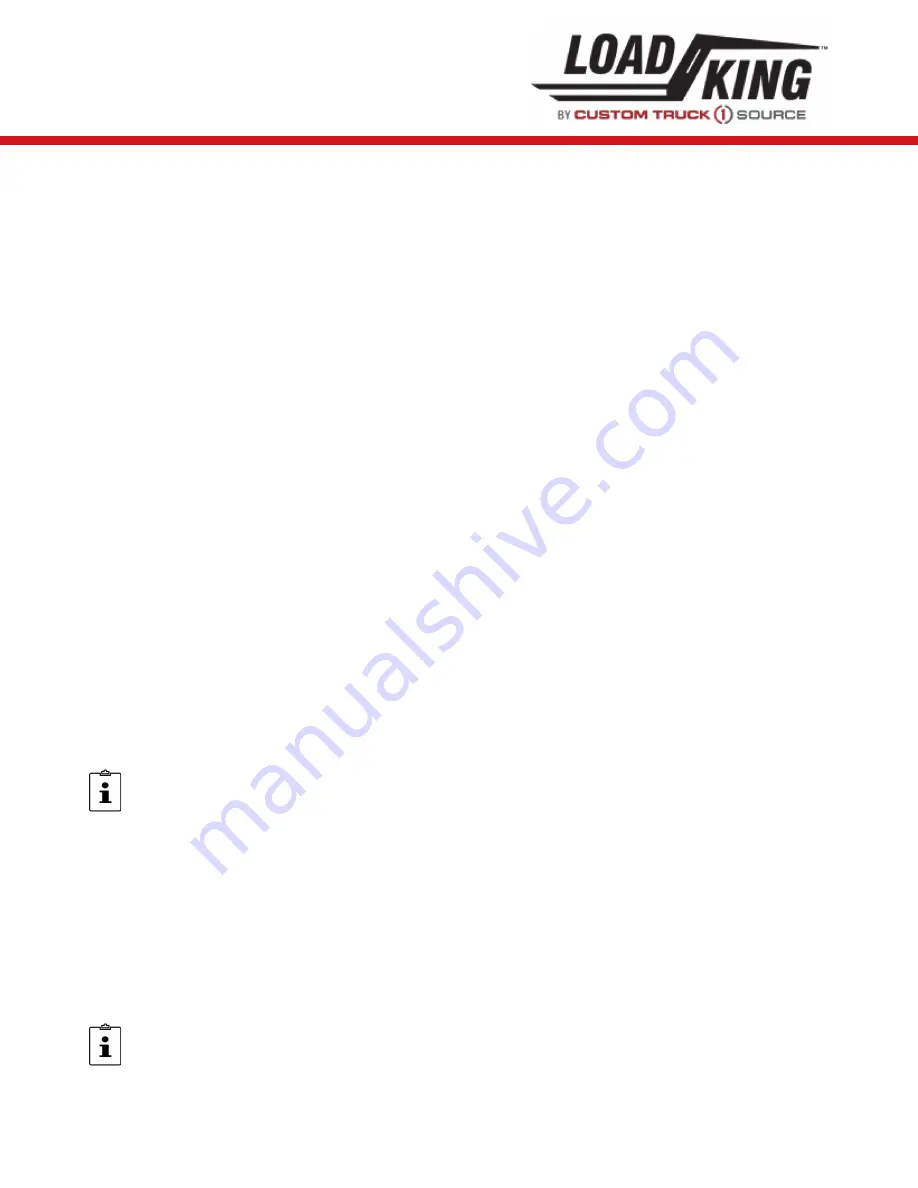
321
Cylinder Leakage
Hydraulic cylinders may retract due to the cooling of the oil in cylinder. Oil shrinks approximately
1% per 25°F of cooling, or as an example, if a cylinder is extended 100" and cools 100°F, it will shrink 4".
TELESCOPE CYLINDER
If excessive leak-down is encountered, check items in the following sequence:
1. With boom offside and horizontal, extend the boom approximately 6 ft. per section. Mark the first
telescoping section at the end of the base section.
2. Elevate the boom to maximum angle and suspend a load on the hook. (7 tons on a 2- part line would
approximate manufacturer’s inspection procedures.)
