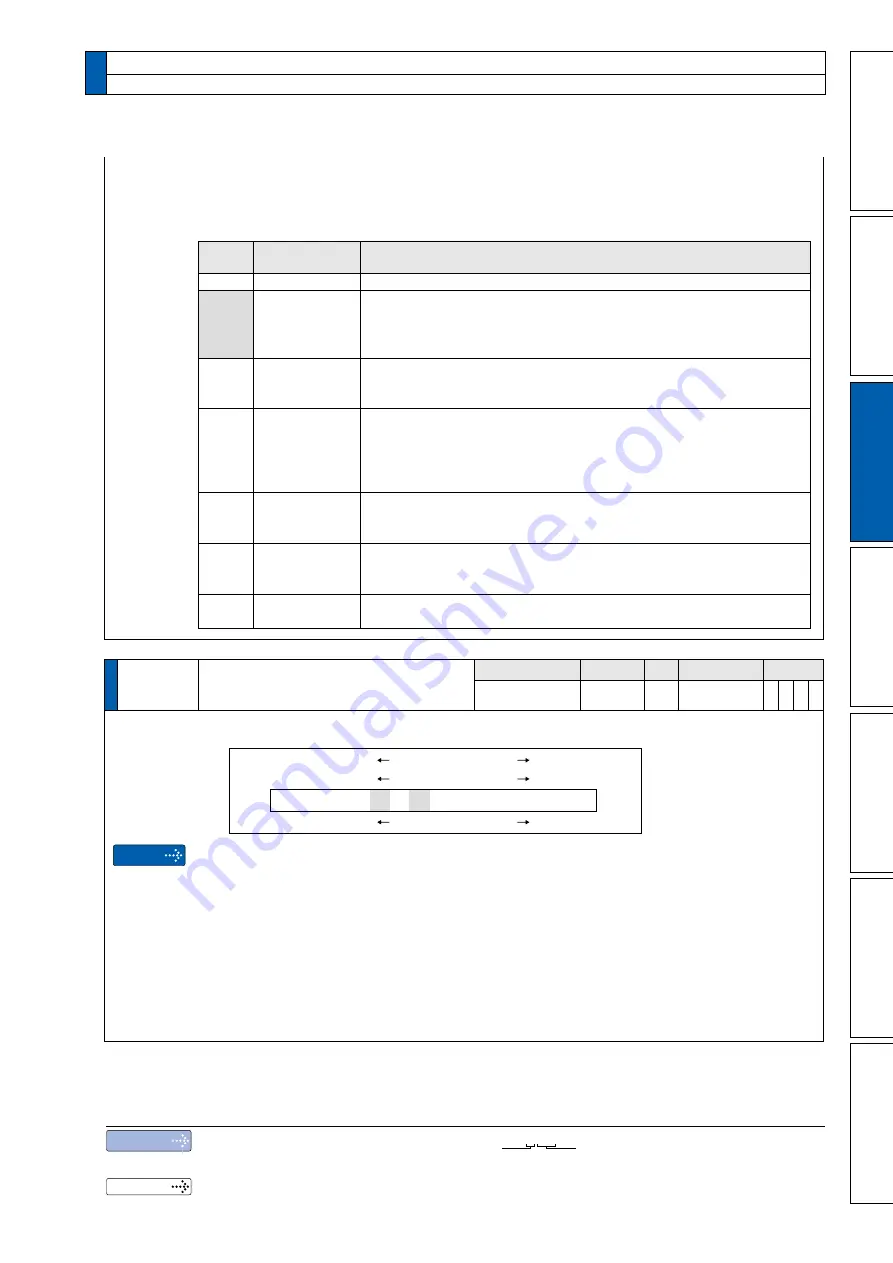
3-41
Note
Related page
・
A parameter is designated as follows:
Pr0.00
No.
Class
・
For
“ Attribute ”,refer to P.3-38
“ Details of Attribute ”.
・
P.2-47
〜
“
Wiring to the Connector
,
X4
”
Default: [ ]
Rev.2.00
1
Before Using the Products
2
Preparation
3
Setup
4
Trial Run
5
Adjustment
6
When In T
roubie
7
Supplement
4.Details of Parameter
【
Class 0
】
Basic Setting
Two-degree-of-freedom control mode: synchronous type
For Two-degree-of-freedom control mode, refer to Pr6.47 (P.3-98).
Set up the action mode of the real-time auto-gain tuning.
Setup
value
Mode
Varying degree of load inertia in motion
0
Invalid
Real-time auto-gain tuning function is disabled.
[1]
Synchronous
Synchronous control mode.
Do not use this mode for unbalanced load or friction compensate. Use
this mode first when maintaining command response filter, then switch
to another mode as necessary.
2
Synchronous
friction
compensation
With dynamic friction compensation/viscous friction compensation in
addition to those of synchronous mode. Use this mode when the load
has a large friction.
3
Stiffness setting
Use this mode when modifying gain filter setting according to stiffness
table without making inertia ratio assumption, unbalanced load
compensation or friction compensation. When handling a load with larger
inertia variations, first estimate inertia in an appropriate mode, e.g. sync
mode, and then switch to this mode.
4
Load
characteristics
update
Use this mode when applying only inertia ratio, dynamic friction
compensation and viscous friction compensation among load
characteristics while holding gain filter setting.
5
Load
characteristic
measurement
Estimate load characteristics without changing basic gain setting or
friction compensation setting with the help of the setup support software.
6
Load fluctuation
response mode
Use this mode when you wish to make robust adjustments for
fluctuating loads.
Pr0.03
Selection of machine stiffness at
real-time auto-gain tuning
Range
Unit
Attribute
Default
Related
control code
0
to
31
—
B
A,B,C-frame: 13
D to F-frame: 11
P S T
Caution
You can set up the response while the real-time auto-gain tuning is valid.
0, 1 - - - - - - - 11 - - 13 - - - - - - - - - - - - 30, 31
low machine stiffness high
low servo gain high
low response high
・
Higher the setup value, higher the velocity response and servo stiffness will be obtained.
However, when increasing the value, check the resulting operation to avoid oscillation or
vibration.
・
Control gain is updated while the motor is stopped. If the motor cannot be stopped due
to excessively low gain or continuous application of one-way direction command, any
change made to Pr0.03 “Selection of machine stiffness at real-time auto-gain tuning” is
not used for update. If the changed stiffness setting is made valid after the motor stopped,
abnormal sound or oscillation will be generated. To prevent this problem, stop the motor
after changing the stiffness setting and check that the changed setting is enabled.
Summary of Contents for MINAS A6N Series
Page 14: ...14 Rev 2 00 MEMO ...
Page 30: ...1 16 Rev 2 00 MEMO ...
Page 104: ...2 74 Rev 2 00 MEMO ...
Page 228: ...3 124 Rev 2 00 MEMO ...
Page 491: ...7 108 Rev 2 00 MEMO ...