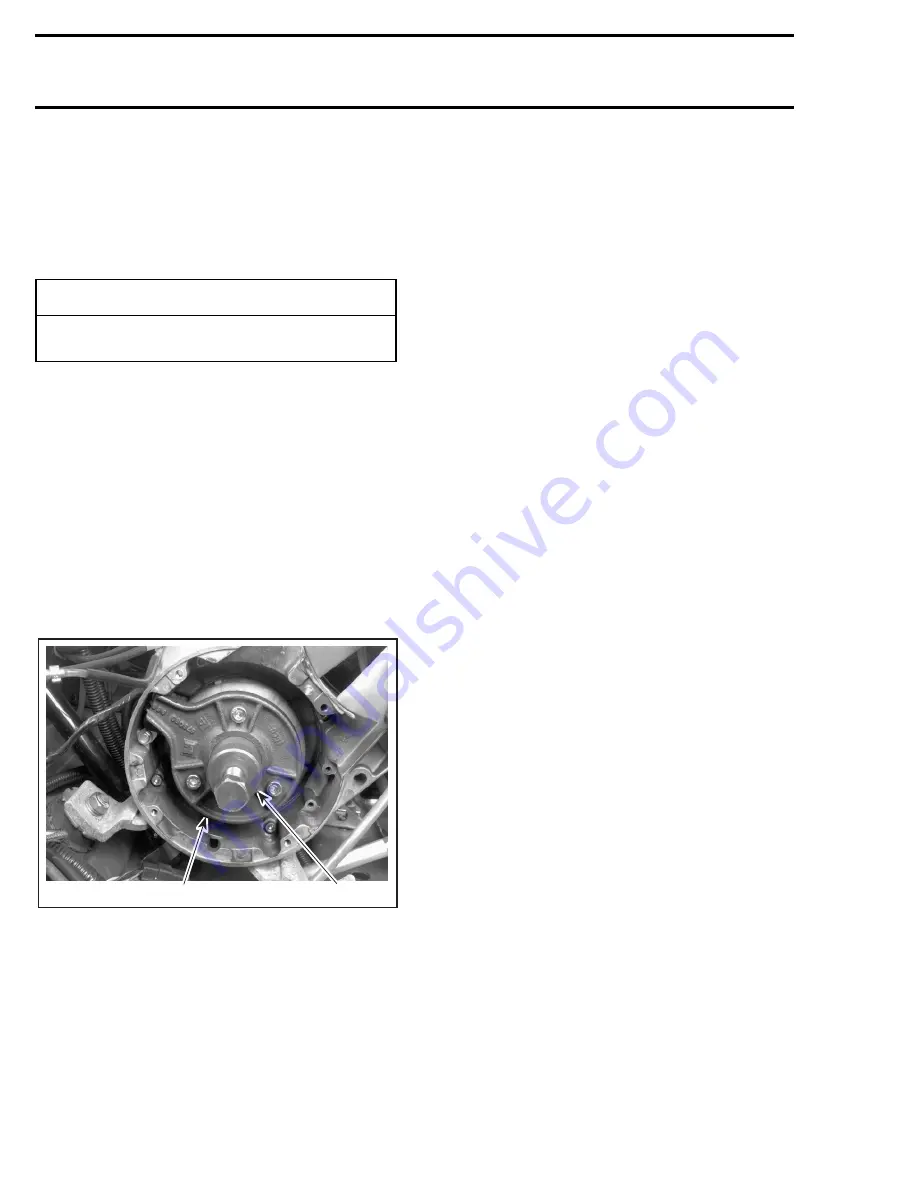
Section 04
ENGINE
Subsection 05
(CDI SYSTEM)
04-05-6
NOTE:
The following procedures can be done
without removing the engine from chassis.
CLEANING
Clean all metal components in a non-ferrous met-
al cleaner.
DISASSEMBLY
To gain access to magneto assembly, remove the
following parts as needed on different engines:
– tuned pipe and muffler
– oil injection pump mounting plate from rewind
starter
– rewind starter
– starting and V-belt pulleys
NOTE:
Before disassembling armature plate, in-
dexing marks should be scribed to facilitate reas-
sembly.
To remove magneto flywheel retaining nut
no. 3
,
install puller ring (P/N 420 8760 80) and M8 x 20
screws.
– Remove magneto flywheel nut, using a 30 mm
socket machined to 40 mm (1.580 in) outside
diameter by 16 mm (5/8 in) long.
NOTE:
To correctly remove a threadlocked fas-
tener it is first necessary to tap on the fastener to
break threadlocker bond. This will eliminate the
possibility of thread breakage.
To remove magneto flywheel
no. 2
, install the
magneto puller (P/N 529 0225 00).
– Tighten puller bolt and at the same time, tap on
bolt head using a hammer to release magneto
flywheel from its taper.
REPAIR
To replace generator coil
no. 1
:
– Heat the armature plate to 93°C (200°F) around
the screw holes to break the threadlocker
bond.
To replace trigger coil
no. 4
:
– Disconnect trigger coil wire (RED).
– Remove grommet from crankcase where trig-
ger coil wire exits magneto housing.
– Remove retaining screws
no. 9
.
– Remove trigger coil and carefully pull wire.
– Install new trigger coil and other parts re-
moved.
Adjustment
Whenever the trigger coil or the magneto fly-
wheel is removed or replaced, the air-gap be-
tween the trigger coil and the flywheel protrusion
must be checked and adjusted. The purpose of
this adjustment is to obtain the minimum clear-
ance between these parts — without touching at
any RPM — so that the trigger coil produces its
proper electrical output. Ignition timing must also
be checked.
Proceed as follows:
1. Rotate flywheel so that one protrusion aligns
with trigger coil.
2. Using a feeler gauge of 0.45 mm (.018 in) to
0.55 mm (.022 in) thick, check air-gap between
center pole of trigger coil and flywheel protru-
sion.
3. If necessary, adjust by slackening retaining
screws and moving trigger coil toward or away
of protrusion.
4. Retighten screws and recheck air-gap.
-
CAUTION
Clean armature and magneto using only a
clean cloth.
A03C07A
529 0225 00
420 8760 80
Summary of Contents for Formula S 1998
Page 1: ......
Page 2: ...1998 Shop Manual VOLUME 1 TUNDRA II LT TOURING E LE FORMULA S S ELECTRIC SL SKANDIC 380 500...
Page 314: ...TUNDRA II LT ANNEX 1...
Page 315: ......
Page 316: ......
Page 317: ......
Page 318: ...SKANDIC 380 500 ANNEX 2...
Page 319: ......
Page 320: ......
Page 321: ......
Page 322: ......
Page 323: ...FORMULA S ANNEX 3...
Page 324: ......
Page 325: ......
Page 326: ......
Page 327: ......
Page 328: ...FORMULA SL ANNEX 4...
Page 329: ......
Page 330: ......
Page 331: ......
Page 332: ......
Page 333: ...TOURING E LE FORMULA S ELECTRIC ANNEX 5...
Page 334: ......
Page 335: ......
Page 336: ......
Page 337: ......
Page 338: ......