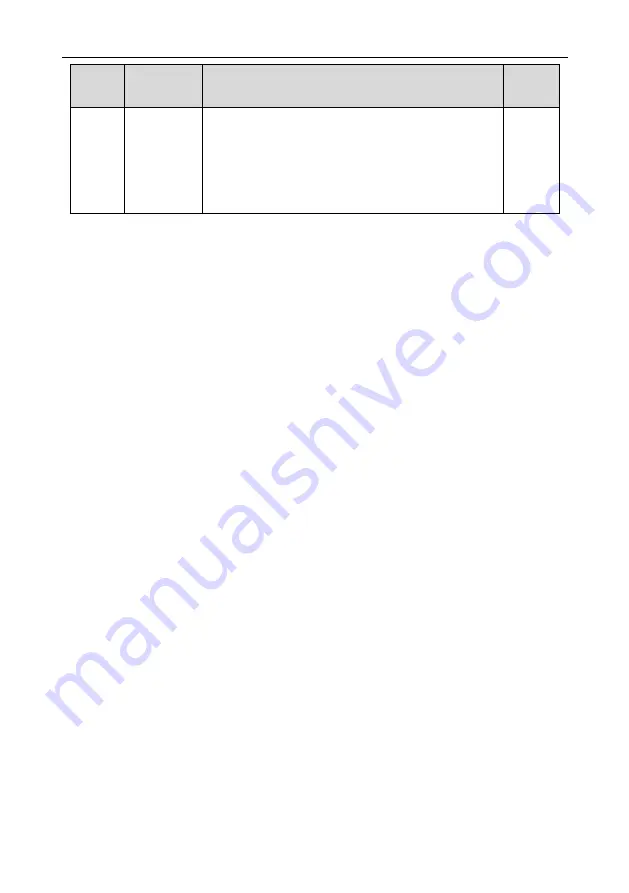
Goodrive300-19 series open loop vector inverter special for hosit Basic operation instruction
-121-
Function
code
Name
Detailed instruction of parameters
Default
value
4: Clear UP/DOWN settings
5: Coast to stop
6: Shift the reference manner of running commands
7: Quick commission mode (commission according to the
non-factory parameter)
7.3 Vector control
Because asynchronous motors have the characteristics of high stage, nonlinear, strong coupling and
various variables, the actual control of the asynchronous motor is very difficult. Vector control is
mainly used to settle this problem with the theme of that divide the stator current vector into exciting
current (the current heft generating internal magnetic field of the motor) and torque current (the
current heft generating torque) by controlling and measuring the stator current vector according to the
principles of beamed magnetic field to control the range and phase of these two hefts. This method
can realize the decoupling of exciting current and torque current to adjust the high performance of
asynchronous motors.
Goodrive300-19 series inverters are embedded speedless sensor vector control calculation. Because
the core calculation of vector control is based on exact motor parameter models, the accuracy of
motor parameter will impact on the performance of vector control. It is recommended to input the
motor parameters and carry out autotune before vector running.
Because the vector control calculation is vary complicated, high technical theory is needed for the
user during internal autotune. It is recommended to use the specific function parameters in vector
control with cautions.