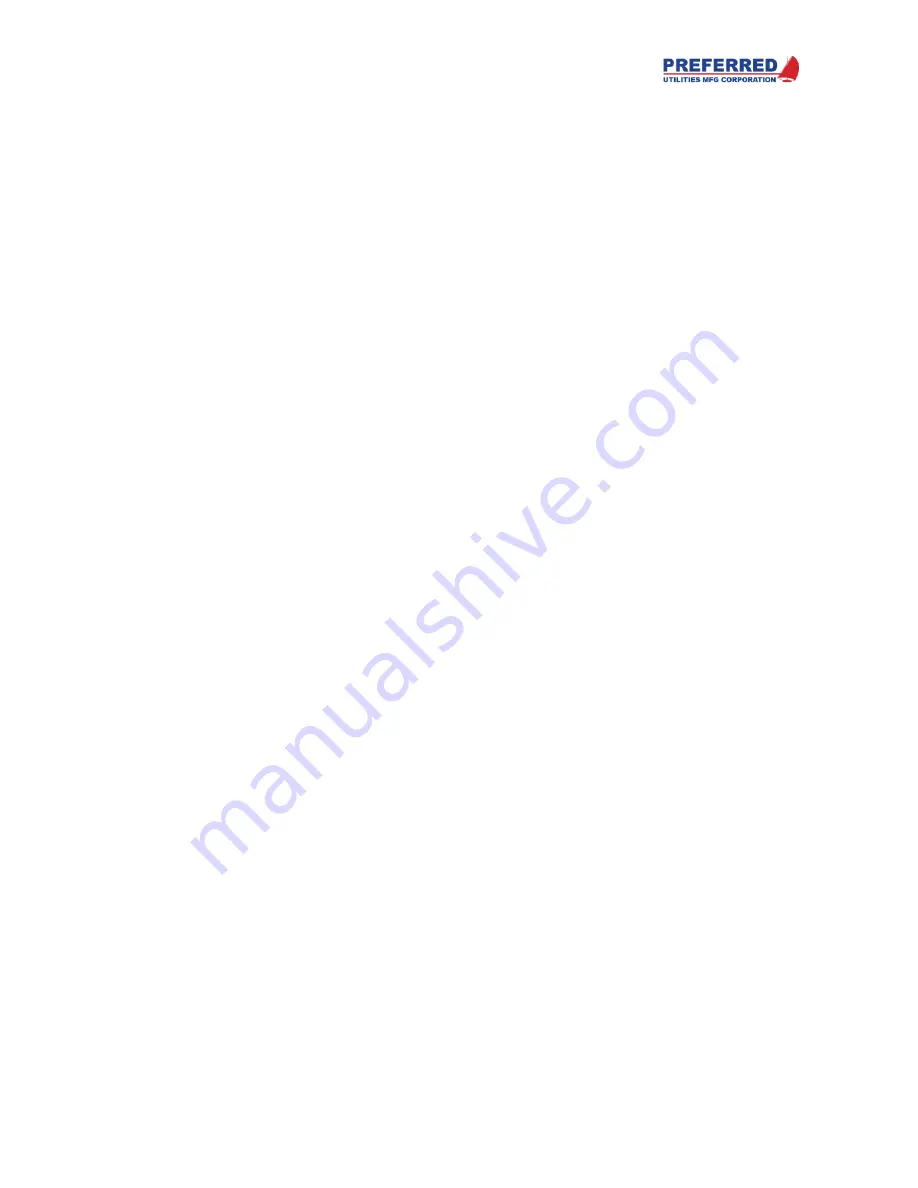
PCC-IV Instruction Manual (Rev. 0.1)
Page 6-27
Section 6
– Blockware Functions
Technical Reference
NOTES:
1. The Track Input signal is used during Track or Override modes to force the value of the PID Integral term.
This Input is used to provide bumpless transfer. See above for details.
2. The Feed Forward Input is added to the result of the PID calculation before the Output Min/Max limiting
logic. This prevents Integral Term Reset Windup.
