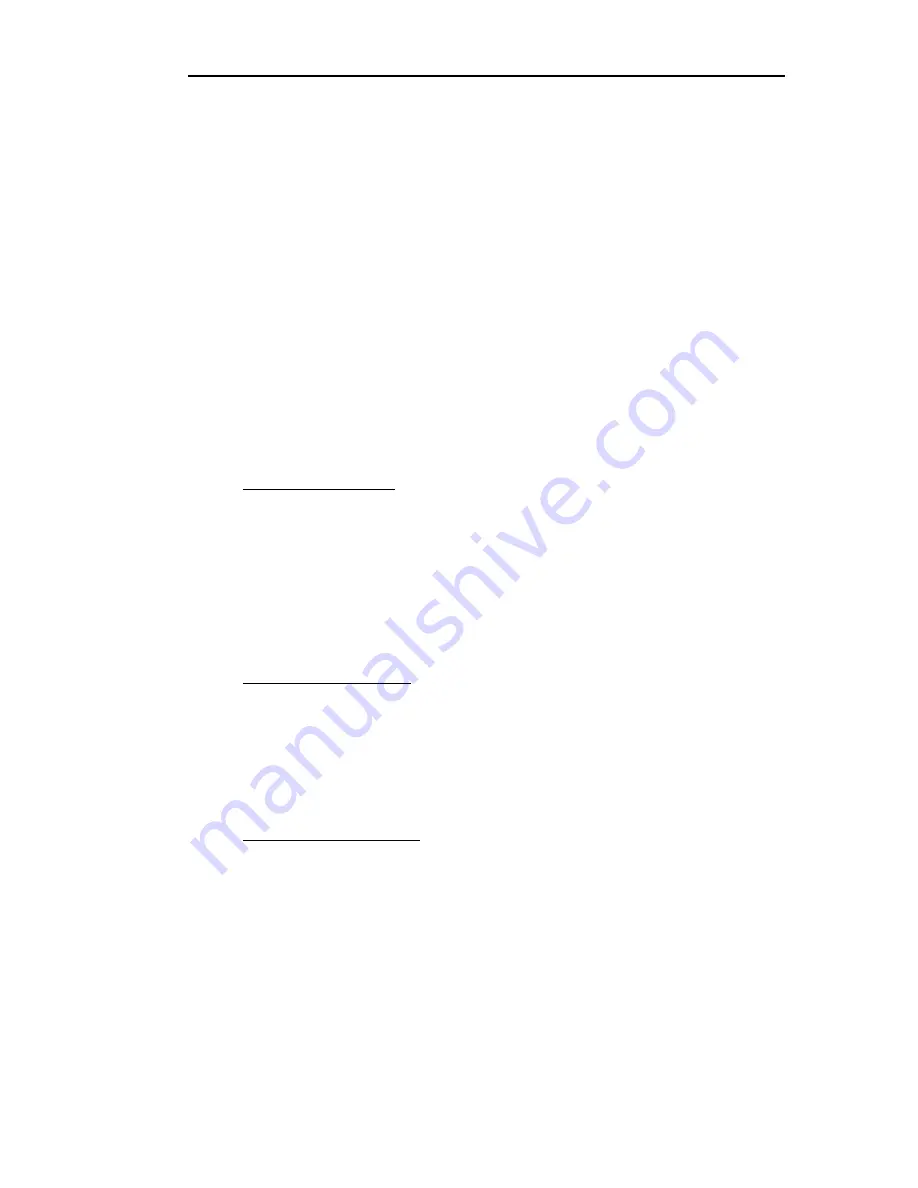
198
Maintenance
Daily Checks
The following maintenance procedures should be done on a daily basis. Make sure
to inspect and replace any hoses which show signs of wear because their failure
could cause a hazard.
Daily Cleaning
At the end of each working day, it is recommended that you flush out the sample
introduction system for five minutes with the plasma on. After analyzing aqueous
solutions, flush with deionized water or a 2% nitric acid solution, followed by
deionized water. After analyzing organic solutions, flush the system using clean
solvent. Also clean the spectrometer housing using a mild lab detergent.
Argon Supply
Make sure that an adequate supply of argon is available and connected to the
system. Check that the argon tank(s) have sufficient pressure, and that a spare tank
is ready if necessary. Argon can be purchased from local suppliers. The argon for
use with ICP systems should be 99.996% pure.
Argon output pressure: 550-825 kPa (80-120 psig)
Purge Gas Supply
The optical path must be purged with either nitrogen or argon. Nitrogen is the
recommended purge gas due to its lower cost. Make sure that an adequate supply
of purge gas is available and connected to the system. Check that the cylinder has
sufficient pressure, and that a spare cylinder is ready if necessary.
The purge gas should be 99.999% pure and is available from local suppliers.
Nitrogen output pressure: 275-825 kPa (40-120 psig)
Shear Gas Supply
The Avio 500 requires a supply of shear gas. The shear gas used is typically
compressed air; however, nitrogen may also be used. Make sure that an adequate
supply of shear gas is available and connected to the system. Check that the supply
has sufficient pressure, and that a spare cylinder is ready if necessary.
Shear Gas output pressure: 550-825 kPa (80-120 psig)
Summary of Contents for AVIO 500
Page 1: ...AVIO 500 Customer Hardware and Service Guide ICP OPTICAL EMISSION ...
Page 2: ......
Page 3: ...Avio 500 Customer Hardware and Service Guide ...
Page 12: ...Contents 10 ...
Page 30: ...28 ...
Page 31: ...C h a p t e r 1 ...
Page 32: ......
Page 33: ...Safety Practices 1 ...
Page 58: ...56 Safety Practices ...
Page 59: ...C h a p t e r 2 ...
Page 60: ......
Page 76: ...74 Preparing Your Laboratory ...
Page 77: ...C h a p t e r 3 ...
Page 78: ......
Page 79: ...System Description 3 ...
Page 115: ...C h a p t e r 4 ...
Page 116: ......
Page 137: ...135 Installing the Quick Change Adjustable Torch Module 1 2 10 8 9 3 4 7 6 5 ...
Page 152: ...150 Installation Figure 4 22 Scott Spray Chamber Clip Assembly in Place ...
Page 195: ...193 Shipping Lists 09290798 USB Cable Table 4 6 Spares Available Continued ...
Page 196: ...194 Installation ...
Page 197: ...C h a p t e r 5 ...
Page 198: ......
Page 217: ...215 Quick Change Adjustable Torch Module 1 2 10 8 9 3 4 7 6 5 ...
Page 316: ...314 Maintenance ...
Page 317: ...C h a p t e r 6 ...
Page 318: ......
Page 342: ...340 Troubleshooting Figure 6 5 Injector too far forward ...
Page 344: ...342 Troubleshooting Figure 6 7 Air leak or spray chamber temperature too high ...
Page 346: ...344 Troubleshooting ...
Page 354: ......