3. With engine shut off, hold or tie the thumb wheel on the joystick in the full “extend” position for
approximately 15 minutes.
4. Return the telescope thumbwheel joystick to neutral, start engine, ground the load, and return the
boom to horizontal. Re-mark the boom section as in (1). Measure the distance between marks to
determine leak-down of the cylinder.
The manufacturer’s allowable drift specification for production machines is as follows:
With 14,300 lb. hook load, 2-part hoist line, boom extended about 6 ft. per section at maximum boom
angle, and 160 degree F. hydraulic oil temperature, the leak-down per cylinder is not to exceed 3/4 inch
in a 15-minute period.
IDENTIFY A DEFECTIVE HOLD VALVE in the cylinder which drifts excessively by interchanging the hold
valve cartridge with one removed from a cylinder that is not drifting, or by replacement with a new
cartridge. Before installing the cartridge, visually inspect the external “O” rings and backup washers.
Retest per the procedure above to determine if hold was defective.
An alternate method to test the hold valve would be to disconnect the two hoses coming from the valve
bank and then elevate the boom . If oil continues to flow slowly from the extend line then it is a hold
problem. If oil continues to flow from retract, then it is faulty or leaking by piston in cylinder.
NOTE:
With hollow rod telescope cylinders you can drain in excess of 40 gallons of oil from the rod.
If the boom comes in while doing this test, then the cylinder is faulty or leaking by the piston in the
cylinder.
IF THE HOLD VALVE IS NOT FOUND DEFECTIVE, the cylinder must be removed from the boom assembly
for repacking and checking. Prior to reassembly of the cylinder, conduct an air test on the piston rod by
blocking the retract ports on the rod near the piston end. Slip a plastic bag over piston end of rod and
retain and seal with rubber band. Apply and hold a slight amount of air pressure at the retract port of the
rod. (Port stamped with “R”) Expansion of the plastic bag indicates a defective rod weldment or seals
on the port tube in the rod.
WHEN REASSEMBLING THE CYLINDER, care should be taken to keep the piston rod assembly parallel
in all planes with the cylinder barrel as the piston enters and is pushed down the barrel prior to gland
engagement.
NOTE:
An external leak from telescope cylinders or hydraulic line within the boom assembly does
not cause leak-down without also having one or more of the above conditions present.
Summary of Contents for 80-160
Page 1: ...OPERATORS MANUAL LOAD KING 80 160 REV B DECEMBER 2020...
Page 2: ...Page Intentionally Blank...
Page 18: ...Page Intentionally Blank...
Page 26: ...26 80 160 Safety 80 160 Safety Sign Locations Right Hand Side View Left Hand Side View...
Page 27: ...27 Rear View Front View...
Page 28: ...28 80 160 Safety Upper Cab...
Page 70: ...70 80 160 Safety Access Egress Rear...
Page 98: ...98 80 160 Assembly...
Page 118: ...118 80 160 Description Of Machine and Controls Lifting controls screen Cab controls screen...
Page 124: ...124 80 160 Description Of Machine and Controls 1 1 PTO Engage Switch...
Page 137: ...137 REPAIRS ADJUSTMENTS REMARKS ITEM REQUIREMENT DATE...
Page 155: ...155 OBSERVE CAUTION NOTES ON OUTRIGGER MOVEMENT WHENEVER SETTING UP OR STOWING OUTRIGGERS...
Page 206: ...Page Intentionally Blank...
Page 209: ...209 8 Install the pin 5 in the guide sheave kickstand 5 9 Remove the lower left hand pin 7 7...
Page 257: ...257 Master Lubrication Chart 13 14 5 4 3 2 2 8 12 9 7 6 15 10 11 BOOM BLOCK TOP VIEW...
Page 300: ...Page Intentionally Blank...
Page 326: ...Page Intentionally Blank...
Page 331: ...331 Repairs Adjustments Remarks Log ITEM REQUIREMENT DATE...
Page 333: ...333...
Page 354: ...Page Intentionally Blank...
Page 362: ...362 80 160 Appendix...
Page 366: ...80 160 Notes...
Page 369: ...80 160 Operator Manual...