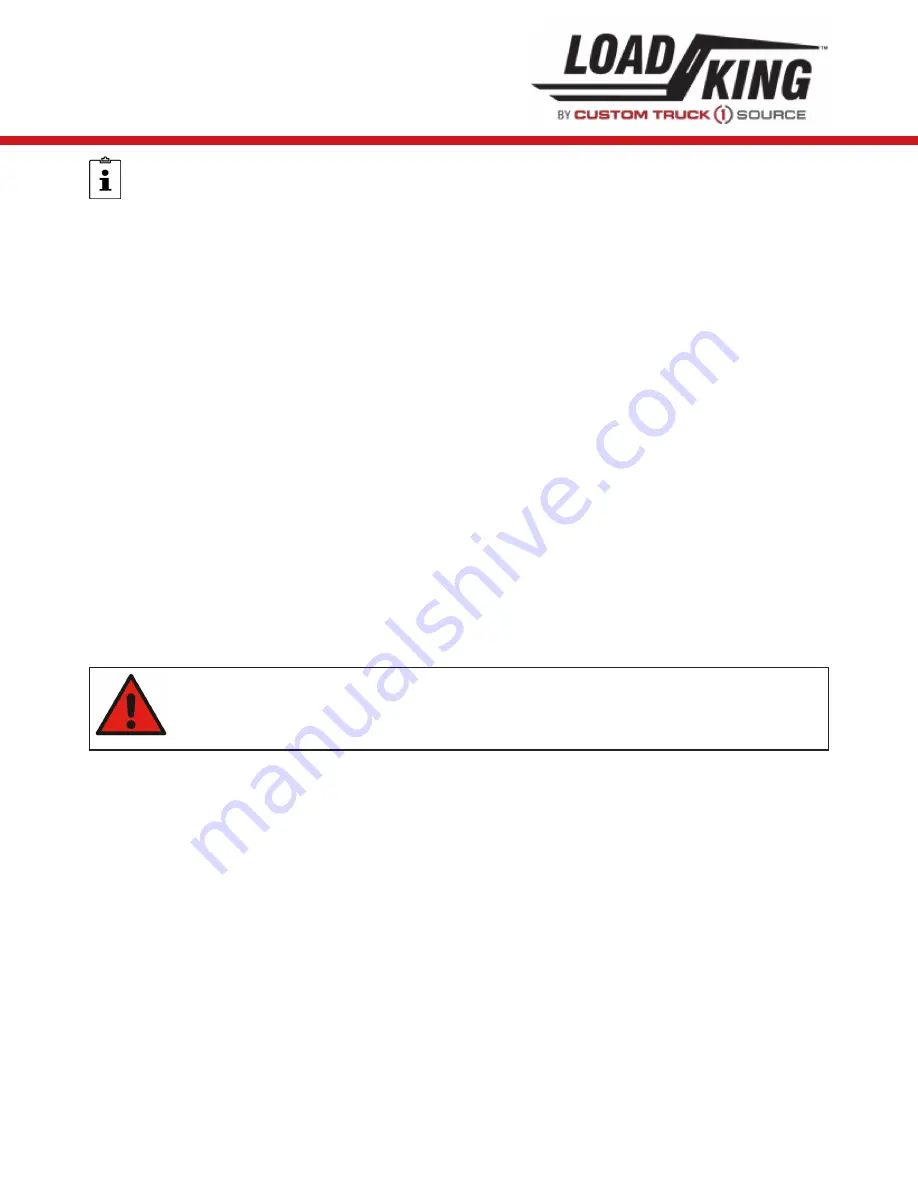
145
NOTES:
The disassembly of boom is a recommendation for proper inspection related to wear,
corrosion, cracks or breakage of components. If crane is used in a highly corrosive environment due
to salts or chemicals, then inspection and maintenance intervals should be more frequent than
shown above.
WEEKLY:
STRUCTURAL MEMBERS AND WELDS
Visually inspect all structural members and welds including
(but not limited to) the extended boom for straightness, roller (or pad) adjustment, and cracks. Pay
special attention to the longitudinal welds joining the top, side and bottom plates. Check the welds
attaching the jib ears to the boom head and the welds attaching the boom head to the tip section. Inspect
the cylinder attaching supports and the boom pivot area.
Inspect the superstructure welds, the welds on the hoist cylinder supports and the welds between the
bottom mounting plate and the vertical plates. This is especially important if the machine is being used
extensively in clamshell, concrete pouring, headache ball, or other high duty cycle applications.
On the carrier, inspect the swing bearing weld band and supporting header welds. Check the welds
attaching the outrigger box to the frame, outrigger box ends at the collar, jack cylinder mounting tube,
and the beam welds.
Visually inspect all boom sections at least weekly or every fifty (50) hours, whichever occurs first.
Preparatory to making the inspection, set the outriggers and rotate the upper to an area where the boom
can be fully lowered and extended.
With the boom fully lowered and extended, visually inspect the sides, top and bottom of each section
for any unusual deformation, scrubbing, wear, or cracking in either the plates or welds, particularly the
fillet welds along the bottom edge of the side plates of the telescoping sections. In addition, note any
missing or illegible indicator mark decals on the telescoping sections.
If any cracks in either fillet welds or plates are noted, the particular component must
be replaced before any further crane operations are performed. This is necessary to
maintain the structural strength of the boom and prevent possible catastrophic failure
resulting in injury or property damage.
Field repair of boom sections is NOT recommended because distortion may be introduced” and original
structural strength not restored.
Boom extension indicator decals are extremely important and must be in place at all times.” Boom
section failures can occur due to overstressing within rated capacities if the sections” are not equally
extended within one indicator mark difference between the telescoping” sections.
Summary of Contents for 80-160
Page 1: ...OPERATORS MANUAL LOAD KING 80 160 REV B DECEMBER 2020...
Page 2: ...Page Intentionally Blank...
Page 18: ...Page Intentionally Blank...
Page 26: ...26 80 160 Safety 80 160 Safety Sign Locations Right Hand Side View Left Hand Side View...
Page 27: ...27 Rear View Front View...
Page 28: ...28 80 160 Safety Upper Cab...
Page 70: ...70 80 160 Safety Access Egress Rear...
Page 98: ...98 80 160 Assembly...
Page 118: ...118 80 160 Description Of Machine and Controls Lifting controls screen Cab controls screen...
Page 124: ...124 80 160 Description Of Machine and Controls 1 1 PTO Engage Switch...
Page 137: ...137 REPAIRS ADJUSTMENTS REMARKS ITEM REQUIREMENT DATE...
Page 155: ...155 OBSERVE CAUTION NOTES ON OUTRIGGER MOVEMENT WHENEVER SETTING UP OR STOWING OUTRIGGERS...
Page 206: ...Page Intentionally Blank...
Page 209: ...209 8 Install the pin 5 in the guide sheave kickstand 5 9 Remove the lower left hand pin 7 7...
Page 257: ...257 Master Lubrication Chart 13 14 5 4 3 2 2 8 12 9 7 6 15 10 11 BOOM BLOCK TOP VIEW...
Page 300: ...Page Intentionally Blank...
Page 326: ...Page Intentionally Blank...
Page 331: ...331 Repairs Adjustments Remarks Log ITEM REQUIREMENT DATE...
Page 333: ...333...
Page 354: ...Page Intentionally Blank...
Page 362: ...362 80 160 Appendix...
Page 366: ...80 160 Notes...
Page 369: ...80 160 Operator Manual...