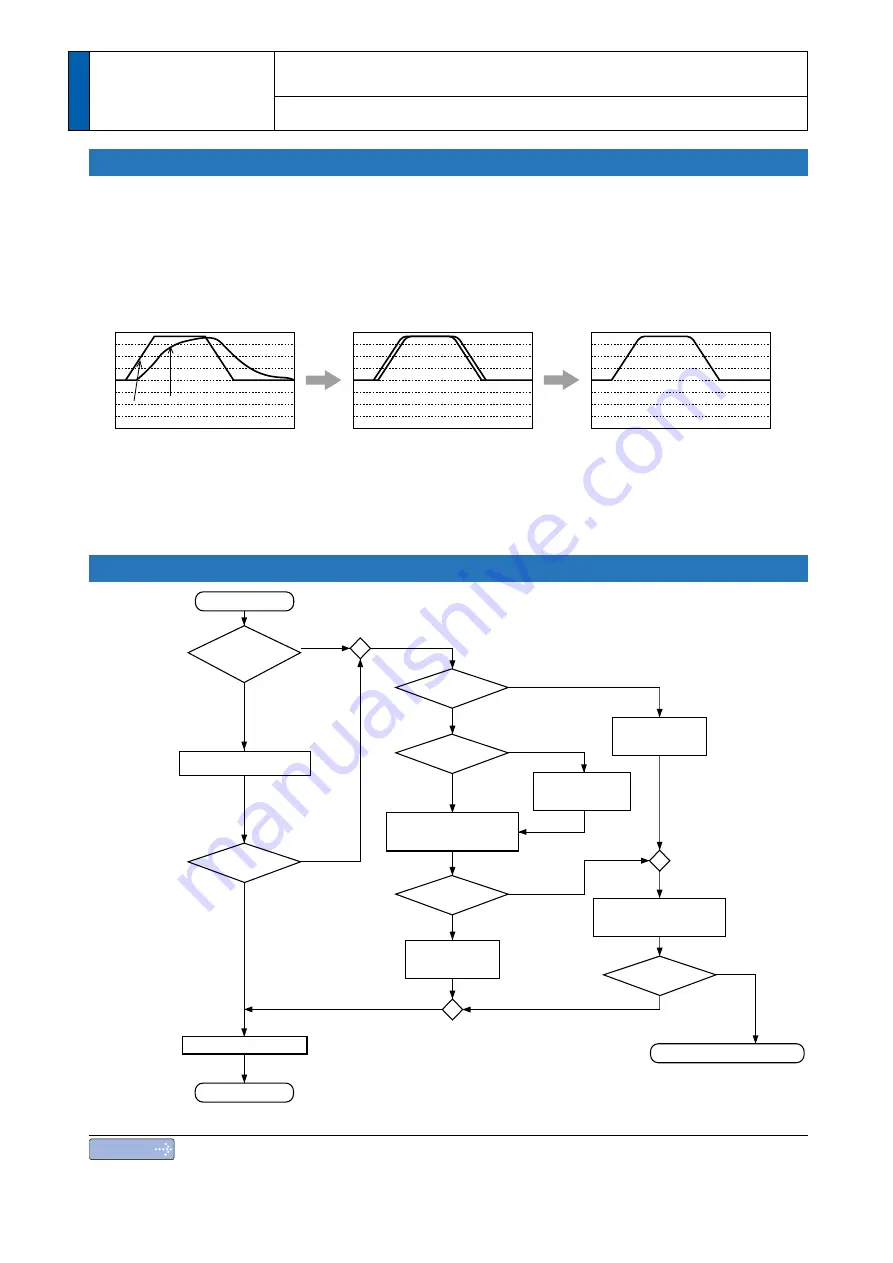
5-2
Rev.2.00
5
1. Gain Adjustment
Adjustment
Outline
Purpose
t is required for the servo driver to run the motor in least time delay and as faithful as
possible against the commands from the host controller. You can make a gain adjust-
ment so that you can run the motor as closely as possible to the commands and obtain
the optimum performance of the machine.
<e.g. : Ball screw>
Procedures
Position loop gain : 200 [0.1 /s]
Velocity loop gain : 1000 [0.1 Hz]
Time constant of
V-loop integration
: 500 [0.1 ms]
Velocity loop feed forward : 0 [0.10 %]
Inertia ratio : 100 [%]
Position loop gain : 1000 [0.1 /s]
Velocity loop gain : 500 [0.1 Hz]
Time constant of
V-loop integration
: 500 [0.1 ms]
Velocity loop feed forward : 0 [0.10 %]
Inertia ratio : 100 [%]
Position loop gain : 1000 [0.1 /s]
Velocity loop gain : 500 [0.1 Hz]
Time constant of
V-loop integration
: 500 [0.1 ms]
Velocity loop feed forward : 500 [0.10 %]
Inertia ratio : 100 [%]
+2000
-
2000
0
0.0
375
250
125
0.0
375
250
125
0.0
375
250
125
[r/min]
Command Speed
Motor actual speed
Gain setup : Low
Gain setup : High
Gain setup : High + feed forward setup
No
Start adjustment
Adjust by
using fit gain
function?
Yes
Yes
Fit gain function
*
No
*
Fit gain function is a function of the setup
support software, “PANATERM”.
Please use the software and the manual
by download from our web site.
Automatic
adjustment ?
Ready for
command
input ?
Yes
Yes
No
No
Real time
auto-gain tuning
Action O.K.?
Action O.K.?
Yes
No
Release of
auto-adjusting
function
Finish adjustment
Operation by using
the trial run function
Yes
No
Action O.K.?
Release of
auto-adjusting
function
Manual gain tuning
Consult to authorized dealer
Writing to EEPROM
Note
For safety operation, first adjust the gain by referring to P.6-42 Setup of Gain Pre-adjustment
Protection.
Summary of Contents for MINAS A6N Series
Page 14: ...14 Rev 2 00 MEMO ...
Page 30: ...1 16 Rev 2 00 MEMO ...
Page 104: ...2 74 Rev 2 00 MEMO ...
Page 228: ...3 124 Rev 2 00 MEMO ...
Page 491: ...7 108 Rev 2 00 MEMO ...