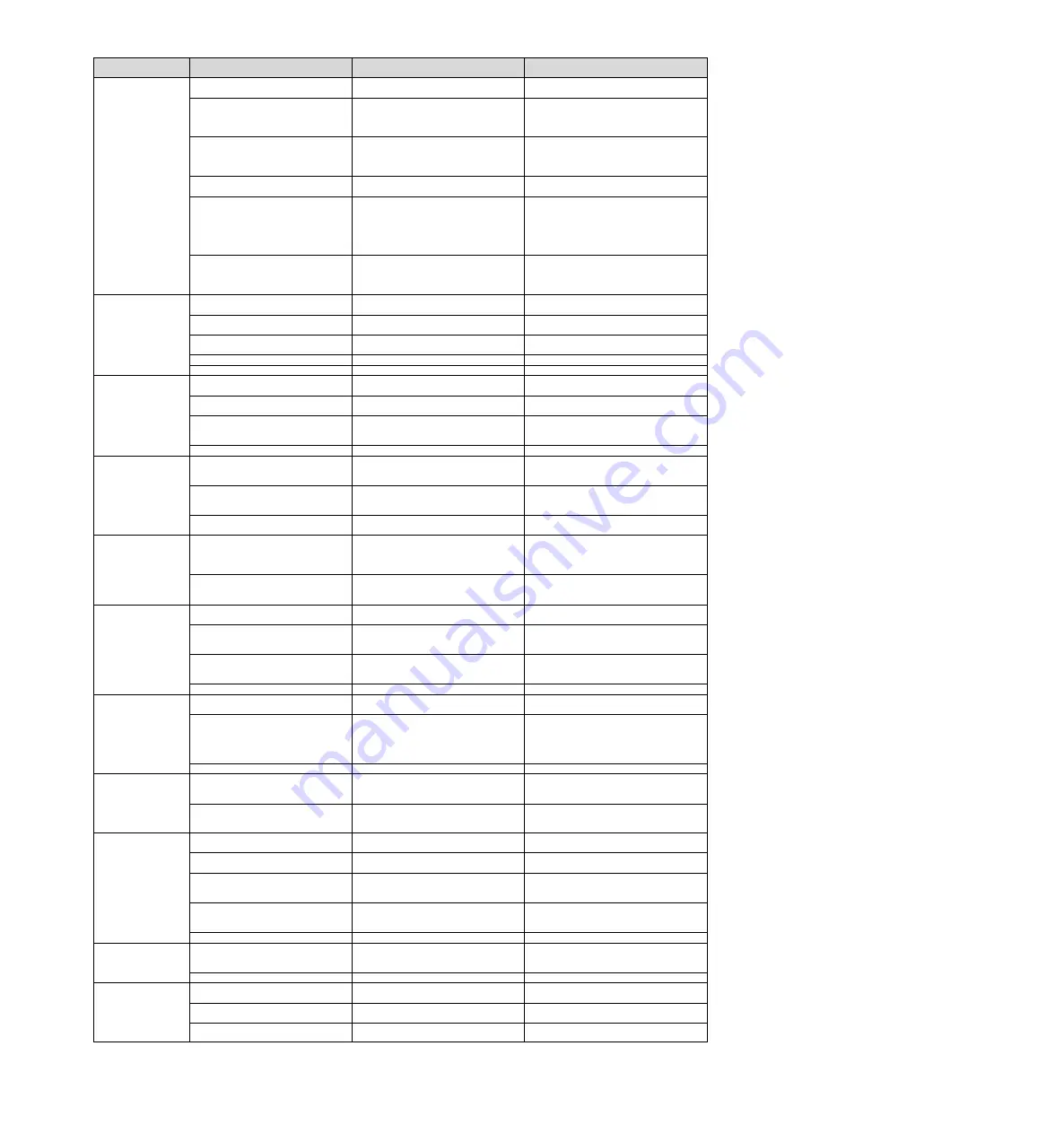
73
Alarm number:
Alarm name
Reason
Confirmation method
The treatment measures
A.400
:
Overvoltage
(Overvoltage Detected
by Main Circuit Power
Supply in Servo Drive)
Power
supply
voltage
exceeds
specification range
Measure the supply voltage.
Adjust the AC/DC power supply voltage to the
product specifications.
The power supply is in an unstable state
or is affected by lightning strike
Measure the supply voltage.
Improve the power supply condition and
switch on the servo drive power again after
installing surge suppressor. When an alarm
still occurs, replace the servo drive.
When the AC power supply voltage
exceeds
the
specification
range,
acceleration and deceleration are carried
out
Confirm the power supply voltage, speed
and torque in operation.
Adjust the AC power supply voltage to the
product specifications.
External regenerative resistance value is
larger than operating conditions
Confirm the operating conditions and
regenerative resistance value.
Confirm that the rotational inertia ratio or mass
ratio is within the allowable range.
Operate in a state where the allowable
moment of inertia ratio or mass ratio is
above the allowable moment of inertia
ratio or mass ratio to confirm that the
moment of inertia ratio or mass ratio is
within the tolerance
Confirm that the rotational inertia ratio or
mass ratio is within the allowable range.
Extend deceleration time or reduce load.
