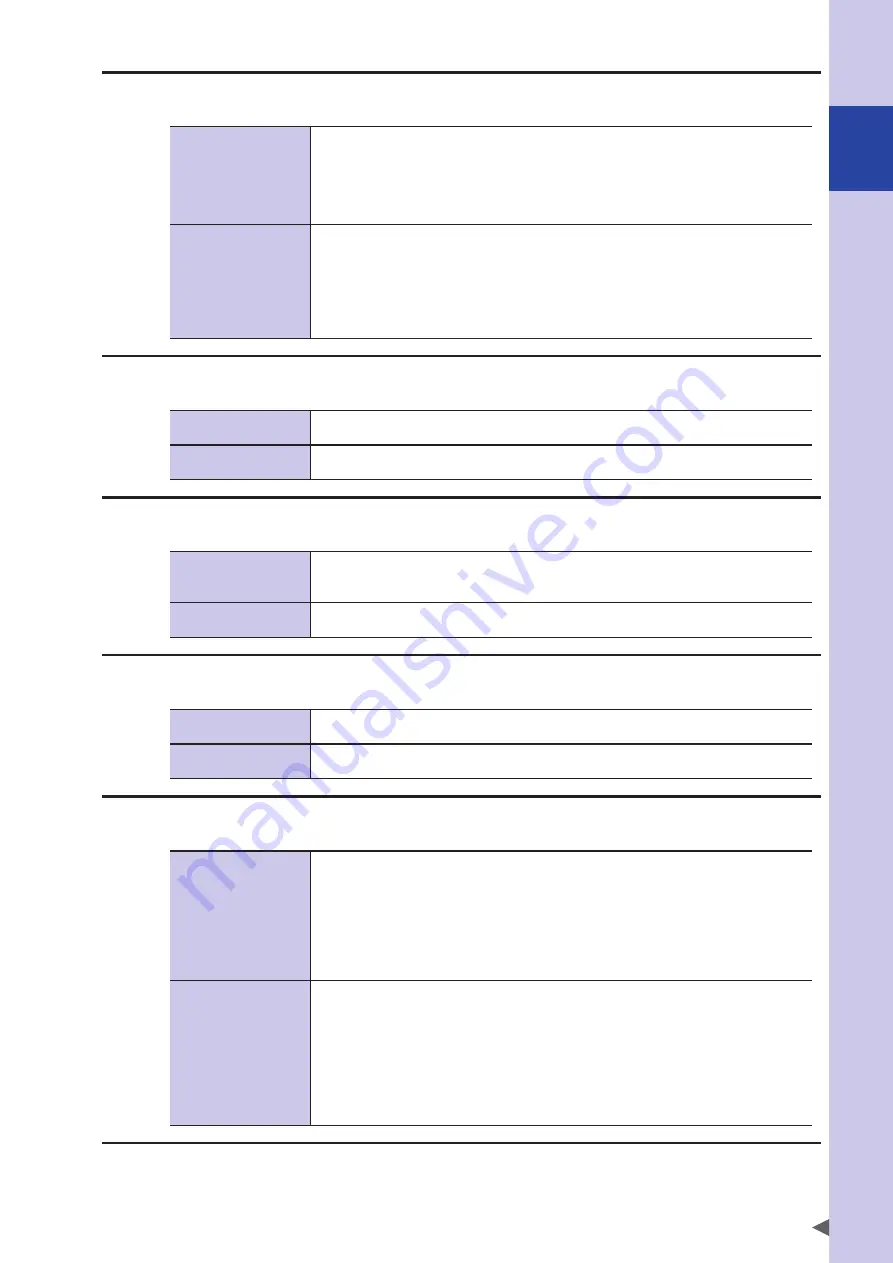
A
Troubleshooting
A-53
17.911: Velocity deviation error
Code
: &H0011 &H038F
Meaning/Cause
a. The robot drive section mechanically locked.
b. The motor acceleration is excessive.
c. The system generation setting is incorrect.
d. The motor cable wiring is broken or wiring is incorrect.
e. The vertical axes electromagnetic brake is defective.
f. Wiring is incorrect or disconnected on the vertical axes electromagnetic brake.
Action
a. Perform robot service and maintenance.
b. Lower the motor acceleration.
c. Redo the system generation.
d-1. Wire the motor cable correctly.
d-2. Replace the motor cable.
e. Replace the vertical axes electromagnetic brake.
f. Replace the ROB I/O cable.
17.912: Current deviation error
Code
: &H0011 &H0390
Meaning/Cause
a. The motor cable wiring was broken.
b. The controller was defective.
Action
a. Replace the motor cable.
b. Replace the controller.
17.913: Dual position deviation error
Code
: &H0011 &H0391
Meaning/Cause
On a dual-drive axis, the position differential between the main axis and sub axis is too large.
a. Friction in the robot drive section is too large.
b. The motor brake wiring is broken.
Action
a. Check the drive sections for assembled condition and lubrication to ensure smooth movement.
b. Check that the motor brake works properly.
17.914: Overspeed
Code
: &H0011 &H0392
Meaning/Cause
a. The robot drive unit was pushed by external force and its speed exceeded the specified value.
b. The system generation setting is incorrect.
Action
a. Remove the external force.
b. Re-perform the system generation.
17.915: Motor over current
Code
: &H0011 &H0393
Meaning/Cause
a. The robot drive section mechanically locked.
b. The motor current exceeded its rated value due to a motor overload.
c. The motor acceleration is excessive.
d. The system generation setting is incorrect.
e. The motor cable wiring is broken or wiring is incorrect.
f. The vertical axes electromagnetic brake is defective.
g. Wiring is incorrect or disconnected on the vertical axes electromagnetic brake.
h. The SAFETY connector is not used correctly.
Action
a. Perform robot service and maintenance.
b. Decrease load on motor.
c. Lower the motor acceleration.
d. Redo the system generation.
e-1. Wire the motor cable correctly.
e-2. Replace the motor cable.
f. Replace the vertical axes electromagnetic brake.
g. Replace the ROB I/O cable.
h. Do not use 24 V DC from the SAFETY connector as power source for external loads.
Summary of Contents for R6YXC1000
Page 1: ...7 6HULHV DW 1R 1 5 5RERW RQWUROOHU 86 5 6 0 18 6 5 5RERWV 5 6HULHV...
Page 2: ......
Page 10: ......
Page 40: ......
Page 42: ......
Page 46: ......
Page 48: ......
Page 54: ......
Page 56: ......
Page 64: ......
Page 80: ......
Page 82: ......
Page 102: ......
Page 108: ......
Page 110: ......
Page 136: ......
Page 168: ......
Page 170: ......
Page 174: ...8 Periodic inspection 8 4...
Page 176: ......
Page 182: ......
Page 256: ......
Page 258: ......
Page 259: ......
Page 260: ...DW 1R 1 XWKRUL HG LVWULEXWRU 3ULQWHG LQ XURSH...