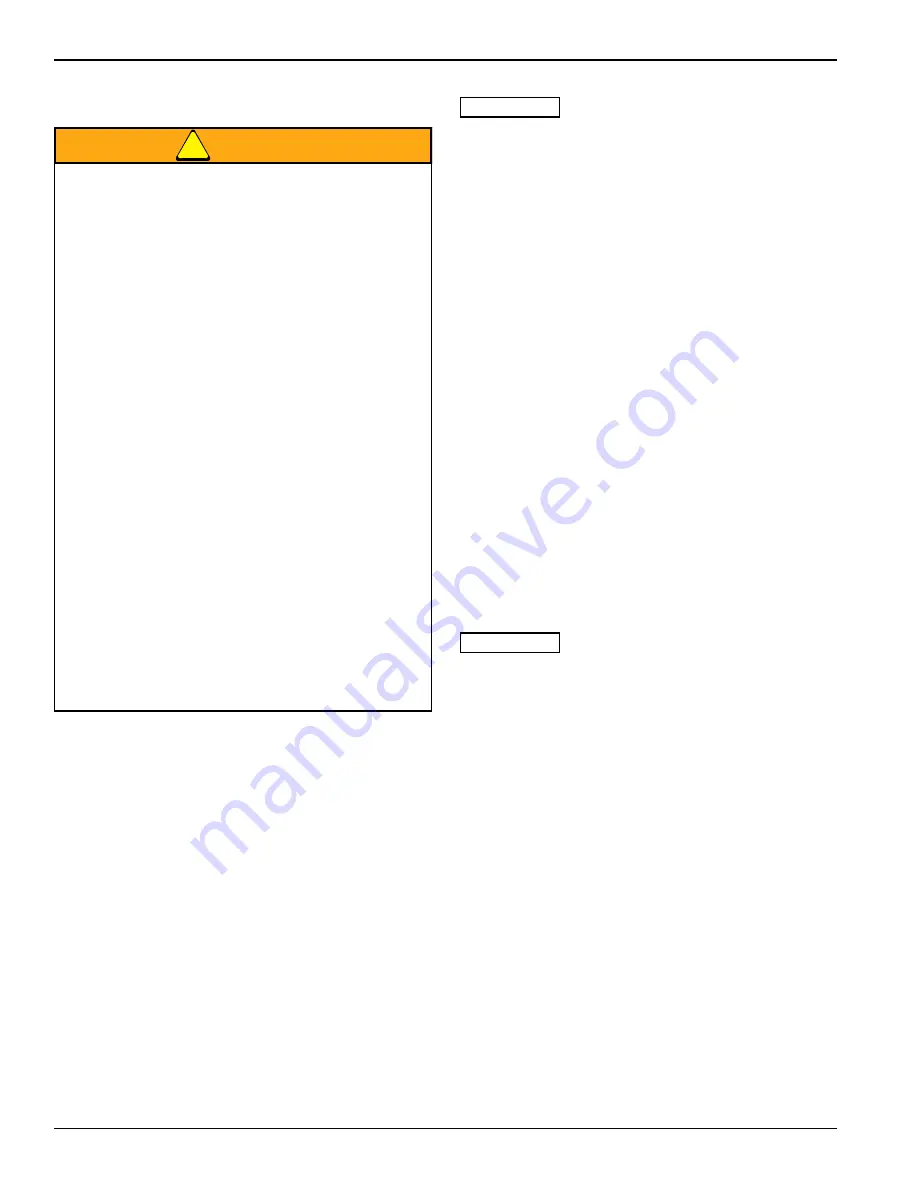
1-6
F-581-R1
INTRODUCTION, SAFETY AND INSPECTION
Mast Removal
WARNING
1.
Move the forklift to a level, designated area.
2. Turn the key off and remove it from the ignition
switch.
3.
Remove the forks.
4.
Move all levers back and forth several times to relieve
internal hydraulic pressure.
5.
Slowly and carefully remove the lift cylinder lines.
Use a container to catch oil and an oil absorbent
product to absorb any spills.
6.
