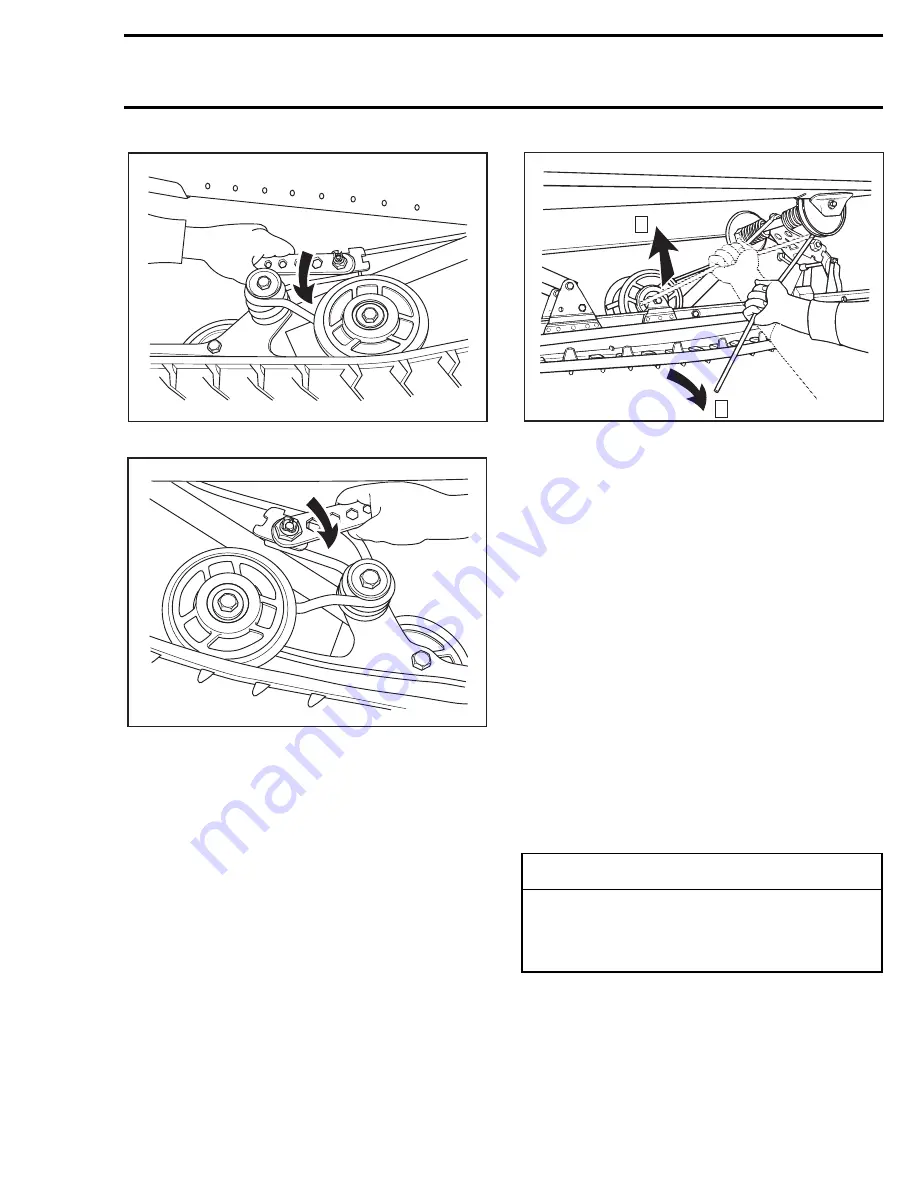
Section 07
REAR SUSPENSION
Subsection 02
(TORQUE REACTION SUSPENSION)
07-02-5
RH SIDE
LH SIDE
NOTE:
To quickly change rear cam position with-
out using any tool:
– Lay vehicle on its side.
– Unhook rear spring by hand from lower idler
wheel.
– Turn adjustment cam by hand to the desired po-
sition.
– Reinstall spring on its support making sure that
it sits in the groove of support.
Stopper Strap
The function of the stopper strap is to control the
transfer of vehicle weight during acceleration and
to control track lead angle.
The longer the belt, the more the weight will be
transferred to the track to provide a better trac-
tion. The shorter the belt, the lesser the weight
transferred to the track, thus maintaining a more
positive steering.
The longer the belt, the greater will be the track
lead angle. A shorter belt will reduce track lead
angle which may help when negotiating a particu-
lar snow condition.
Adjusting holes on the stopper strap allow to ad-
just it according to driver’s requirements, field
and/or snow conditions.
A05F0OA
A05F0PA
-
CAUTION
Whenever stopper strap length is changed,
track tension must be readjusted to prevent
any possibility of operating vehicle with a
too loose or too tight track tension.
A05F0FA
1
2
Summary of Contents for Formula S 1998
Page 1: ......
Page 2: ...1998 Shop Manual VOLUME 1 TUNDRA II LT TOURING E LE FORMULA S S ELECTRIC SL SKANDIC 380 500...
Page 314: ...TUNDRA II LT ANNEX 1...
Page 315: ......
Page 316: ......
Page 317: ......
Page 318: ...SKANDIC 380 500 ANNEX 2...
Page 319: ......
Page 320: ......
Page 321: ......
Page 322: ......
Page 323: ...FORMULA S ANNEX 3...
Page 324: ......
Page 325: ......
Page 326: ......
Page 327: ......
Page 328: ...FORMULA SL ANNEX 4...
Page 329: ......
Page 330: ......
Page 331: ......
Page 332: ......
Page 333: ...TOURING E LE FORMULA S ELECTRIC ANNEX 5...
Page 334: ......
Page 335: ......
Page 336: ......
Page 337: ......
Page 338: ......