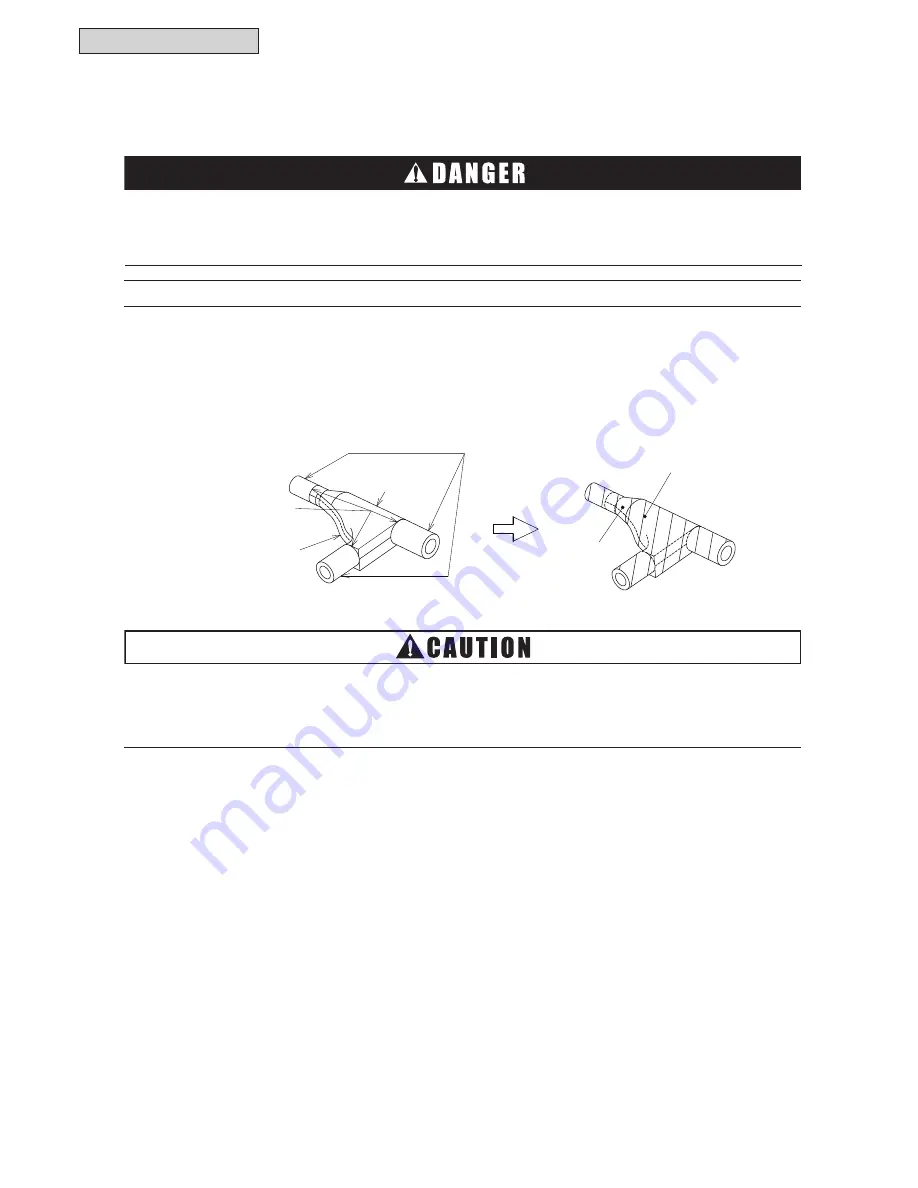
3. Make sure that all stop valves on the outdoor unit are closed completely.
4. Blow-out the inside of the pipes with nitrogen gas before brazing. Bleed nitrogen gas through refrigerant
lines when brazing. Pressure should not exceed 2.9psi (0.02MPa).
5. The airtight test pressure of this product is 601psi (4.15MPa).
6.
,QVWDOOWKH¿HOGVXSSOLHGLQVXODWLRQZLWKWKHVHPXOWLNLWVWRHDFKEUDQFKOLTXLGVLGHDQGJDVHRXVVLGHZLWK
WDSH$OVRDSSO\WKH¿HOGVXSSOLHGLQVXODWLRQIRUWKHVHXQLWV
Make sure that a test for leakage of refrigerant gases has been performed. The refrigerant used for this unit
+)&5$LVDQRQÀDPPDEOHQRQWR[LFDQGRGRURZHYHULIUHIULJHUDQWVKRXOGOHDNDQGPDNH
FRQWDFWZLWKVSDUNV¿UHWR[LFJDVZLOOEHJHQHUDWHG$OVREHFDXVHWKHÀXRURFDUERQLVKHDYLHUWKDQDLUWKH
ÀRRUVXUIDFHZLOOEH¿OOHGZLWKLWZKLFKFRXOGFDXVHVXIIRFDWLRQ
NOTE
When polyethylene foam is applied, a thickness of 13/32 inch (10mm) for liquid piping and 19/32 to 25/32 inch (15
to 20mm) for gas piping is recommended. (Use a grade of insulation with a heat resistance of 212ºF (100ºC) for
gas piping.)
Do not leave any gaps
between layers of insulation.
Insulation
(Field-Supplied)
After positioning all insulation with tape,
follow up and secure it permanently
with a second application of tape.
Insulation for Gas and
Liquid Line (Accessory)
Insulation Tape
(Field-Supplied)
Wrap insulation tape between the accessory
insulation and the field-supplied insulation.
There should be no gaps showing.
After installation, it is recommended that the customer retain this manual for future reference.
Ɣ 3HUIRUPLQVXODWLRQZRUNRQO\ZKHQWKHVXUIDFHWHPSHUDWXUHRIWKHSLSHPDWHULDOKDVFRROHGWRURRP
temperature. Anything done immediately after brazing can cause the insulation to melt.
Ɣ 'XULQJSLSLQJZRUNDOZD\VFRYHURYHURUSOXJWKHRSHQHQGWRNHHSWKHLQVLGHIUHHRIGXVWDQGPRLVWXUH
60
INSTALLATION
Summary of Contents for YVAHP0721CW Series
Page 2: ......
Page 10: ...viii SM 16007 ...
Page 14: ......
Page 15: ...SM 16007 1 1 INSTALLATION 1 Installation ...
Page 163: ...SM 16007 2 1 OPERATION 2 Operation ...
Page 164: ...2 2 SM 16007 OPERATION Ɣ 5HIHU WR WKH 6HUYLFH 0DQXDO IRU QGRRU 8QLW RU RQWUROOHU ...
Page 165: ...SM 16007 3 1 TROUBLESHOOTING 3 Troubleshooting ...
Page 284: ......
Page 285: ...SM 16007 4 1 MAINTENANCE 4 Maintenance ...
Page 360: ......
Page 390: ......
Page 391: ...SM 16007 6 1 FIELD WORK INSTRUCTIONS 6 Field Work Instructions ...
Page 400: ...6 10 SM 16007 FIELD WORK INSTRUCTIONS 0ROOLHU KDUW IRU 5 ft 3 l b ...
Page 401: ...SERVICE PARTS LIST SM 16007 7 1 7 Service Parts List ...
Page 416: ... 2016 Johnson Controls Inc SM 16007 Code No LIT 12012400 Issued November 2016 ...