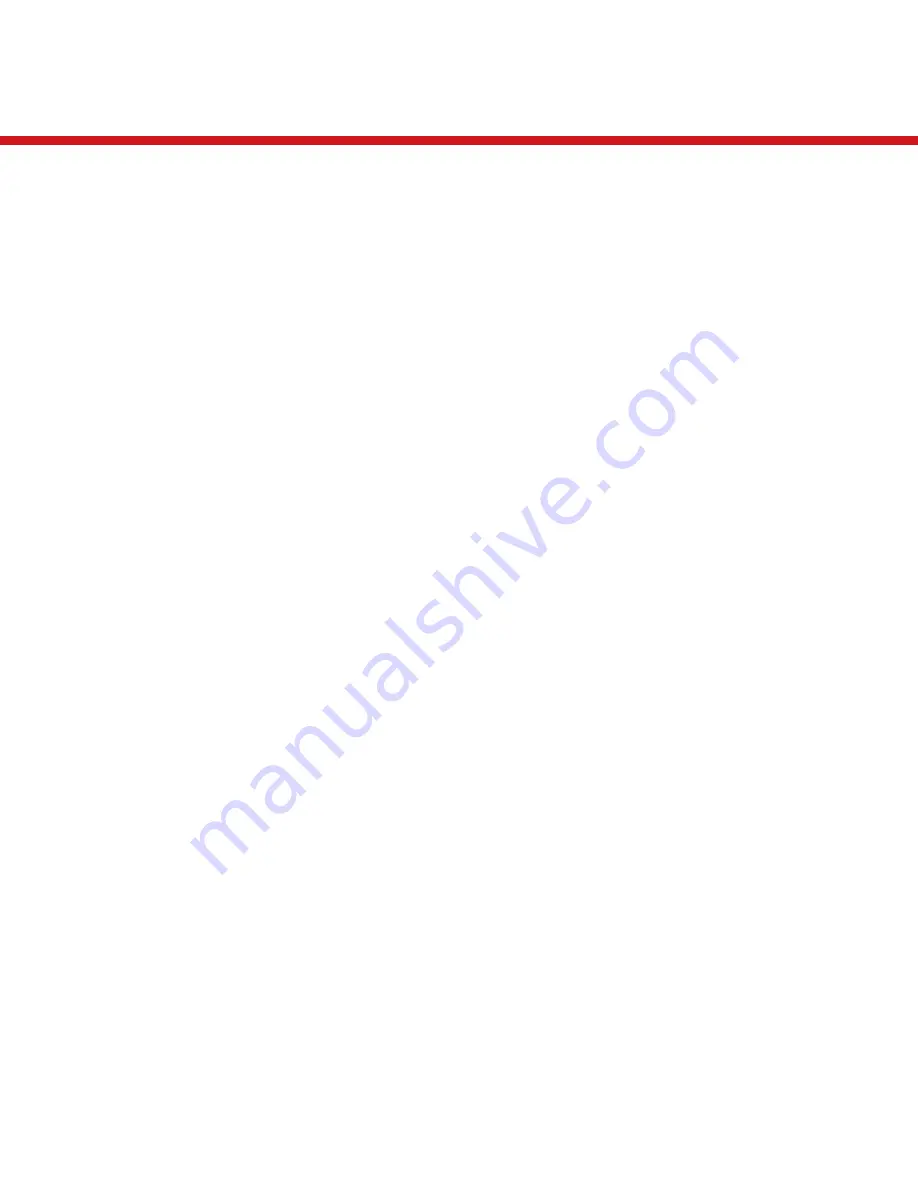
286
80-160
Maintenance
HYDRAULIC CYLINDERS
Check the cylinder mounting brackets, bushings, and pins for wear, alignment, tightness, and damage.
If misalignment or excessive play or wear are detected, replace the defective pin or bushing. Check the
rod eye welds for cracks and breaks and have damaged welds repaired.
HYDRAULIC COMPONENTS
Check the hydraulic valves, motors, pumps, hoses, tubes and connections for excess dirt, oil and
grease. Clean these items if necessary and check for leaks and damage. Tighten leaky connections and
repair any damaged components.
WEEKLY:
RETURN LINE FILTER
Change the hydraulic reservoir return line filters after the first 40 hours of the break-in period; thereafter,
follow the quarterly check recommendation.
MONTHLY:
HYDRAULIC RESERVOIR
Drain any accumulated moisture from the hydraulic reservoir by parking the machine on a slight incline
and loosen the pipe plug in the bottom of the reservoir.
HYDRAULIC OIL
Visually check the condition of the hydraulic oil once each month. Thickening of the oil or a change in its
appearance, such as darkening, may serve as a rough indicator of when an oil change is needed.
Periodic testing of the oil is the safest, most accurate method of determining the condition of the oil. An
oil supplier can be consulted for assistance in testing the oil.
Change the oil whenever testing and/or inspection reveals the oil to be unsuitable for safe and efficient
operation or yearly.
QUARTERLY:
HYDRAULIC FILTER
Remove and replace the hydraulic reservoir return line filters. Access is gained by removing the cover
plate on the right-hand deck plate.
When replacing the filters, clean the spring and bypass valves. Inspect the “O” ring for damage and
replace if necessary.
Summary of Contents for 80-160
Page 1: ...OPERATORS MANUAL LOAD KING 80 160 REV B DECEMBER 2020...
Page 2: ...Page Intentionally Blank...
Page 18: ...Page Intentionally Blank...
Page 26: ...26 80 160 Safety 80 160 Safety Sign Locations Right Hand Side View Left Hand Side View...
Page 27: ...27 Rear View Front View...
Page 28: ...28 80 160 Safety Upper Cab...
Page 70: ...70 80 160 Safety Access Egress Rear...
Page 98: ...98 80 160 Assembly...
Page 118: ...118 80 160 Description Of Machine and Controls Lifting controls screen Cab controls screen...
Page 124: ...124 80 160 Description Of Machine and Controls 1 1 PTO Engage Switch...
Page 137: ...137 REPAIRS ADJUSTMENTS REMARKS ITEM REQUIREMENT DATE...
Page 155: ...155 OBSERVE CAUTION NOTES ON OUTRIGGER MOVEMENT WHENEVER SETTING UP OR STOWING OUTRIGGERS...
Page 206: ...Page Intentionally Blank...
Page 209: ...209 8 Install the pin 5 in the guide sheave kickstand 5 9 Remove the lower left hand pin 7 7...
Page 257: ...257 Master Lubrication Chart 13 14 5 4 3 2 2 8 12 9 7 6 15 10 11 BOOM BLOCK TOP VIEW...
Page 300: ...Page Intentionally Blank...
Page 326: ...Page Intentionally Blank...
Page 331: ...331 Repairs Adjustments Remarks Log ITEM REQUIREMENT DATE...
Page 333: ...333...
Page 354: ...Page Intentionally Blank...
Page 362: ...362 80 160 Appendix...
Page 366: ...80 160 Notes...
Page 369: ...80 160 Operator Manual...