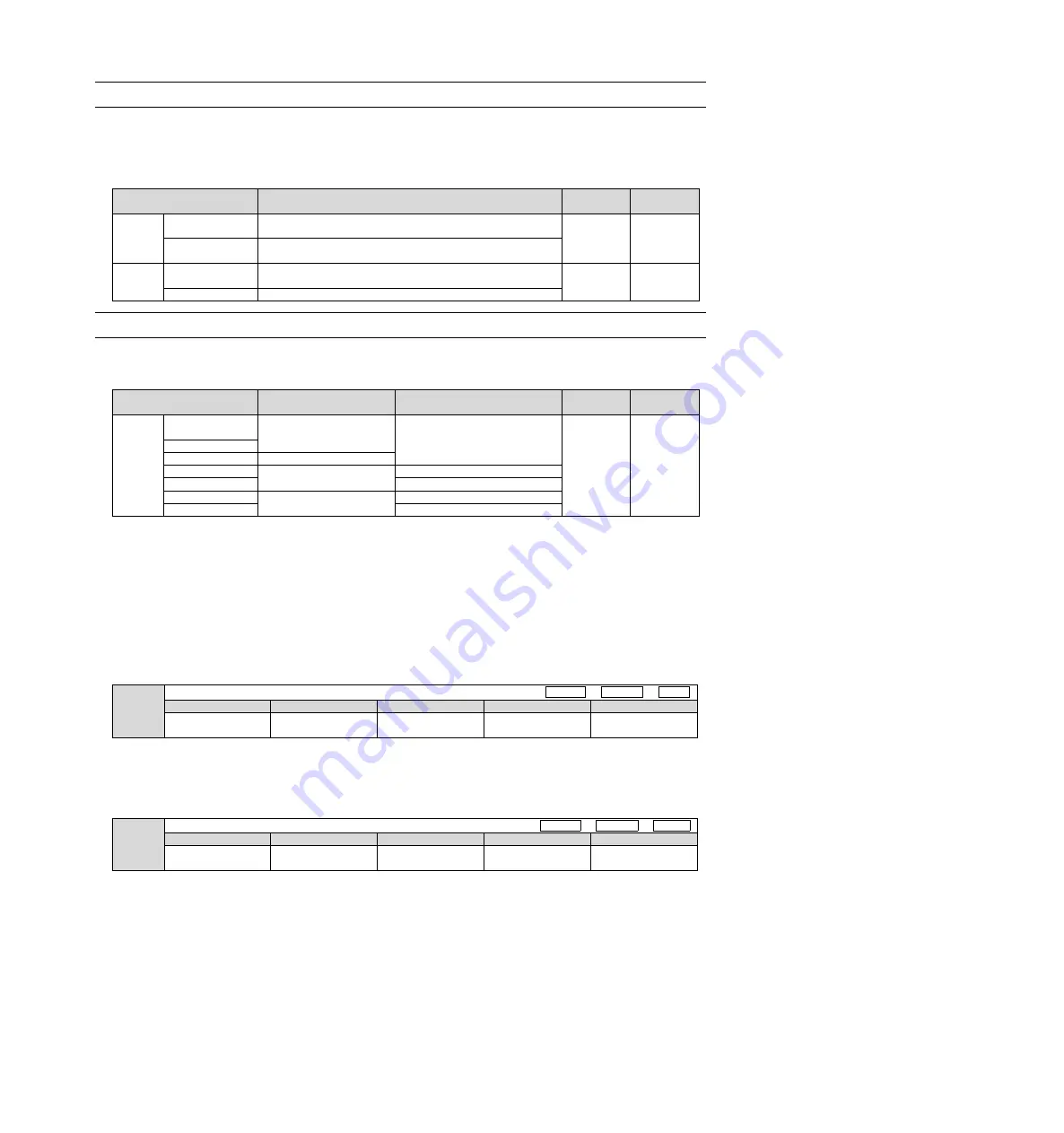
28
Even in the over-travel state, it is still allowed to drive in the opposite direction by inputting command.
5.8.2 Select whether the over-travel prevention function is valid/invalid
The valid/invalid over-travel prevention function can be selected by PN50A = n.X
(prohibiting the
distribution of the forward-rotation-side drive input (P-OT) signal) and PN50B = n.
X (prohibiting the
distribution of the reverse-rotation-side drive input (N-OT) signal).
When the selection is invalid, there is no need to connect the input signal for over-travel prevention.
Parameter
Meaning
Effective
time
Category
Pn50A
n. 2
[Factory setting]
After the overtravel function takes effect, input the No Forward
Drive Input (P-OT) signal from CN1-IN2.
Power
restart
Setup
n. 8
Overtravel function fails. Forward rotation side drive is always
allowed.
Pn50B
n
3
[Factory setting]
After the overtravel function takes effect, input the drive input
(N-OT) signal from CN1-IN3 on the reverse side.
Power
restart
Setup
n.
8
Overtravel function fails. Reverse side drive is always allowed.
5.8.3 Selection of Motor Stopping Method for Over-travel Prevention Function
The servo mOTor stop method when the overtravel prevention function operates is selected by Pn001 = n
XX (stop method when servo OFF and Gr.1 alarm occurs, stop method when overtravel (ot)).
Parameter
Stop method of motor *
Turn state after motor stops
Effective
time
Category
Pn001
n.
00
[Factory setting]
Dynamic brake
Free-running operation
Power
restart
Setup
n.
01
n.
02
Free-running operation
n.
1
Decelerate according to
Pn406 setting
Zero position fixing
n.
2
Free-running operation
n.
3
Decelerate according to
Pn30A setting
Zero position fixing
n.
4
Free-running operation
* Torque control cannot slow down to stop. According to the setting of Pn001 = n.
X (servo OFF and stop method in
case of Gr.1 alarm), the dynamic brake stops or the free running stops, and enters the free running state after the servo
motor stops.
When the emergency stop torque is set to stop the servo motor
When the emergency stop torque is set to stop the servo motor, Pn406 (Emergency Stop Torque) is set.
When Pn001 = n.
X
is set to 1 or 2, the servo motor will be decelerated with the set torque of Pn406 as
the maximum value.
The factory setting is "800%". This is a large enough value to ensure that the servo motor must output
maximum torque. However, the actual effective maximum limit of emergency stop torque is the maximum
torque of the servo motor.
Pn406
Emergency stop torque
Speed
Position
Torque
Setting range
Setting Unit
Factory setting
Effective time
Category
0
〜
800
1% *
800
Effective
immediately
Setup
* Percentage relative to rated torque of motor.
When the deceleration time is set to stop the servo motor
When setting the deceleration time of the servo motor to stop the servo motor, Pn30A (deceleration time at
servo OFF and forced stop) is set.
Pn30A
Deceleration Time for Servo OFF and Forced Stop
Speed
Position
Torque
Setting range
Setting Unit
Factory setting
Effective time
Category
0
〜
10000
1ms
0
Effective
immediately
Setup
When Pn30A is set to "0", zero speed stops.
The deceleration time set by Pn30A is the time from the highest speed of the motor to the stop of the motor.