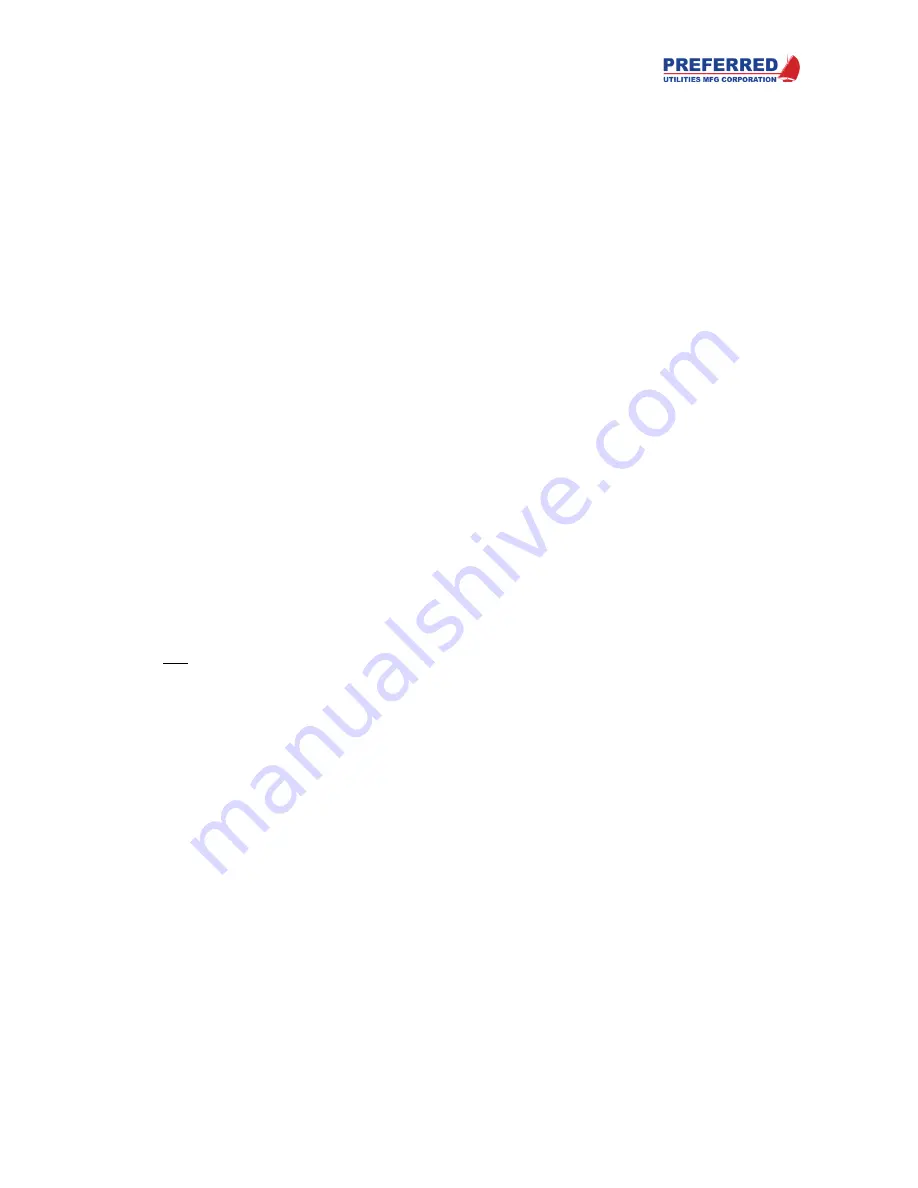
PCC-IV Instruction Manual (rev. 0.2)
Page 5-16
Section 5 – Configuring Blockware
Modify Parameters as required
See Section 6 for a complete description of every block parameter
Block 5 AIN:
There are seven parameters that can be configured. In many cases the default value will be used. However,
some parameters need to be modified to suit the needs of the desired Control Strategy.
•
P1 – Option Board 0 since the CPU board input is being used
•
P2 – Input Channel 2 as the second analog input channel is being used
•
P3 – Volts for 0% is 1.000 as this will be a 1-5 Vdc signal
•
P4 – Volts for 100% is 5.000 as this will be a 1-5 Vdc signal
•
P5 – Sq. Root Option is 0 as we do not want to square root the signal
•
P6 – Filter Seconds 1.0 as this will eliminate noise or sharp spikes
•
P7 – Low Flow Cutoff is 0.00 as this is not required
Block 25 FPCON:
We need a Front Panel Constant to adjust/display our Submaster Bias. We will setup a +/- 50% bias adjustment
range.
•
P1 – Min Output is -50.00
•
P2 – Max Output is 50.00
Block 26 WSUM:
We want to apply the positive or negative Submaster Bias to the Plant Master signal. We will setup the WSUM block
as “A + B” with Input A as the Plant Master signal and Input B as the +/- Bias signal.
•
P1 – K1 is 1.000 as we are not scaling the input
•
P2 – K2 is 1.000 as we are not scaling the input
•
P3 – K3 is 1.000, it is not used in this application
•
P4 – K4 is 0.00, it is not used in this application
Block 55 PB:
We need to add a pushbutton to select Local PID or Remote Plant Master control.
•
P1 – Pwr Up Mode is 3 as we want the button to power up in its last mode of operation
Block 59 HIALM:
We will assume the Plant Master has a high and low header pressure alarm. We want high and low drum pressure
alarms only when in Local PID mode.
•
P1 – SP Mode is 2 as we want an internal setpoint
•
P2 – % Deadband is 1.00 as we want 1% of the Drum Pressure transmitter’s full-scale range to be our
deadband (i.e. a 0-200 PSI transmitter would have a dead band of 2 PSI).
•
P3 – is 70.00 as we want 70% of the Drum Pressure transmitter’s full-scale range to give us a high alarm
(i.e. a 0-200 PSI transmitter would alarm above 140 PSI).
•
P4 – Disable Hi/Lo is 1 so that the alarm is disabled when the PB is high
•
P5 – Delay Sec of 60. We want a 60 second delay before the alarm sounds to prevent nuisance alarming.
Block 60 LOALM:
•
P1 – SP Mode is 2 as we want an internal setpoint
•
P2 – % Deadband is 1.00 as we want 1% of the Drum Pressure transmitter’s full-scale range to be our
deadband (i.e. a 0-200 PSI transmitter would have a dead band of 2 PSI).
•
P3 – is 40.00 as we want 40% of the Drum Pressure transmitter’s full-scale range to give us a high alarm
(i.e. a 0-200 PSI transmitter would alarm below 80 PSI).
•
P4 – Disable Hi/Lo is 1 so that the alarm is disabled when the PB is high
•
P5 – Delay Sec of 60. We want a 60 second delay before the alarm sounds to prevent nuisance alarming.
Block 85 LED:
We will use a light to tell us whether we have selected Local PID or Remote Plant Master control
•
P1 – Invert Input is 1 as we need to invert the input – when the PB is low (0) the LED is high (1) – this
causes the LED to light up when we are in Local PID mode.
Block 125 ASW:
•
P1 – Xfer rate Enable is 1 – we want transfer rate limiting to avoid and “bumps” when switching modes
•
P2 – A to B %/Sec is 1.00. This gives us a 1% per second transfer rate going from Plant Master to Local
PID mode.