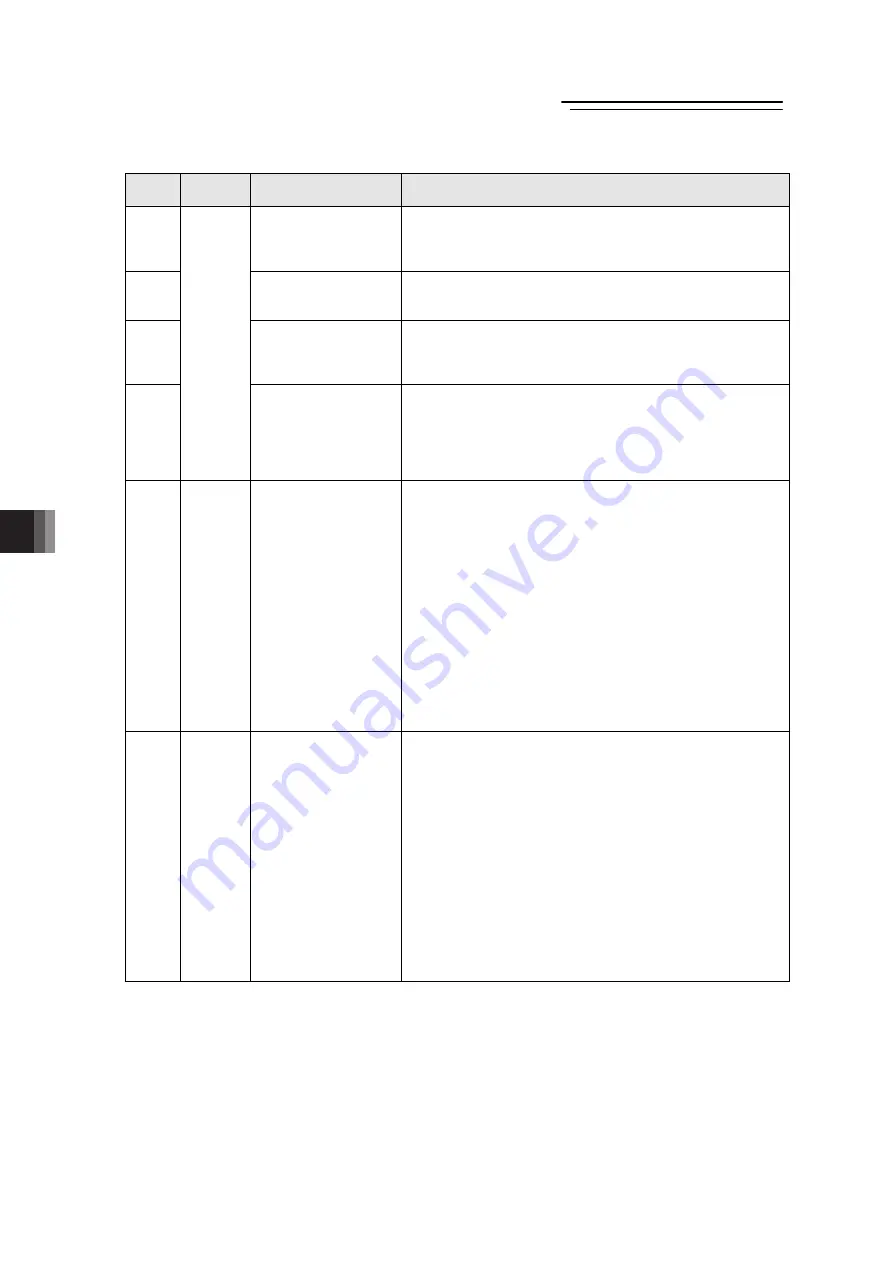
9.
Troubleshooting
Fieldbus Communication
238
RCP6S
*
In the alarm code list, description of P6PC shows RCM-P6PC, P6AC shows RCM-P6AC and P6DC shows RCM-P6DC.
Alarm
Code
Alarm
Level
Alarm Name
Cause/Treatment
090
Software reset
command in servo-ON
condition
Cause
: A software reset command was issued when the
servo was ON.
Treatment : Issue a software reset command after confirming
that the servo is OFF (SV signal is 0).
091
Position No. error in
teaching
Cause
: The position number out of the available range was
selected.
Treatment : Select the position number from 63 or smaller.
092
PWRT signal detection
during movement
Cause
: The current position write signal PWRT was input
while the actuator was jogging.
Treatment : Check that JOG+/- signal is not on and stopped
(MOVE output signal is off) before inputting.
093
Operation
release
PWRT signal detection
in incomplete home
return
Cause
: The current position write signal PWRT was input
when home return was not yet completed.
Treatment : Input the HOME signal first to perform home return,
and then input the PWRT signal after confirming
that the home return has completed (HEND output
signal is ON).
0A1
Cold start
Parameter data error
Cause
: The data input range in the parameter area is not
appropriate.
Example 1) This error occurs when the magnitude
relationship is apparently inappropriate
such as when 300mm was incorrectly
input as the value of the soft limit negative
side while the value of the soft limit
positive side was 200.3mm.
Example 2) In rotary axis, when the index mode is
changed to the normal mode and the soft
limit negative side is 0, this error is issued.
Set the soft limit negative side to a value
-0.3mm is added to the outer side of the
effective stroke. [Refer to 8.2 [2] Soft limit
positive side, Soft limit negative side]
Treatment : Change the value to the appropriate one.
0A2
Operation
release
Position data error
Cause
: 1) A move command was input when no target
position was set in the “Position” field of a
position No. in the position table.
2) The value of the target value in the “Position”
field exceeded the Parameter No.3 and 4 “Soft
limit set value”.
3) Pressing operation was specified while the
vibration suppress control function remained
effective.
Treatment : 1) Set the target position.
2) Change the target position value to the one
within the soft limit set value.
3) The vibration suppress control function and
pressing operation cannot be used concurrently.
Provide setting so that either of the functions is
effective.
ME0349-4B
Summary of Contents for RCM-P6AC
Page 2: ......
Page 9: ...Fieldbus Communication RCP6S ME0349 4B ...
Page 32: ...Fieldbus Communication 20 RCP6S ME0349 4B ...
Page 86: ...2 Wiring Fieldbus Communication 74 RCP6S ME0349 4B ...
Page 178: ...3 Operation Fieldbus Communication 166 RCP6S ME0349 4B ...
Page 184: ...4 Vibration Suppress Control Function Fieldbus Communication 172 RCP6S ME0349 4B ...
Page 192: ...6 Power saving Function Fieldbus Communication 180 RCP6S ME0349 4B ...
Page 196: ...7 Absolute Reset Fieldbus Communication 184 RCP6S ME0349 4B ...
Page 284: ......
Page 285: ......