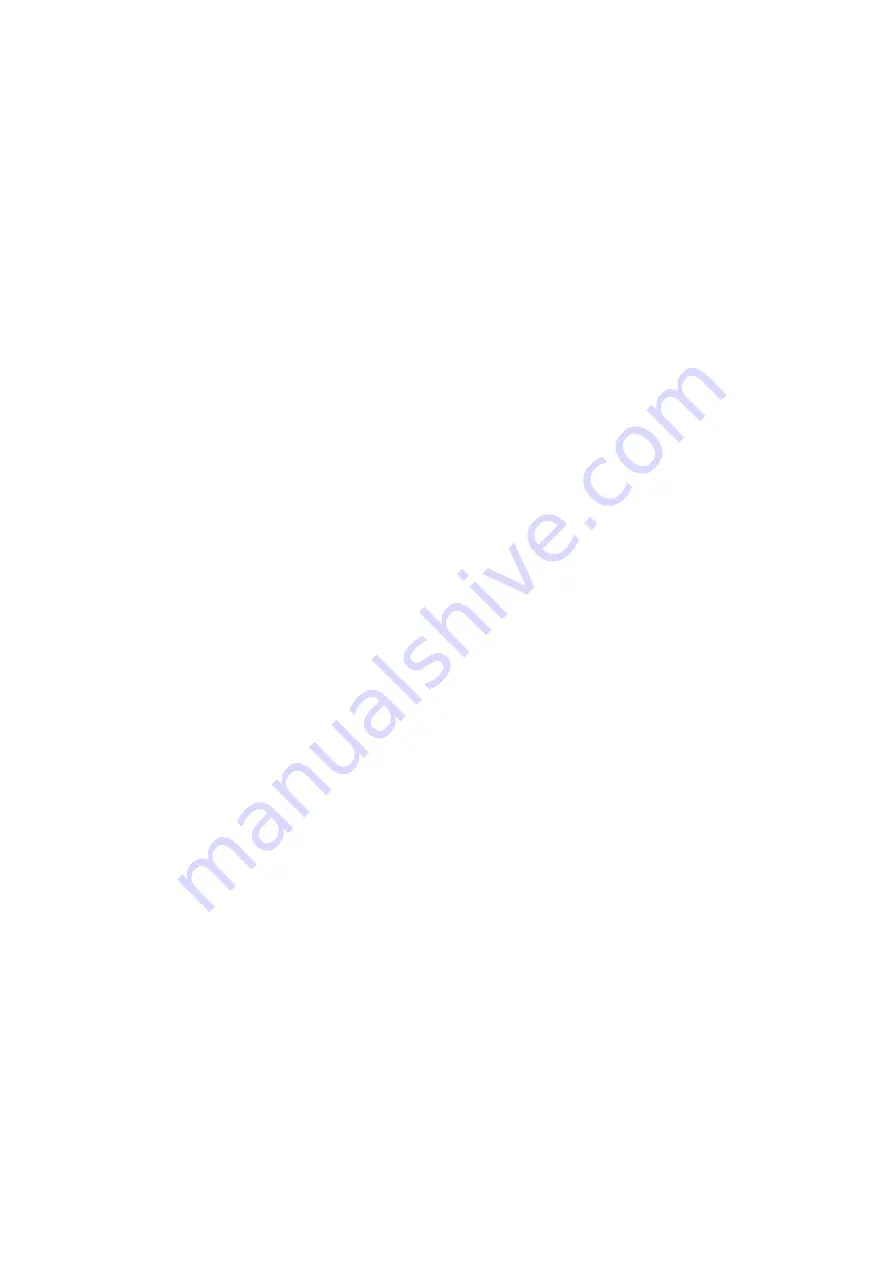
iv
9. HOW TO USE THE OPERATION PANEL (APPLICATION)
.................................... 129
9-1. Management of sewing patterns
..................................................................................129
9-1-1. Creation of a new pattern ............................................................................................... 129
9-1-2. Copying a pattern ........................................................................................................... 131
9-1-3. Deleting a pattern ........................................................................................................... 132
9-2. Setting up the polygonal-shape stitching
...................................................................133
9-2-1. Editing a polygonal-shape stitching pattern .................................................................... 133
9-2-2. Creating a new polygonal-shape stitching pattern .......................................................... 139
9-2-3. Setting the step from which polygonal-shape stitching is started ................................... 140
9-2-4. How to carry out the corner stitching using a polygonal-shape stitching pattern ............ 141
9-3-1. Selecting the cycle pattern .............................................................................................. 142
9-3-2. Editing cycle sewing data ............................................................................................... 143
9-3-3. Creating a new cycle pattern .......................................................................................... 144
9-3-4. Setting the step from which cycle sewing pattern is started ........................................... 146
9-4-1. Selecting the custom pattern .......................................................................................... 147
9-4-2. Creating a new custom pattern ....................................................................................... 149
9-4-3. Editing the custom pattern .............................................................................................. 152
9-4-4. Copying and deleting the custom pattern ....................................................................... 153
9-5. Condensation custom pattern
.....................................................................................155
9-5-1. Selecting the condensation custom ................................................................................ 155
9-5-2. Creating a new condensation custom ............................................................................. 155
9-5-3. Condensation custom edit function ................................................................................. 158
9-5-4. Copying/deleting a condensation custom ....................................................................... 159
9-6. Simple lock of the screen
.............................................................................................160
9-8. Adjustment of brightness of the LED panel
................................................................161
9-9-1. Data communication ....................................................................................................... 162
9-9-2. USB ................................................................................................................................ 165
9-9-3. NFC ................................................................................................................................ 166
9-10-1. Assignable data ............................................................................................................ 167
9-10-2. How to assign a function to a key ................................................................................. 168
9-11. Maintenance management function
..........................................................................170
10. QUICK REFERENCE CHART ACCORDING TO STITCH PITCH GAUGE (CON
VERSION TABLE OF "1 PITCH/MM")
..................................................................174
.............................................................................................175
Summary of Contents for SC-956
Page 1: ...INSTRUCTION MANUAL LH 4500C Series SC 956...
Page 180: ...175 11 GAUGE PARTS LIST 43 22 TABLE OF EXCHANGING GAUGE PARTS LH 4578C TYPE F LH 4578C F type...
Page 181: ...176 23 TABLE OF EXCHANGING GAUGE PARTS LH 4578C 7 LH 4578C 7...
Page 182: ...177 47 24 TABLE OF EXCHANGING GAUGE PARTS LH 4588C 7 LH 4588C 7...