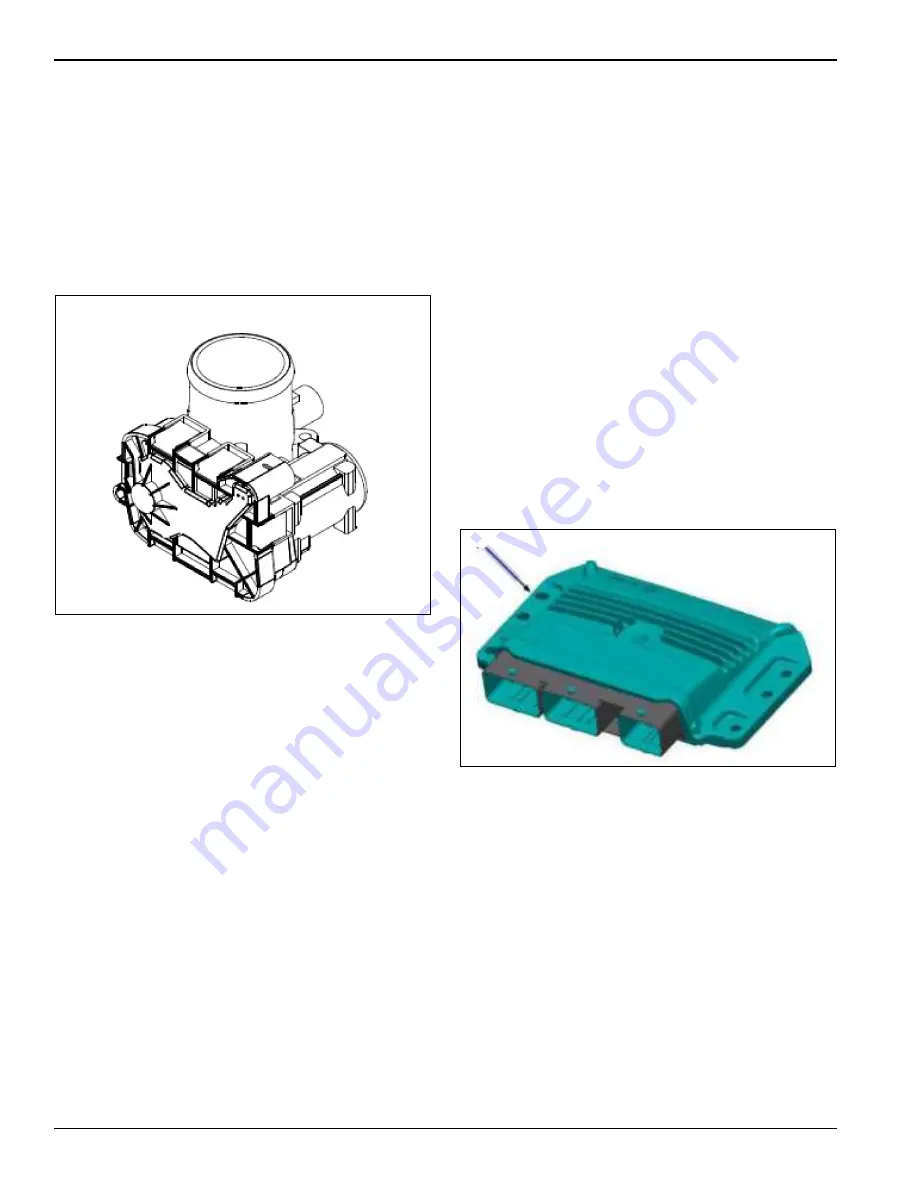
5-4
F-581-R1
ENGINE WITH FUEL SYSTEM
Electronic Throttle
The electronic throttle plate is commanded to open by the
ECU. A servo motor on the throttle opens the throttle
plate and a throttle position sensor sends a signal back to
the ECU to confirm the commanded opening is achieved.