Servo drive failure
-
In the state that the main loop power supply is
not turned on, the servo drive control power
supply is turned on again. When an alarm still
occurs, replace the servo drive.
A.410
:
Under voltage
(The power supply part
of the main loop inside
the servo drive detects
the undervoltage)
Supply voltage below specification
Measure the power supply voltage.
Adjust the power supply voltage to the normal
range
Power supply voltage drops during
operation
Measure the power supply voltage.
Increase power supply capacity.
Instantaneous power failure occurred
Measure the power supply voltage.
If the instantaneous stop holding time (Pn509)
is changed, it is set to a smaller value.
Servo drive fuse blown
-
Replace the servo drive
Servo drive failure
-
Replace the servo drive.
A.510
:
Over speed
(Motor speed is above
the highest speed)
U, V, W phase sequence error of motor
wiring
Confirm the connection of servo motor.
Confirm whether there is any problem with the
motor wiring.
The command input value exceeds the
overspeed value
Confirm the input command.
Lower the command value. Or adjust the gain.
The motor speed exceeds the maximum
speed
Confirm the waveform of motor speed.
Reduce the speed command input gain and
adjust the servo gain. Or adjust operating
conditions.
Servo drive failure
-
Replace the servo drive.
A.520
:
Vibration alarm
Abnormal vibration of motor speed is
detected
Confirm the abnormal sound of the motor
and the speed and torque waveforms
during operation.
Reduce motor speed. Or reduce the speed
loop gain (Pn100).
The value of the moment of inertia ratio
(Pn103) is larger than the actual value or
varies greatly
Confirm the moment of inertia ratio or mass
ratio.
Correctly set the moment of inertia ratio
(Pn103).
Vibration detection value (Pn312) is
inappropriate
Verify that the vibration detection value
(Pn312) is appropriate.
Set the vibration detection value appropriately
(Pn312).
A.521
:
Automatically
adjust
alarm
(Custom adjustments,
EasyFFT,
no
adjustment
Vibration
detected in function)
The motor vibrates greatly when using
the adjustment-free function
Confirm the waveform of motor speed.
Reduce the load below the allowable moment
of inertia ratio, or increase the load value set
by the adjustment-free value to reduce the
rigidity value.
The motor vibrates greatly when custom
adjustment and EasyFFT are performed. Confirm the waveform of motor speed.
The processing method described in the
operation steps for implementing each
function.
A.710
:
Overload
(instantaneous
maximum load)
A.720
:
Overload
(continuous
maximum load)
Motor wiring, encoder wiring or poor
connection
Confirm wiring.
Confirm whether there is any problem with
motor wiring and encoder wiring.
The operation of the motor exceeds the
overload protection characteristic
Confirm the overload characteristics and
operation commands of the motor.
Discuss load conditions and operating
conditions again. Or reconsider the motor
capacity.
The motor is not driven due to
mechanical
factors,
resulting
in
excessive load during operation
Confirm the operation command and motor
speed.
Improve mechanical factors.
Servo drive failure
-
Replace the servo drive.
A.730
:
A.731
:
DB overload
(Excessive
power
consumption
of
dynamic
brake
detected)
The motor is being driven by external
force
Confirm operation status.
Do not drive the motor by external force.
The rotating or operating energy when
DB stops exceeds the capacity of DB
resistor
The usage frequency of DB is confirmed by
the power consumption of DB resistor.
Try the following measures.
• Reduce the command speed of servo motor.
• Reduce the rotational inertia ratio or mass
ratio.
• Reduce the number of DB stops.
Servo drive failure
-
Replace the servo drive.
A.740: Impulse Current
Limiting
Resistance
Overload
(The main circuit power
on frequency is too
high)
The allowable number of inrush current
limiting resistors when the main loop
power supply is ON/OFF is exceeded
-
Lower the ON/OFF frequency of the main loop
power supply.
Servo drive failure
-
Replace the servo drive.
A.810
:
Encoder backup alarm
(only detected when
absolute value encoder
is connected
(Detected on encoder
side
Turn on the power supply of absolute
value encoder for the first time
Confirm whether the power is switched on
for the first time.
Setting operation of encoder is carried out
The encoder cable was removed and
then connected
Confirm whether the power is switched on
for the first time.
Confirm the connection of the encoder and set
the encoder.
The servo drive control power supply
(+5V) and battery power supply have
both failed
Verify that the encoder connector battery
and connector status are correct.
After power supply to the encoder is restored
(battery replacement, etc.), the encoder is set
up.
Absolute value coder fault
-
When the alarm cannot be released even if
the setting operation is performed again,
replace the servo motor.
Servo drive failure
-
Replace the servo drive.
A.820
:
Encoder and check
alarm (Detected
on
encoder side
)
Encoder failure
-
Reset encoder. When it still occurs frequently,
it is possible that the servo motor fails.
Replace the servo motor.
Servo drive failure
-
Replace the servo drive.
A.830
:
Encoder battery alarm
(The absolute value
encoder battery voltage
is below the specified
value)
The battery is not well connected and not
connected
Confirm battery connection.
Connect the battery correctly.
The battery voltage is lower than the
specified value (2.7 V)
Measure the battery voltage.
Replace the battery.
Servo drive failure
-
Replace the servo drive.