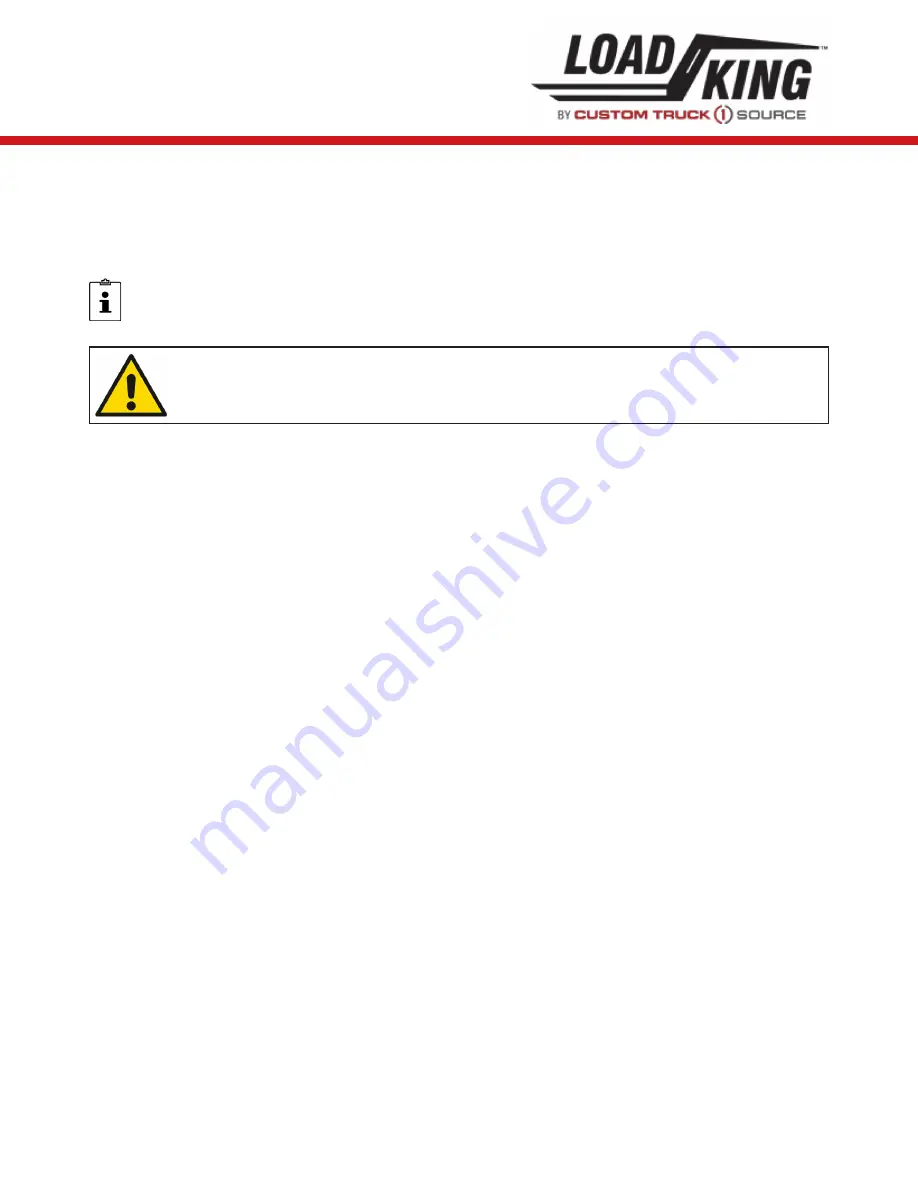
237
Your
Load King
Crane will have been filled with Shell Tellus S2 V 46 hydraulic oil unless otherwise
specified. Different manufacturer’s use chemical formulations which may not be compatible. Therefore,
at a minimum, you must verify that any makeup oil added is compatible with the oil already in the system.
When changing oil, if a different brand is used, the system should be flushed by cycling all cylinders at
least once to their limits to insure that as much as possible of the old oil has been removed from the
system.
NOTE:
Observe all oil handling hazards. Used oil should be recycled or reclaimed. Remember, oil
is not a disposable resource and it is your responsibility to maintain sound environmental practices
in regards to used oil and other fluids.
IMPROPER OR INADEQUATE MAINTENANCE OF THE HYDRAULIC OIL OR OIL
FILTER WILL RESULT IN PREMATURE WEAR TO VALVES, CYLINDERS,
MOTORS, ETC.
Summary of Contents for 80-160
Page 1: ...OPERATORS MANUAL LOAD KING 80 160 REV B DECEMBER 2020...
Page 2: ...Page Intentionally Blank...
Page 18: ...Page Intentionally Blank...
Page 26: ...26 80 160 Safety 80 160 Safety Sign Locations Right Hand Side View Left Hand Side View...
Page 27: ...27 Rear View Front View...
Page 28: ...28 80 160 Safety Upper Cab...
Page 70: ...70 80 160 Safety Access Egress Rear...
Page 98: ...98 80 160 Assembly...
Page 118: ...118 80 160 Description Of Machine and Controls Lifting controls screen Cab controls screen...
Page 124: ...124 80 160 Description Of Machine and Controls 1 1 PTO Engage Switch...
Page 137: ...137 REPAIRS ADJUSTMENTS REMARKS ITEM REQUIREMENT DATE...
Page 155: ...155 OBSERVE CAUTION NOTES ON OUTRIGGER MOVEMENT WHENEVER SETTING UP OR STOWING OUTRIGGERS...
Page 206: ...Page Intentionally Blank...
Page 209: ...209 8 Install the pin 5 in the guide sheave kickstand 5 9 Remove the lower left hand pin 7 7...
Page 257: ...257 Master Lubrication Chart 13 14 5 4 3 2 2 8 12 9 7 6 15 10 11 BOOM BLOCK TOP VIEW...
Page 300: ...Page Intentionally Blank...
Page 326: ...Page Intentionally Blank...
Page 331: ...331 Repairs Adjustments Remarks Log ITEM REQUIREMENT DATE...
Page 333: ...333...
Page 354: ...Page Intentionally Blank...
Page 362: ...362 80 160 Appendix...
Page 366: ...80 160 Notes...
Page 369: ...80 160 Operator Manual...