The electronic throttle performs the tasks of idle and
over-speed governing. If there is a sensor failure in the
throttle the power to the motor is shut off and the plate
assumes a limp home position (just slightly open to allow
a high idle of the forklift).
Figure 5-3: Throttle Body
As mentioned previously, if there is a throttle related
failure, the electronic throttle will go into a “LIMP HOME”
mode of operation. This mode of operation has the
symptom of no engine response to the pedal. Check for
any throttle body codes and remedy the situation. Then
clear the codes and key off the vehicle and let sit for at
least 30 seconds. This resets the ECU and removes the
“LIMP HOME” throttle mode and should return pedal
response. The “LIMP HOME” mode can be triggered by
simply disconnecting the throttle body connector while
the vehicle power is on. If the throttle body of an engine
has to be replaced, the range of travel of the new throttle
has to be learned by the ECU. It is important to open the
S3000 monitor software, see page 5-15 through
page 5-18, to clear the EEPROM in the diagnostics tab.
The key switch must then be turned off for 30 seconds.
When the key is switched back on the ECU will cycle the
throttle body through the full range of motion to re-learn
the throttle body end stops.
S3000 Engine Control Unit (S3000)
The S3000 ECU is the command and control unit for the
2.4 liter LPG engine. The ECU monitors inputs, performs
engine management calculations and controls outputs to
achieve the desired engine performance. The ECU also
monitors the various input and output components, as
well as it’s own internal functioning, for failures and then
alerts the operation if any failures occur. The ECU also
supplies the forklift controller with various engine
operating parameters to allow for proper forklift
operation. The S3000 ECU along with the S3000 Monitor
software allows monitoring and recording of engine
operating parameters as well as reading and clearing
engine Diagnostic Trouble Codes (DTCs). The S3000
Monitor software is run in a Windows XP operating
system on a laptop or desktop PC. The connection from
the PC to the S3000 is through a Kvaser or iFak cable
which connects to the USB port of the PC and to the CAN
BUSS lines of the S3000 ECU (pin 2 of the 9 pin
connector is CAN L and pin 7 is CAN H). The
corresponding CAN wires can be found on the engine
harness 8 pin Duetch connector CRP83 pins 7 (CAN
H)and 8 (CAN L). See Figure 4-2.
Figure 5-4: Engine Control Unit
The ECU (S3000) opens the throttle to the required
opening to obtain the commanded speed. It then
calculates the airflow into the engine based on MAP,
speed, air and coolant temperature. The correct amount
of fuel for the this airflow is calculated and injection
signals, compensated for the actual measured fuel
pressure, are sent to the injector driver unit which drives
the peak and hold current injectors to deliver fuel to each
intake manifold runner in sequence. The spark timing is
set for optimum drivability and emissions. The resulting
fuel air mixture is burned in the cylinder supplying torque
to the crankshaft. The heated exhaust gas oxygen
(HEGO) sensor is used to determine if the fueling was
rich or lean of mixture and the injector pulse widths are
then trimmed to provide fueling, which cycles the air to
fuel ratio around the optimum 15.7 : 1 air to fuel ratio, to
achieve maximum catalyst reduction of pollutants.
Summary of Contents for Bendi B40i4
Page 2: ......
Page 26: ...1 20 F 581 R1 INTRODUCTION SAFETY AND INSPECTION...
Page 100: ...3 52 F 581 R1 TROUBLESHOOTING AND CORRECTIVE MAINTENANCE...
Page 120: ...4 20 F 581 R1 CALIBRATION AND PROGRAMMING...
Page 129: ...ENGINE WITH FUEL SYSTEM 5 9 Figure 5 10 Fuel System Troubleshooting...
Page 133: ...ENGINE WITH FUEL SYSTEM 5 13...
Page 134: ...5 14 F 581 R1 ENGINE WITH FUEL SYSTEM...
Page 140: ...6 2 F 581 R1 GM ENGINE SUPPLIER PROVIDED DOCUMENTATION...