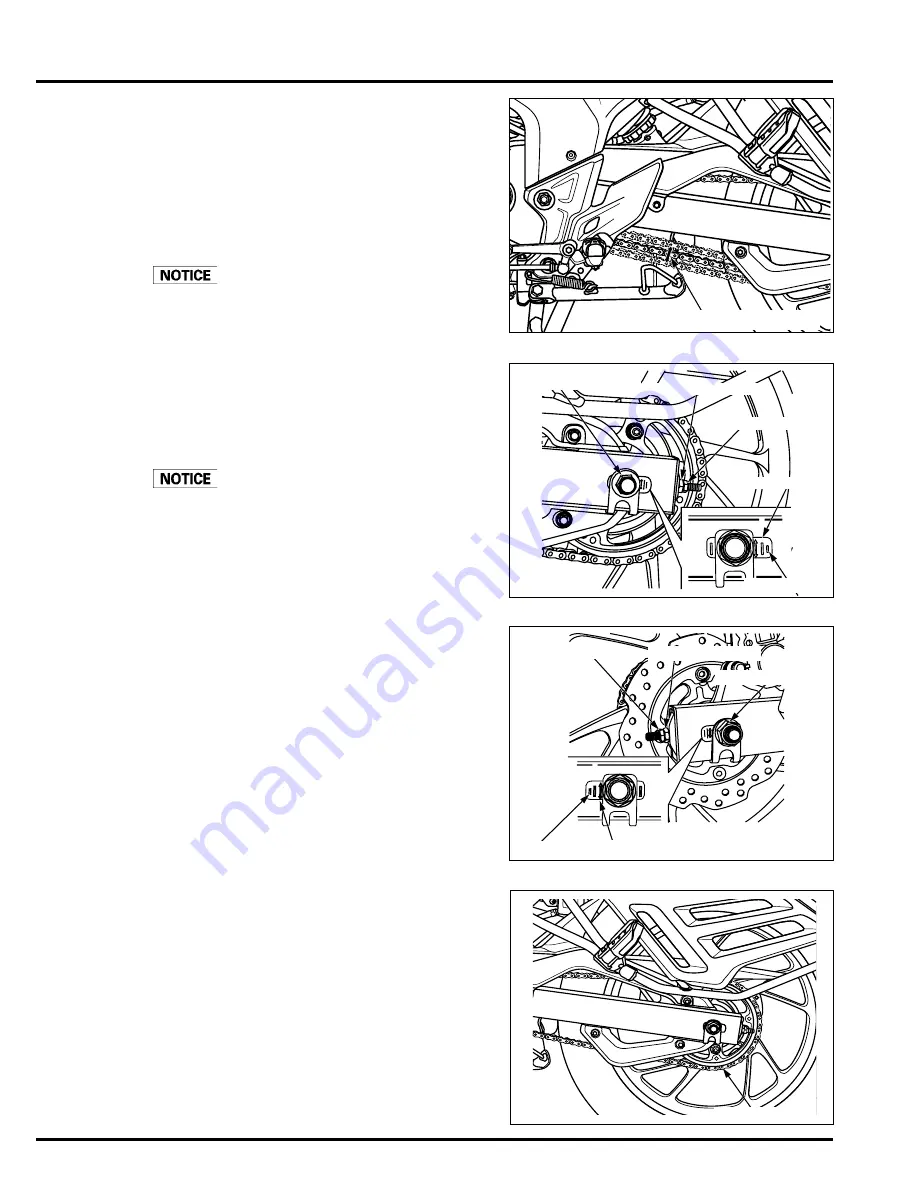
3-16
MAINTENANCE
DRIVE CHAIN
DRIVE CHAIN SLACK INSPECTION
Turn the ignition switch “OFF”. Place the motorcycle on its
center stand and shift the transmission into neutral.
Check the slack at three places in the drive chain lower
run midway between the sprockets.
CHAIN SLACKNESS: 25 – 35 mm (0.9842 – 1.37 in)
Excessive chain slack, 50 mm (1.96 in) or more, may
damage the frame.
ADJUSTMENT
Loosen the lock nut and then the adjusting nut until the
correct drive chain slack is obtained.
Align the chain adjuster index marks with the rear edge of
the adjusting slots.
Adjust the drive chain at minimum slack point.
Tighten the rear axle nut to the specified torque.
TORQUE: 88 N·m (8.8 kgf·m, 65 lbf·ft)
Tighten both adjusting nuts and lock nuts.
Recheck the drive chain slack and free wheel rotation.
Check the rear brake pedal free play (page 3-20).
CLEANING AND LUBRICATION
Turn off the ignition switch, place the motorcycle on its
center stand on a level ground and shift the transmission
into neutral.
Never inspect
the drive chain
while the engine
is running.
Never adjust the
drive chain while
the engine is
running.
ADJUSTING NUT
ADJUSTING NUT
LOCK NUT
LOCK NUT
REAR AXLE SHAFT
REAR AXLE NUT
INDEX MARK
INDEX MARK
REAR EDGE
REAR EDGE
DRIVE CHAIN
25-35 mm (0.9842 - 1.37in)
Summary of Contents for CB HORNET 160R 2015
Page 1: ...SHOP MANUAL CB HORNET 160R CB HORNET 160R...
Page 38: ...MEMO...
Page 71: ...MEMO...
Page 72: ...5 0 FUEL SYSTEM 27 N m 2 8 kgf m 20 Ibf ft COMPONENT LOCATION...
Page 127: ...MEMO...
Page 128: ...8 0 CYLINDER PISTON COMPONENT LOCATION...
Page 137: ...MEMO...
Page 154: ...10 0 ALTERNATOR 74 N m 7 5 kgf m 55 Ibf ft COMPONENT LOCATION...
Page 243: ...MEMO...
Page 299: ...MEMO...
Page 319: ...MEMO...
Page 326: ...MEMO...
Page 327: ...19 WIRING DIAGRAM 19 1 STANDARD AND CBS CB HORNET 160R 19 1...
Page 333: ...MEMO...
Page 336: ...Honda Motor Co Ltd 2015 82K43P0 Published by Honda Motorcycle Scooter India Pvt Ltd...