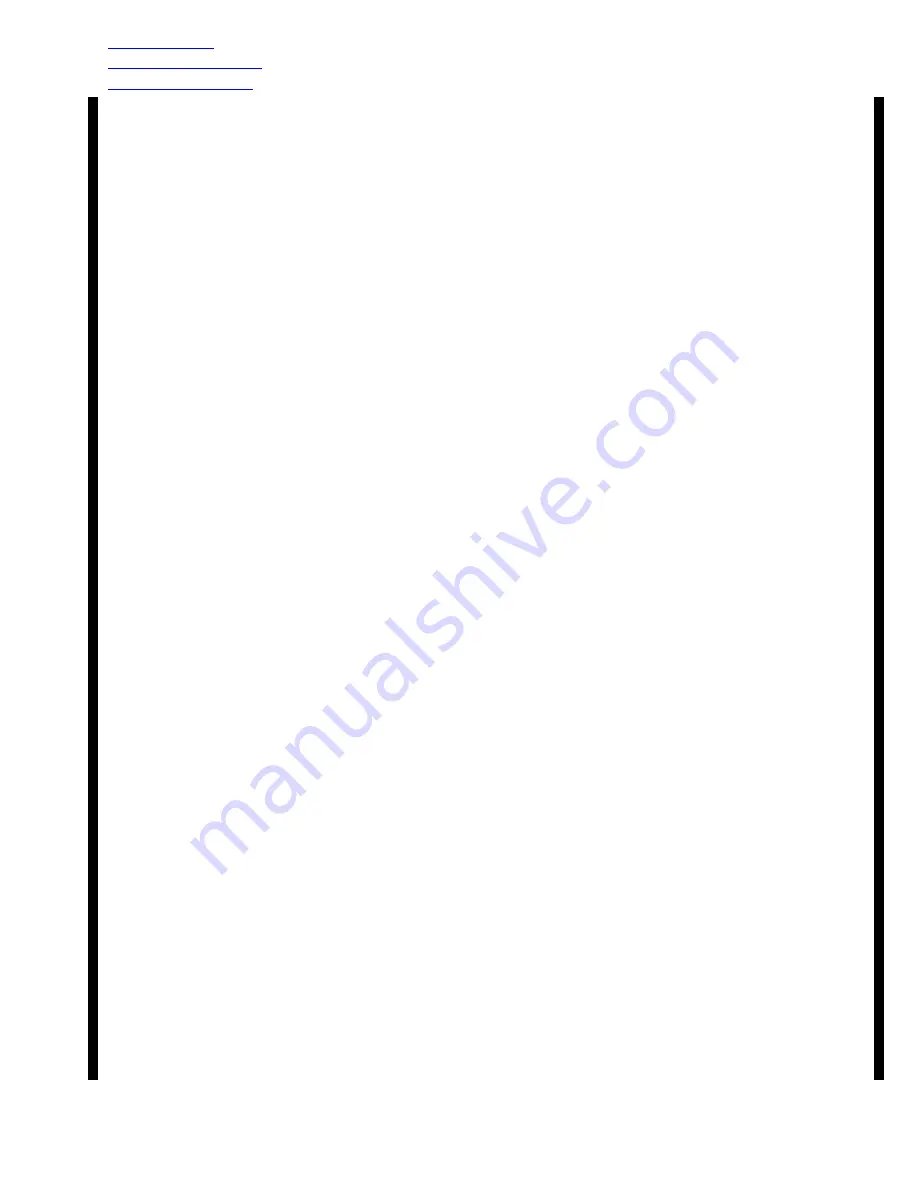
CSP-HMI-3
MD Helicopters, Inc
.
MAINTENANCE MANUAL
96-00-00
Page 605
Revision 13
The information disclosed herein is proprietary to MD Helicopters, Inc.
Neither this document nor any part hereof may be reproduced or transferred to
other documents or used or disclosed to others for manufacturing or any other
purpose except as specifically authorized in writing by MD Helicopters, Inc.
Copyright
©
1999
−
2016 by MD Helicopters, Inc.
3. Wiring Inspection
A. Wire Harness Inspection
NOTE:
D
Perform this inspection upon completion
of maintenance on a wire harness or as
otherwise directed.
D
This procedure applies to RF cables.
D
Not all steps are applicable when per
forming this procedure on completed
maintenance.
(1). Visually inspect wire harness for
contact with structure. If harness
contacts structure, perform the follow
ing:
(a). Inspect individual wires contacting
structure for damage. If damage
limitations are exceeded, repair or
replace as necessary.
(b). Inspect section of RF cable contacting
structure for damage. If damage
limitations are exceeded, replace
cable.
(c). Apply anti-chaffing provisions to
section of wire harness in contact
with structure (Ref. Wire Mainte
nance Procedures). A protected
harness in contact with a smooth
surface is allowed.
(d). Re-route, or adjust routing of
harness if contact is with a sharp
edge. Wiring in contact with sharp
edges is not allowed.
(2). Visually inspect wire harness for proper
support and protection as follows:
(a). Inspect condition of harness clamps.
Replace clamp if cushion is damaged,
and tighten attachment hardware if
loose.
(b). Install additional clamps if necessary,
and only if structure can support the
installation.
(c). Inspect harness for missing or broken
spot ties. Apply tying tape to harness
as required.
(d). Inspect anti-chaffing provisions for
wear or damage. Replace provisions
if necessary.
NOTE:
If anti-chaffing provision is found worn
or damaged, it may be necessary to adjust
routing of wire harness to avoid future dam
age.
(3). Visually inspect routing of wire harness
using the following criteria:
(a). Minimum distance between harness
and movable components shall be 0.5
in. (12.7 mm).
(b). Wire attached to moving assemblies
shall twist instead of bend.
(c). Tangles, kinks, and crossovers are
not permitted.
(d). Adjust harness routing as required to
meet criteria.
(4). Visually inspect bends in wire harness
and make sure minimum allowable
radius is not exceeded. Use following
criteria:
(a). Minimum bend radius for single
wires (non-coaxial) shall be 10 times
the outside diameter of wire.
(b). Minimum bend radius for (non-coaxi
al) single wire, group, bundle or
harness at terminations shall be 3
times the outside diameter of largest
included single wire.
(c). Minimum bend radius for (non-coaxi
al) group, bundle or harness shall be
6
times the outside diameter. In no
case shall bend radius of group,
bundle or harness be less than 10
times the outside diameter of largest
included single wire.
(d). Minimum radius of bend for a coaxial
cable shall not adversely affect the
characteristics of cable, and shall be
no less than 6
times the outside
diameter.
Summary of Contents for 369-500
Page 14: ......
Page 30: ......
Page 82: ......
Page 94: ......
Page 106: ......
Page 116: ......
Page 134: ......
Page 150: ......
Page 162: ......
Page 168: ......
Page 178: ......
Page 226: ......
Page 232: ......
Page 244: ......
Page 346: ......
Page 416: ......
Page 444: ......
Page 458: ......
Page 472: ......
Page 490: ......
Page 536: ......
Page 560: ......
Page 578: ......
Page 604: ......
Page 612: ......
Page 616: ......
Page 628: ......
Page 654: ......
Page 678: ......
Page 706: ......