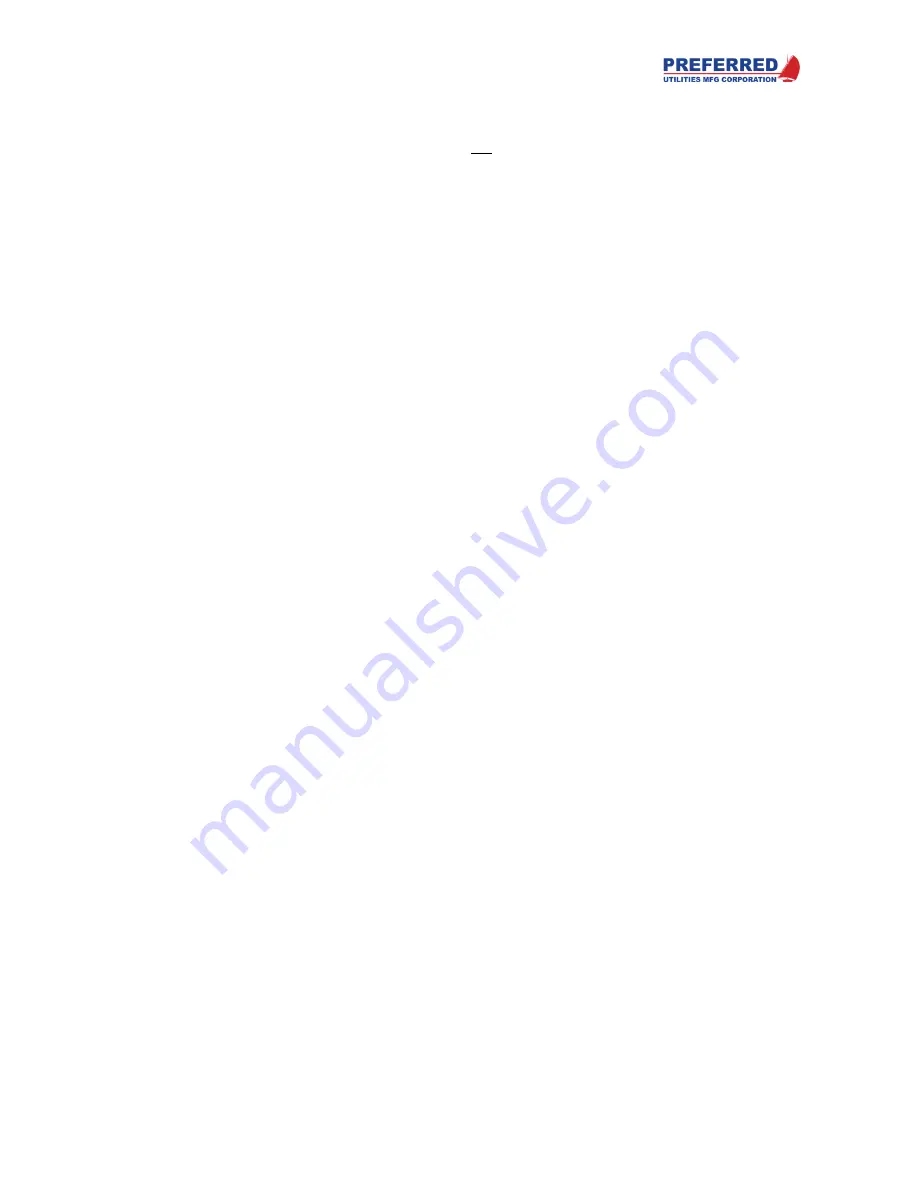
PCC-IV Instruction Manual (rev. 0.2)
Page 5-18
Section 5 – Configuring Blockware
Test the configuration
Read
Section 4
before testing. This section explains how to use the “Force” and “Examine” features of the
PCC-IV’s Brows Blocks Menu.
The PCC-IV should not be performing any control Function while being
tested. Each Block that was added or was modified should be thoroughly checked prior to returning
the PCC-IV to process control
.
To test the configuration:
•
Write the new Blockware to the PCC-IV and verify there are no errors. The green RUN LED should
be solid green after sending the configuration
•
Display “PM Demand.” Compare the numeric display to that of the Plant Master Output. If they do
not match, check engineering units in the Panel Data Screen and check parameters of B5 (AIN).
•
Display “PM Bias.” Using the
▲
and
▼
soft-buttons run the Bias all the way up and all the way
down to verify the display ranges from -50% to +50%. Set the Bias to -10%. Using the PCC-IV’s
Brose Blocks Menu, force the Plant Master Input (B5) to 50% or, if possible, base load the Plant
Master at 50%. Examine B26. It should read 40%. If not, check the Inputs and parameters of Blocks
5, 25, and 26.
•
Press the Local/Remote Pushbutton to toggle the control mode. The LED, PV, and SP bargraphs
should toggle accordingly. If not, check the Inputs and/or parameters of Blocks 55 (PB) & 85 (LED).
Place in Local PID mode.
•
Place the controller in the Local PID mode. Force the Drum Pressure Input (B4) to 0%. A “Low PIS”
Alarm should annunciate. Acknowledge the alarm (press “ACK”) and check the verbiage on the
annunciator display. Correct if necessary. Note: A 4-20 ma simulator can be used as the Input in
lieu of forcing the Block.
•
Force the Drum Pressure Input to 100%. A “High PSI” Alarm should annunciate. Acknowledge the
alarm and check the verbiage on the display. Correct if necessary.
•
Unforce all Blocks
•
Force the output of Block 40 to zero to allow adjustment of the Analog Output.
•
Place the controller into Auto and select Remote mode.
•
Set the Bias to zero.
•
Force Block 5 to various settings and verify the output of the controller, B150 (AOUT), follows Plant
Master Demand. The PV and SP bargraphs should be equal and follow Plant Master Demand.
•
Adjust the Bias and verify the output of the controller, B150 (AOUT), follows Plant Master Demand
+/- the Bias accordingly. The SP bargraph should be offset by the Bias value.
•
Place the controller into Local mode.
•
Adjust the Drum PSI Setpoint to various settings. The SP bargraph should follow accordingly.
•
Force the Drum PSI input, Block 4 (AIN), above or below the Drum PSI Setpoint. The output of the
controller should react inversely. The PV bargraph should follow the Drum Pressure accordingly.
Place the controller into operation
If all the above tests were successful, you are ready for operation. Once in operation you should check the
tuning (Gain, Integral, etc.) of the Drum Pressure PID control loop and adjust if necessary.