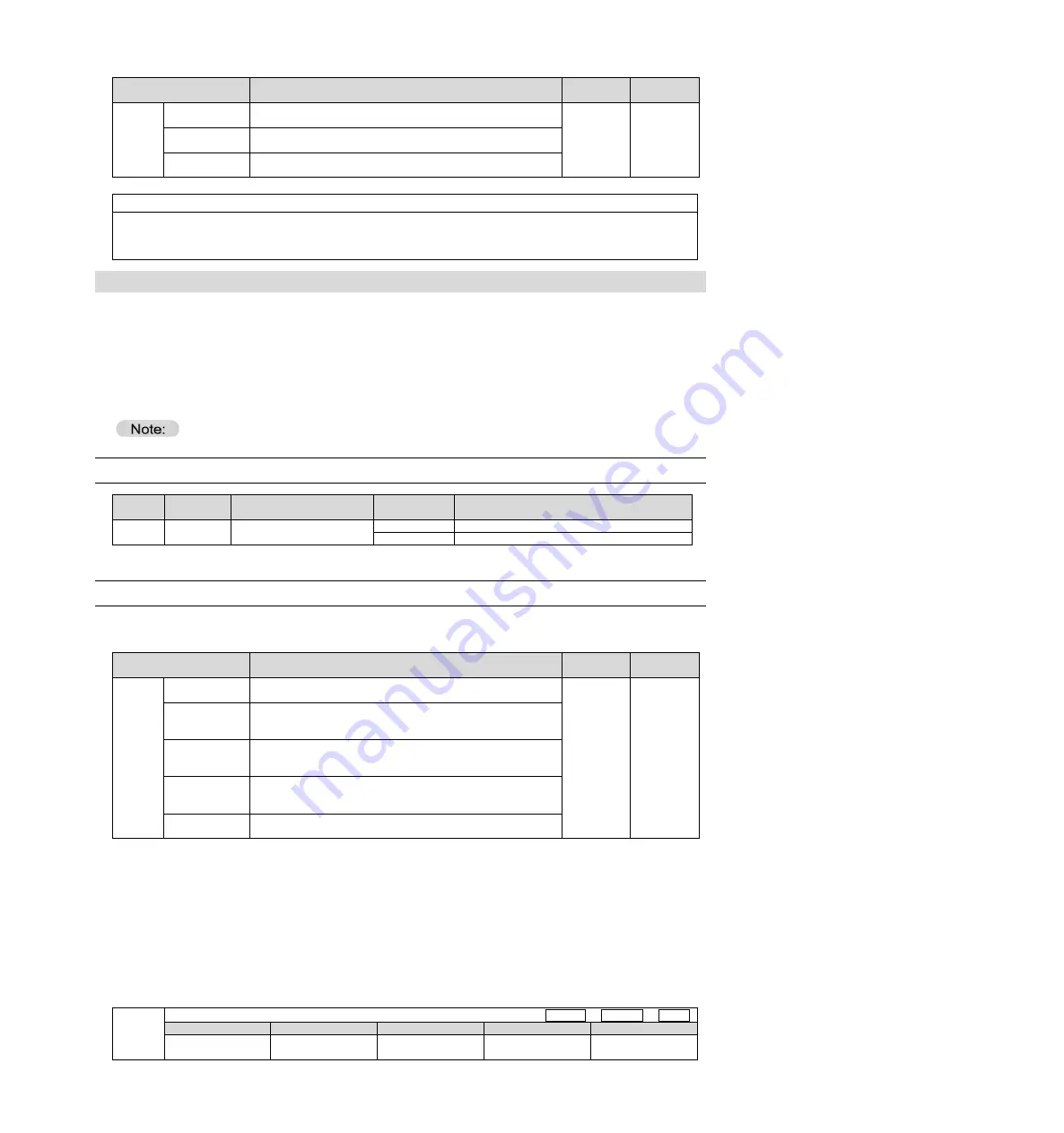
51
Parameter setting when using multiple coil absolute value encoder
Parameter
Meaning
Effective
time
Category
Pn002
n.
0
[Factory setting]
Used as multiple coils absolute value encoder.
A battery is needed.
Power
restart
Setup
n.
1
Used as incremental encoder.
No battery is required
n.
2
Used as 1 coil absolute value encoder.
No battery is required.
Notice
Please install the battery on either side of the upper device or encoder cable.
If batteries are installed on the upper device and encoder cable at the same time, a circulation loop will be formed
between the batteries, resulting in product damage or burning.
6.9 Forced stop function
The forced stop function refers to the function of forcibly stopping the servo motor by a signal from an upper
device or an external device.
When forced stop is used, distribution of the forced stop input (FSTP) signal (Pn516 = n.
X) is required.
There are three methods for stopping the motor: dynamic brake (DB) stop, free running stop and deceleration
stop.
(Note) The forced stop function is different from the hardware base blocking (HWBB) function and is not a function specified in the
safety standard. Please note.
Panel display and operator display
When forced to stop, "FSTP" will be displayed on the panel display and the digital operator.
6.9.1 Forced Stop Input (FSTP) Signal
Type
Signal
name
Connector pin number
Signal status
Meaning
Input
FSTP
Distribution required
ON (closed)
Driveable (normal operation)
OFF (OFF)
The motor stopped running.
(Note) FSTP signal needs to be distributed. It can be distributed to terminals through Pn516 = n.
X (distribution of forced stop
input (FSTP) signal).
6.9.2 Selection of Stop Method for Forced Stop Function
The stop method of the forced stop function is selected through Pn00A=n.
X
(stop method at forced
stop).
Parameter
Meaning
Effective
time
Category
Pn00A
n.
0
DB stop or free operation stop (stop method is the same as
Pn001 = n.
X).
Power
restart
Setup
n.
1
[Factory
setting]
The set torque of Pn406 is used as the maximum torque to
decelerate and stop the motor. The state after stopping
depends on the setting of Pn001 = n.
X.
n.
2
The set torque of Pn406 is taken as the maximum torque to
decelerate and stop the motor, and then enter the free running
state.
n.
3
According to the deceleration time of Pn30A, the motor is
decelerated and stopped. The state after stopping depends on
the setting of Pn001 = n.
X
n.
4
According to the deceleration time of Pn30A, the motor will
decelerate and stop, and then enter the free running state.
(Note) During torque control, deceleration cannot be stopped. According to the setting of Pn001 = n.
X (servo OFF and stop
method in case of Gr.1 alarm), the dynamic brake stops or the free operation stops.
When the emergency stop torque (Pn406) is set to stop the servo motor
When the emergency stop torque is set to stop the servo motor, Pn406 (Emergency Stop Torque) is set.
When Pn001=n.
X
is set to 1 or 2, the servo motor will be decelerated with the set torque of Pn406 as the
maximum value.
The factory setting is "800%". This is a large enough value to ensure that the servo motor must output
maximum torque. However, the actual effective maximum limit of emergency stop torque is the maximum
torque of the servo motor.
Pn406
Emergency stop torque
Speed
Position
Torque
Setting range
Setting Unit
Factory setting
Effective time
Category
0
~
800
1% *
800
Effective
immediately
Setup