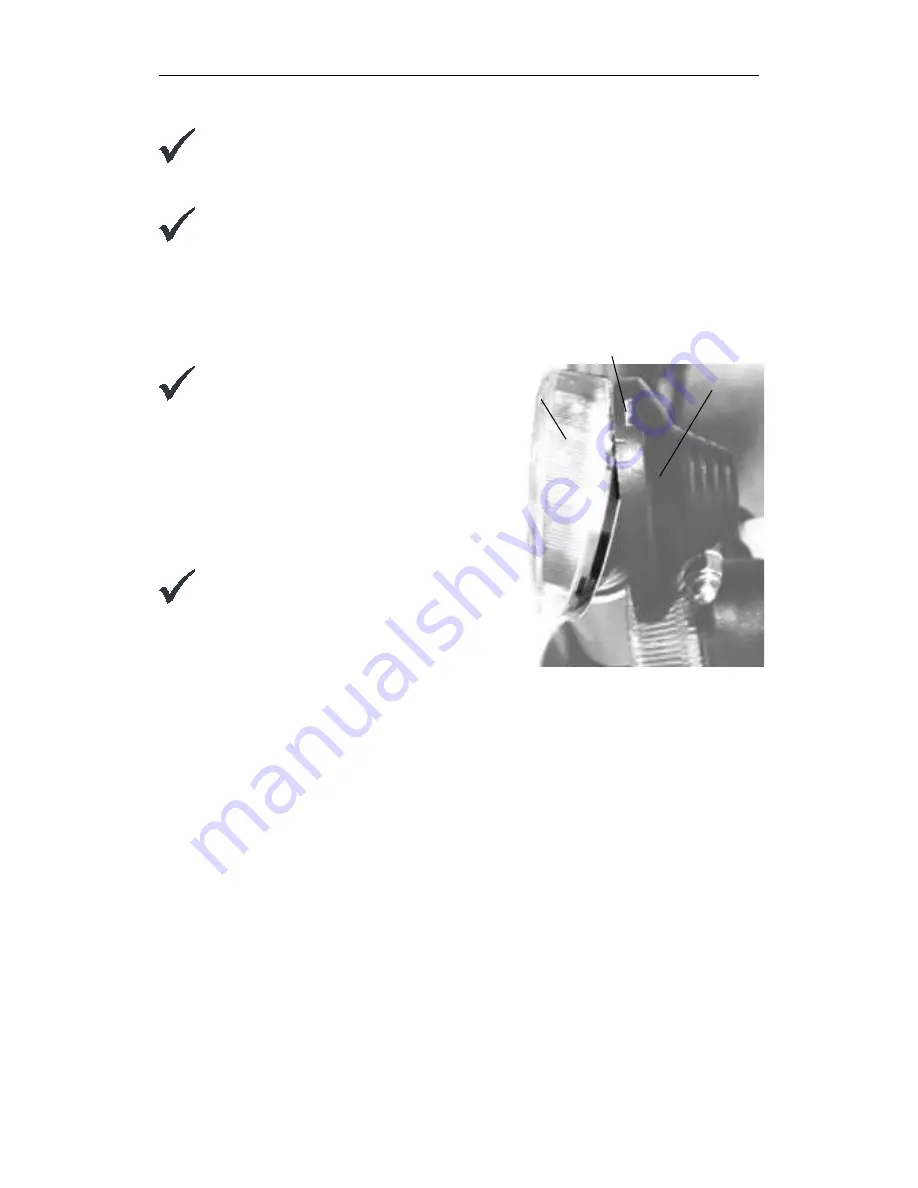
Twister / Twister Junior
Service Manual
Issued: 21.01.02
Page 145
Note
:
Make sure that the earth cable is placed inside the bulb socket and does not touch the
positive terminal (7) of the light bulb (4).
Note
:
check whether the bulb socket thread is oxidised.
For this purpose, disassemble the headlight housing (see chapt. 15.6), clean thread if
necessary and grease lightly.
15.3.3 Reassembly of headlights
•
Mount the headlight glass (1)
Note
:
The tongue in the headlight glass (1) must
engage with the headlight housing groove (5).
See also Fig. "Disassembled headlight" in
chapter 15.3.
•
Check whether the contact (7) in the headlight
housing is fitting closely to the light bulb positive
terminal (4).
•
Fasten the headlight glass (1) using the tapping
screw (2).
Note
:
The contact fits closely, when the headlight
glass (1) must be inserted with a slight
pressure.
1
5
Groove in headlight housing
Fit headlight glass