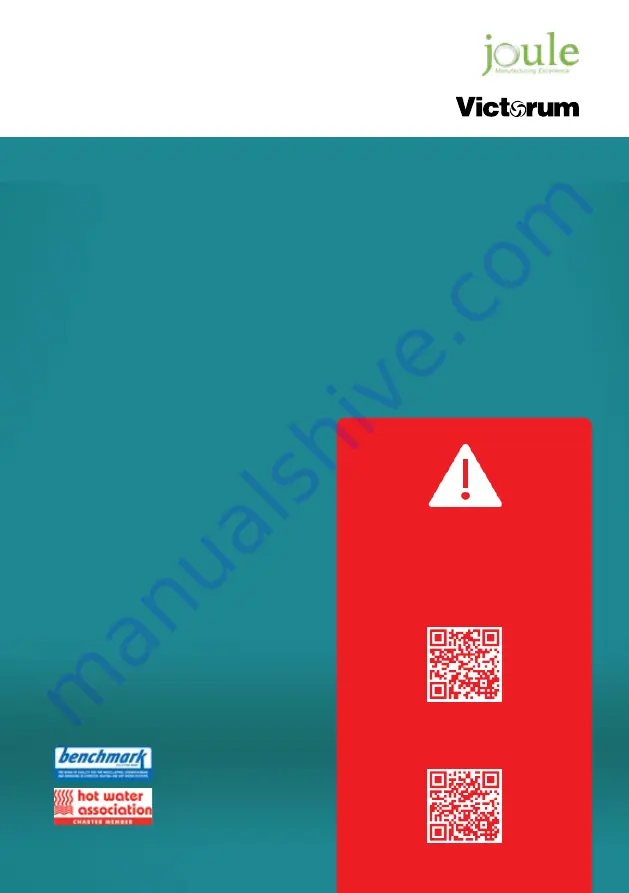
Victorum Exhaust Air Heat Pump Installation Guide
1
Victorum Pre-Plumb &
Victorum Compact Exhaust Air Heat
Pump Installation & Maintenance Manual
REGISTER THIS PRODUCT
ONLINE WITHIN 28 DAYS OF
COMMISSIONING
IRELAND
www.joule.ie/register-a-product
UNITED KINGDOM
www.jouleuk.co.uk/register-a-product
ENG-0014-7