3. The Adaptive Gain Input is ignored for PID types 1 and 2 (see Parameter 10). Negative Input values are set
equal to 0.00%, Inputs greater than +327.00% are set equal to +327.00%. The PID Gain (Parameter 1) is
multiplied by the Adaptive Gain Input divided by 100.00%.
Example: Gain = 15.0, and the Adaptive Gain Input = 25.00%, the effective PID gain would be 3.75.
4. The three Track Mode Inputs are logically OR’d together. If any one of the three Inputs equals “1”, AND
Repeats/Min > 0, then the Block Output is forced to equal the Track Signal Input. This is accomplished by
forcing the PID Integral term to counteract the Proportional, Derivative, and Feed Forward terms. If all three
Track Mode Inputs equal “0”, the normal PID calculation determines the Output.
5. When the Override Input = “1”, AND the PID is NOT in Track Mode, AND Repeats/Min > 0, the PID Integral
term is set equal to the Track Signal Input. This feature is used to provide bumpless transfer when Override
(i.e. Constraint) control strategies are utilized. See Example in the Configuration section. Track mode has
priority over Override mode.
6. The Setpoint Filter is used to prevent abrupt PID Output changes due to setpoint changes. When the filter =
1.000, the filter time constant (in seconds) is: (60 / (Integral Repeats/Min)), Parameter 2 determines the
Repeats/Min. The filtering effect is proportionately less as the Setpoint Filter parameter is reduced. Example:
Setpoint Filter = 0.90, Repeats/Min = 0.75; therefore, the filter time constant is 72 seconds.
Note: If Parameter 2 = 0.01 repeats/min, and setpoint filter = 1.00, the filter time constant is 6000 seconds!
Note: When Parameter 2 = 0.00 (i.e. Reset turned OFF), the filter time constant is 60 seconds when the setpoint
filter = 1.00. Setpoint filter values less than 1.00 reduce the time constant proportionately.
The Setpoint filter must be turned OFF for full metering combustion fuel and airflow PID loops, and for
cascade control inner loops (i.e. three-element feedwater flow loop).
7. The Maximum Output limit must be greater than the Minimum Output limit (Parameters 5 and 6).
8. For P or PD modes (i.e. Repeats/min=0.0, I term is Off), the PID Output equals the mid-point of the Maximum
and Minimum Output Parameters when PV=SP. For Example: the mid-point is 50% for 0-100% Output range,
100% for 50-150%, 75% for 50-100%, … Neither Track Mode nor Override Mode will activate if
Repeats/Min = 0.0.
9. In applications when Repeats/min=0.0 (i.e. I term is Off), it is not always desirable for the PID Output to be
at the midpoint when PV=SP (see note 8). Examples: some batch processing, level control, and pressure relief
valves. Output Bias adds/subtracts to/from the standard PID midpoint Output, but the Output is still limited
by the Min/Max Output Parameters. If Output Bias is non-zero when Repeats/min > 0, serious system
oscillations can occur due to Reset Windup.
10. Reverse action means that the PID Output decreases when the process variable Input increases above setpoint.
Direct action causes the Output to increase when the process variable increases above setpoint.
11. “Derivative Action = PV” (Parameter 10 = 0) avoids abrupt PID Output changes due to setpoint changes,
since the derivative only responds to changes of the PV Input. “Derivative Action = Error” (Parameter 10 =
1) is generally only used in the inner loop of cascaded PID loops.
12. Gap PID provides an error zone on either side of the setpoint with reduced (or zero) gain. This feature is
useful with noisy signals such as boiler furnace pressure, and with non-linear processes such as pH control
loops. Gap Band (Parameter 11) determines setpoint deviation band within which the reduced gain is applied.
The Gap Gain Multiplier (Parameter 12) numerically multiplies the normal PID Gain (Parameter 1) within the
Gap Band. Gap Gain can be set equal to 0. Outside the Gap band the normal PID Gain remains the same, but
the error is automatically biased down for a smooth transition (see figure above). Gap Parameters 11 and 12
are ignored for PID types 1 and 3 (see Parameter 9).