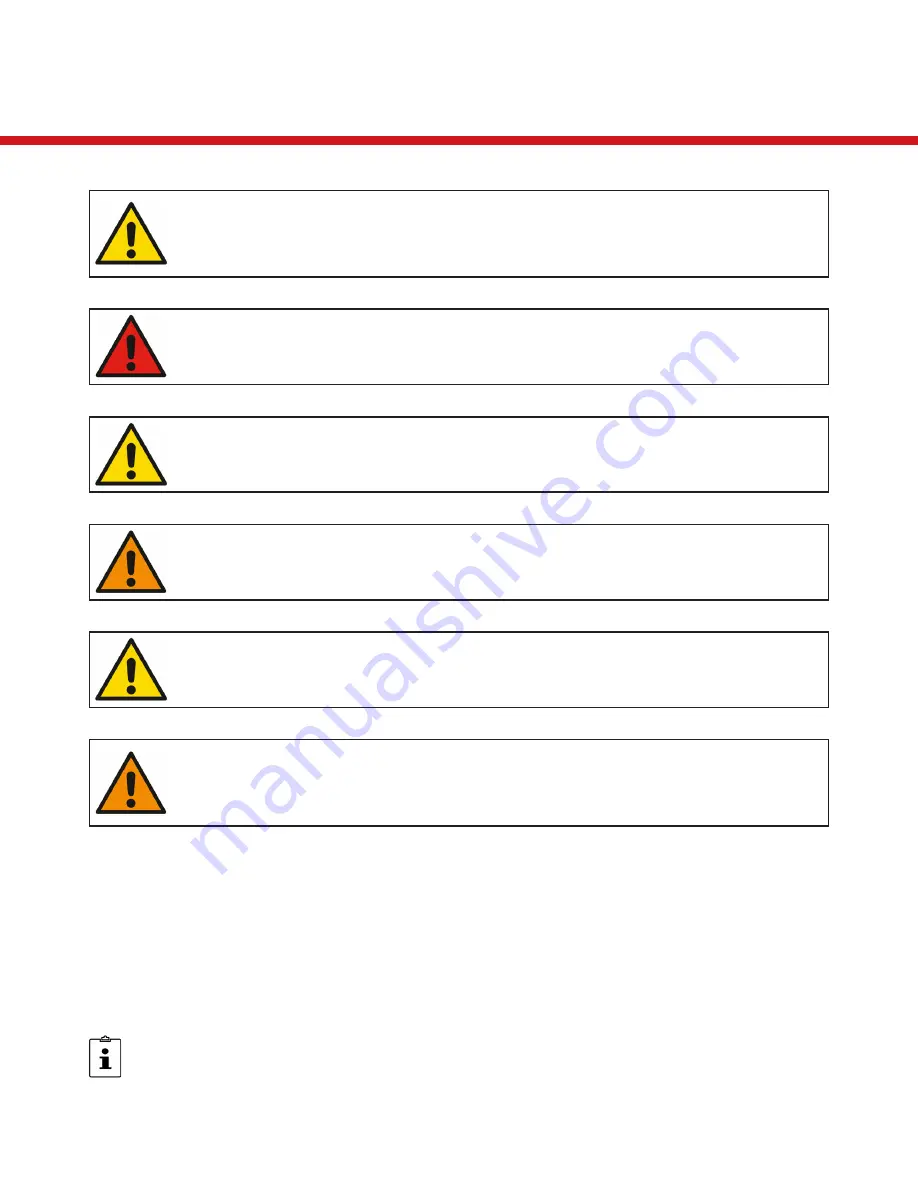
334
80-160
Service / Parts
Welding Instructions
When doing repair welding on your unit take precaution attaching your ground to
the component being repaired. This will reduce the chance of arcing through a
bearing, cylinder, etc., damaging the component. Paint should be removed from
the surface to be used as the “ground” (earth).
Use necessary precaution when welding around fuel tanks, oil reservoir, batteries,
tubing and pressure systems.
When welding close to glass, cylinder rods, or any polished surface, provide adequate
protection from splatter.
Never weld when the engine is running. Always disconnect the battery cables and
applicable grounds before welding.
Do not weld on wet surfaces since this will cause hydrogen embrittlement of the weld.
Always have a fire extinguisher on hand in case of fire. Adequate ventilation and
dry area are necessary. Protective clothing should be used and all persons in the
welding area should have protection for their eyes. Follow instructions for welding
and cutting on paint.
AWS CLASS E7018
Low hydrogenrod for normal repairs on low alloy to medium carbon steel. All position welding, good
penetration, and crack resisting up to 80,000 yield. Also suitable for repair of previous intershield welds.
AWS CLASS E11018G
Low hydrogen rod for repair on high strength alloy steel such as T-1, 80,000 to 100,000 yield. All position
welding, good penetration, and high tensile stength up to 110,000.
NOTE:
Low hydrogen rod E7018 must be used within four (4) hours upon removal from a freshly
opened container or from a storage oven.
Low hydrogen rod E11018G must be used within 1/ 2 hour upon removal from its container or from
a storage oven.
Summary of Contents for 80-160
Page 1: ...OPERATORS MANUAL LOAD KING 80 160 REV B DECEMBER 2020...
Page 2: ...Page Intentionally Blank...
Page 18: ...Page Intentionally Blank...
Page 26: ...26 80 160 Safety 80 160 Safety Sign Locations Right Hand Side View Left Hand Side View...
Page 27: ...27 Rear View Front View...
Page 28: ...28 80 160 Safety Upper Cab...
Page 70: ...70 80 160 Safety Access Egress Rear...
Page 98: ...98 80 160 Assembly...
Page 118: ...118 80 160 Description Of Machine and Controls Lifting controls screen Cab controls screen...
Page 124: ...124 80 160 Description Of Machine and Controls 1 1 PTO Engage Switch...
Page 137: ...137 REPAIRS ADJUSTMENTS REMARKS ITEM REQUIREMENT DATE...
Page 155: ...155 OBSERVE CAUTION NOTES ON OUTRIGGER MOVEMENT WHENEVER SETTING UP OR STOWING OUTRIGGERS...
Page 206: ...Page Intentionally Blank...
Page 209: ...209 8 Install the pin 5 in the guide sheave kickstand 5 9 Remove the lower left hand pin 7 7...
Page 257: ...257 Master Lubrication Chart 13 14 5 4 3 2 2 8 12 9 7 6 15 10 11 BOOM BLOCK TOP VIEW...
Page 300: ...Page Intentionally Blank...
Page 326: ...Page Intentionally Blank...
Page 331: ...331 Repairs Adjustments Remarks Log ITEM REQUIREMENT DATE...
Page 333: ...333...
Page 354: ...Page Intentionally Blank...
Page 362: ...362 80 160 Appendix...
Page 366: ...80 160 Notes...
Page 369: ...80 160 Operator Manual...