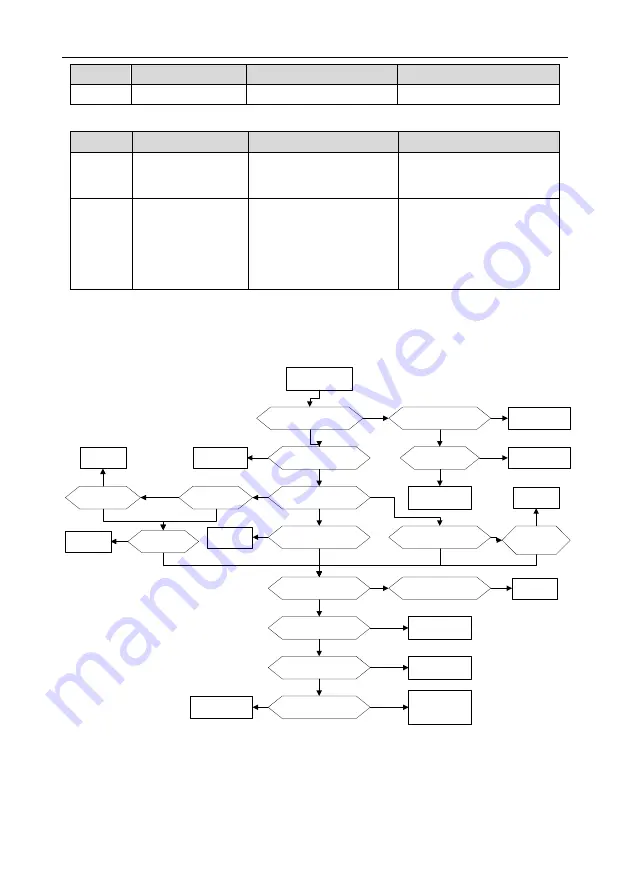
Goodrive300-19 series open loop vector inverter special for hosit Fault tracking
-196-
Code
Fault
Cause
Solution
disconnected
8.5.2 Other faults
Code
Fault
Cause
Solution
PoFF
System power
failure
The system is power-off or
the bus voltage is too low
Check the environment of the
power supply
Communication
failure between
keypad and main
control board
The keypad is not
connected properly
Check the installation
environment of the keypad
8.6 Common fault analysis
8.6.1 The motor does not work
The motor does not
rotate
If the POWER is on or not?
If there is displaying on the
keypad
If the contactor closes on
the input side
Switch on the air
contactor
Check the
voltage of RST
with multimeter
Inverter fault
Check the voltage of
the power supply
If the keypad displays the
information or not
Ensure the running
command channel
Press RUN to run
Normal running
Settle the fault
according to the
fault information
Normal running
Normal running
If the speed command
setting is right or not
Normal running
Check the voltage of
UVW with multimeter
Inverter fault
If the motor configuration
is right or not
Set a right motor
configuration
If the load is too heavy
Reduce the load if
the motor is locked
due to heavy load
Motor fault
Yes
No
No
Yes
Yes
Normal
Yes
Yes
Normal
Abnormal
Normal
Communication
Terminal
Keypad
Yes
Abnormal
No
No
No
No
No
No
Normal
Normal
Abnormal
Yes
Normal
Abnormal
Yes
Check the state of the input terminal
Reset the
parameters
if it is normal running
If the communication
configuration is right or not
If the communication
parameter is right or not?
Normal running
Normal
Abnormal
If the running is
normal or not after
switching on the
terminal
Abnormal
If the running is normal after setting
a right speed command