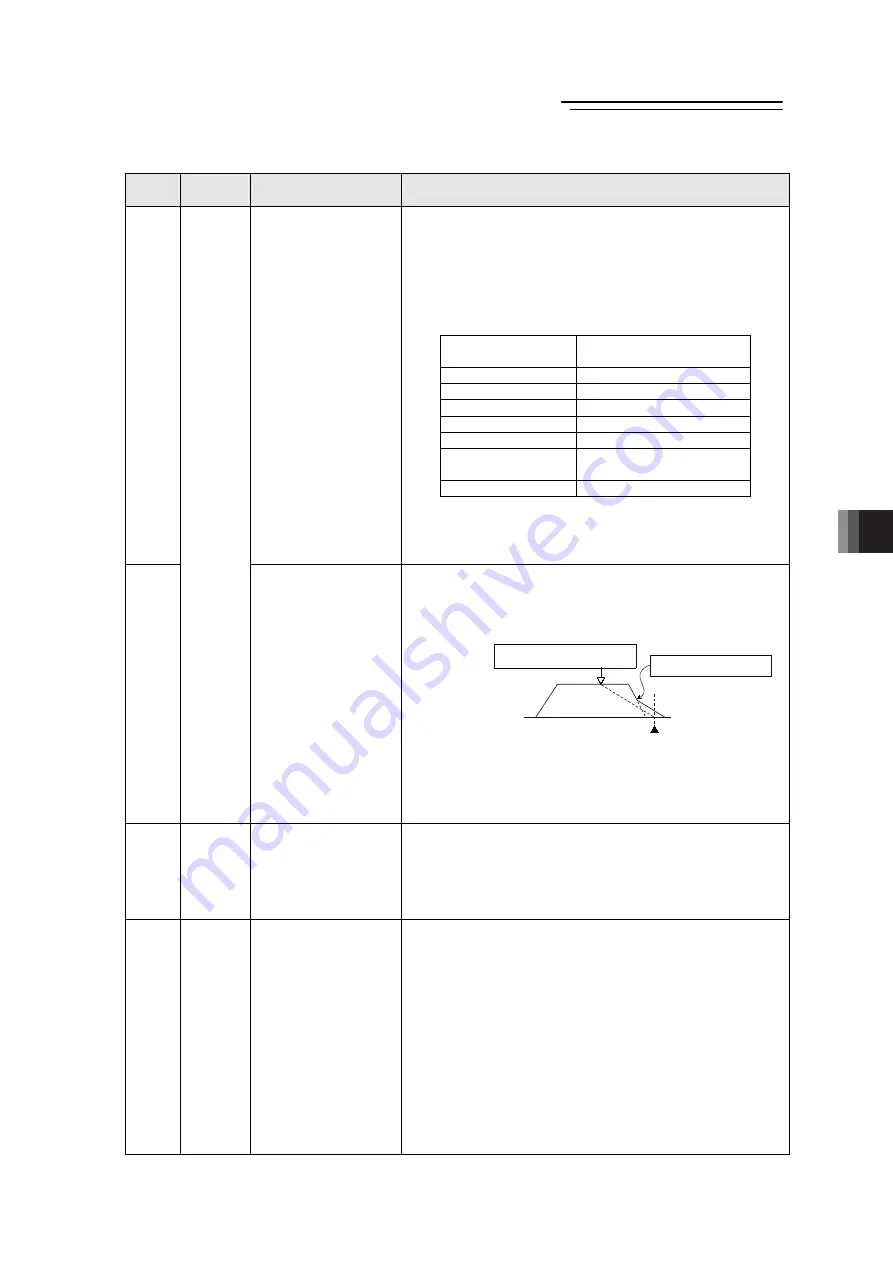
9.
Troubleshooting
Fieldbus Communication
239
RCP6S
*
In the alarm code list, description of P6PC shows RCM-P6PC, P6AC shows RCM-P6AC and P6DC shows RCM-P6DC.
Alarm
Code
Alarm
Level
Alarm Name
Cause/Treatment
0A3
Position command data
error
Cause
: 1) The command value during direct numeric
specification exceeded the maximum set value.
2) Pressing operation was specified in the field bus
specification while the vibration suppress
function remained effective.
Treatment : 1) Exceeded command item code is displayed in
the detailed address. Input an appropriate value
by referring to these values.
Detailed Address
(Command Item Code)
Command Item
0F00
Target Position
0F02
Command Speed
0F04 Acceleration
0F06 Deceleration
0F08
Positioning Width
0F0C
Pressing Current Limit
Value
0F0D
Control Signal
2) The vibration suppress control function and
pressing operation cannot be used concurrently.
Provide setting so that either of the functions is
effective.
0A7
Operation
release
Command deceleration
error
Cause
: Because there is not enough deceleration distance
when the deceleration is changed to a lower setting
during the operation, the actuator exceeded the soft
limit when deceleration was made from the current
position with the deceleration after the change.
Soft limit
Deceleration starting position
not resulting in soft limit overshoot
If a command is issued here,
soft limit overshoot will occur.
The cause is that the timing to make the next
movement command when the speed was changed
during the operation was late.
Treatment : Make the timing earlier for the movement command
for the deceleration speed change.
0A8
Cold start
Unsupported
motor/encoder types
Cause
: A motor or encoder not applicable for this controller
is connected, and the motor or encoder cannot be
classified.
Treatment : Contact us in case this alarm is issued with the
applicable actuator or occurs again even after the
power is rebooted.
0B4
For
P6AC
Only
Operation
release
Electric angling
mismatching
Cause
: 1) The position deviation counter is over-flown.
2) An error occurred in Z-axis detection. (When
detail code in error list of teaching tool is 0001
H
)
Treatment : 1) This error occurs when an actuator cannot
operate.
Confirm about the load conditions, that the work
does not interfere with any object nearby or the
brake has been released, etc.
If the error occurs even when the servo is ON,
the cable breakage or disconnection is
considered. Check the cable connection. Please
contact IAI if there is no failure in the cable and
connector connections.
2) Turn the power OFF and reboot. If the same
error occurs again, please contact IAI.
ME0349-4B
Summary of Contents for RCM-P6AC
Page 2: ......
Page 9: ...Fieldbus Communication RCP6S ME0349 4B ...
Page 32: ...Fieldbus Communication 20 RCP6S ME0349 4B ...
Page 86: ...2 Wiring Fieldbus Communication 74 RCP6S ME0349 4B ...
Page 178: ...3 Operation Fieldbus Communication 166 RCP6S ME0349 4B ...
Page 184: ...4 Vibration Suppress Control Function Fieldbus Communication 172 RCP6S ME0349 4B ...
Page 192: ...6 Power saving Function Fieldbus Communication 180 RCP6S ME0349 4B ...
Page 196: ...7 Absolute Reset Fieldbus Communication 184 RCP6S ME0349 4B ...
Page 284: ......
Page 285: ......