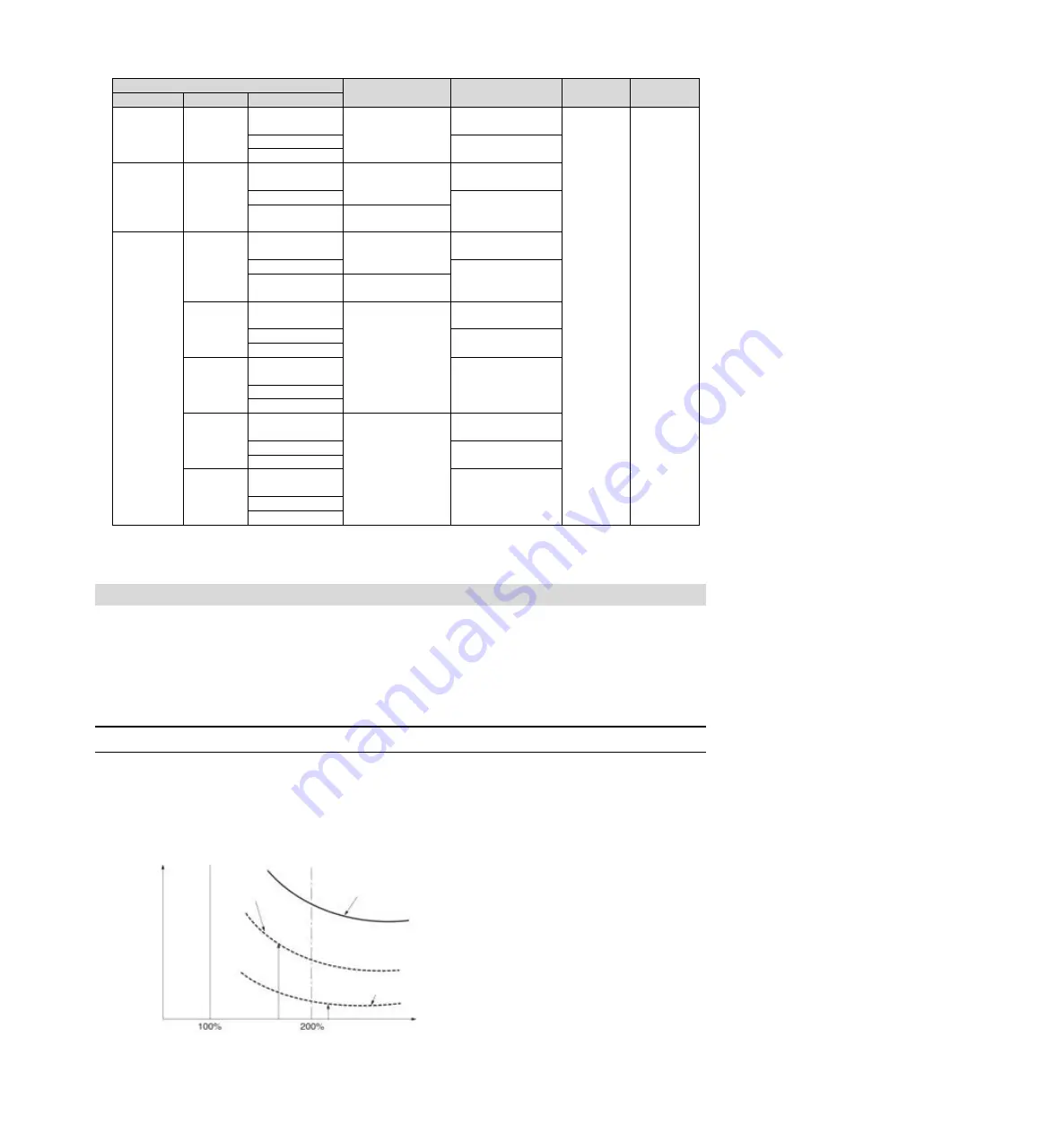
34
The combination and stopping method of parameter setting contents are described in the following table.
Parameter
Stop method Servo
motor
State after the servo
motor stops
Effective
time
Category
Pn00B
Pn00A
Pn001
n.
0
[Factory
setting]
---
n.
0
[Factory setting]
Zero speed
Dynamic brake
Power
restart
Setup
n.
1
Free-running
operation
n.
2
n.
1
n.
0
[Factory setting]
Dynamic brake
Dynamic brake
n.
1
Free-running
operation
n.
2
Free-running
operation
n.
2
n.
0
[Factory
setting]
n.
0
[Factory setting]
Dynamic brake
Dynamic brake
n.
1
Free-running
operation
n.
2
Free-running
operation
n.
1
n.
0
[Factory setting]
Taking the set
torque of Pn406 as
the maximum
value to decelerate
the motor
Dynamic brake
n.
1
Free-running
operation
n.
2
n.
2
n.
0
[Factory setting]
Free-running
operation
n.
1
n.
2
n.
3
n.
0
[Factory setting]
Decelerate the
motor according to
the setting of
Pn30A
Dynamic brake
n.
1
Free-running
operation
n.
2
n.
4
n.
0
[Factory setting]
Free-running
operation
n.
1
n.
2
(Note) 1. When Pn001 = n.
0
or n.
1
, the setting of Pn00A will be ignored.
2. The setting of PN00A = n.
X is only valid for position control and speed control. The setting of Pn00A=n.
X will
be ignored during torque control, and the setting of Pn001 = n.
X will be followed.
5.11 Motor overload detection value
Motor overload detection value refers to the value (threshold) of detecting overload warning and overload
alarm when continuous load exceeding the rated value of servo motor is applied. Which can prevent the servo
motor from overheating.
Servo drive can change the detection time of A.910 (overload warning) and A.720 (overload (continuous
maximum) alarm). However, the detected value of A.710 (overload characteristic and overload (instantaneous
maximum) alarm) cannot be changed.
5.11.1 Detection time of overload warning (A.910)
The overload warning detection time at the factory is 20% of the overload warning detection time. By changing
the overload warning value (Pn52B), the overload warning detection time can be changed. This function can
be used as overload protection function of the used system to improve safety.
For example, as shown in the following figure, when the overload warning value (Pn52B) is changed from 20%
to 50%, the overload warning detection time will become half (50%) of the overload warning detection time.
Overload detection time
Pn52B=50%
overload warning
detection curve
Overload alarm
detection curve
Torque command [%]
Pn52B=20% (factory set) overload
warning detection curve