Disconnect all wiring (if used) between the mast and
the forklift body.
7.
Support the mast using the sling and an overhead
hoist.
8.
Chain the individual sections of mast together at the
upper cross braces. Chain the lower mast carriage to
the lower section of the mast, keeping the sections
from moving when the mast is laid down on the floor.
9.
Remove all pins holding the tilt cylinders to the mast.
IMPORTANT
The mast is EXTREMELY heavy. Extra care should be
taken to minimize possible injury. Make sure the
hoist is rated for the weight of the mast. Make sure
the blocks you will lay the mast on can hold the
weight. Also, be SURE that no one and nothing is in
the path the mast is taking to reach the blocks.
Cleaning & Inspecting the
Forklift
Landoll Corporation recommends that their forklifts NOT
be cleaned with a power washer. Electrical boards,
circuitry and wiring can be damaged by high pressure
water and soap. Moisture and soap left on components
can rust, corrode or leave a residue that can damage
everything that it comes in contact with. The preferred
method of removing dust is compressed air. For localized
cleaning, use a non-flammable solvent parts washer and
compressed air after the part or area is cleaned.
• Always clean all metal parts with a de-greasing type
cleaner solvent and wipe dry with a clean shop rag.
• Allow parts to air dry.
• DO NOT allow cleaning solvent to come in contact
with rubber parts or rubber insulation, such as
electrical wiring, seals, etc. to avoid quicker
corrosion.
IMPORTANT
Cleaning solvents can be TOXIC and FLAMMABLE.
Pay particular attention to all WARNING labels
provided by the solvent manufacturer, such as,
protection during use, personal health precautions
and ventilation to avoid breathing vapors.
• For non-metal parts, clean using a mild soap
solution, shop vacuum for dust and loose dirt or a
dust pan and brush.
• Inspect all parts thoroughly for breaks, cracks, tears,
burrs, scoring, warping or sharp edges, glazing, rust
pitting, flat spots, etc. Notify your supervisor of all
defects and record it in the truck log book.
• Inspect all screws and hardware for stress marks,
breaks, cracks, thread defects, etc.
• Replace all damaged or questionable parts.
• Take care to properly identify and tag each part and
its order of removal. If necessary, keep notes and put
markings on all parts using a non-destructive marker,
such as a felt-tipped pen.
• When servicing the mast or sections of the
mast, hardwood blocks (4”X4”, 100 X 100mm
minimum) should be used to keep individual
sections of the mast from falling. In addition
to the hardwood blocks, chains should be
used to hold the mast sections from moving,
in both the vertical and horizontal directions.
• Mast work to be done in a flat, designated
area.
• NEVER walk under or stand upon forks.
• Remove forks before starting mast repairs.
• NEVER reach through the upright open areas
of the mast.
• NEVER maintain or repair the mast without
supports or while anyone is near the forklift.
(ASME B56.1-2000)
• Raise mast and position blocks under the
second stage mast.
• Using an appropriate set of C-clamps, secure
wooden blocks to mast channel.
• Lower mast until it sits firmly on wooden
blocks.
• For mast inspection, use only an approved
safety platform or step ladder.
• NEVER repair chains, they are to be replaced.
• NEVER replace chain sets with only one
chain. All chains are to be replaced in pairs.
Summary of Contents for Bendi B40i4
Page 2: ......
Page 26: ...1 20 F 581 R1 INTRODUCTION SAFETY AND INSPECTION...
Page 100: ...3 52 F 581 R1 TROUBLESHOOTING AND CORRECTIVE MAINTENANCE...
Page 120: ...4 20 F 581 R1 CALIBRATION AND PROGRAMMING...
Page 129: ...ENGINE WITH FUEL SYSTEM 5 9 Figure 5 10 Fuel System Troubleshooting...
Page 133: ...ENGINE WITH FUEL SYSTEM 5 13...
Page 134: ...5 14 F 581 R1 ENGINE WITH FUEL SYSTEM...
Page 140: ...6 2 F 581 R1 GM ENGINE SUPPLIER PROVIDED DOCUMENTATION...