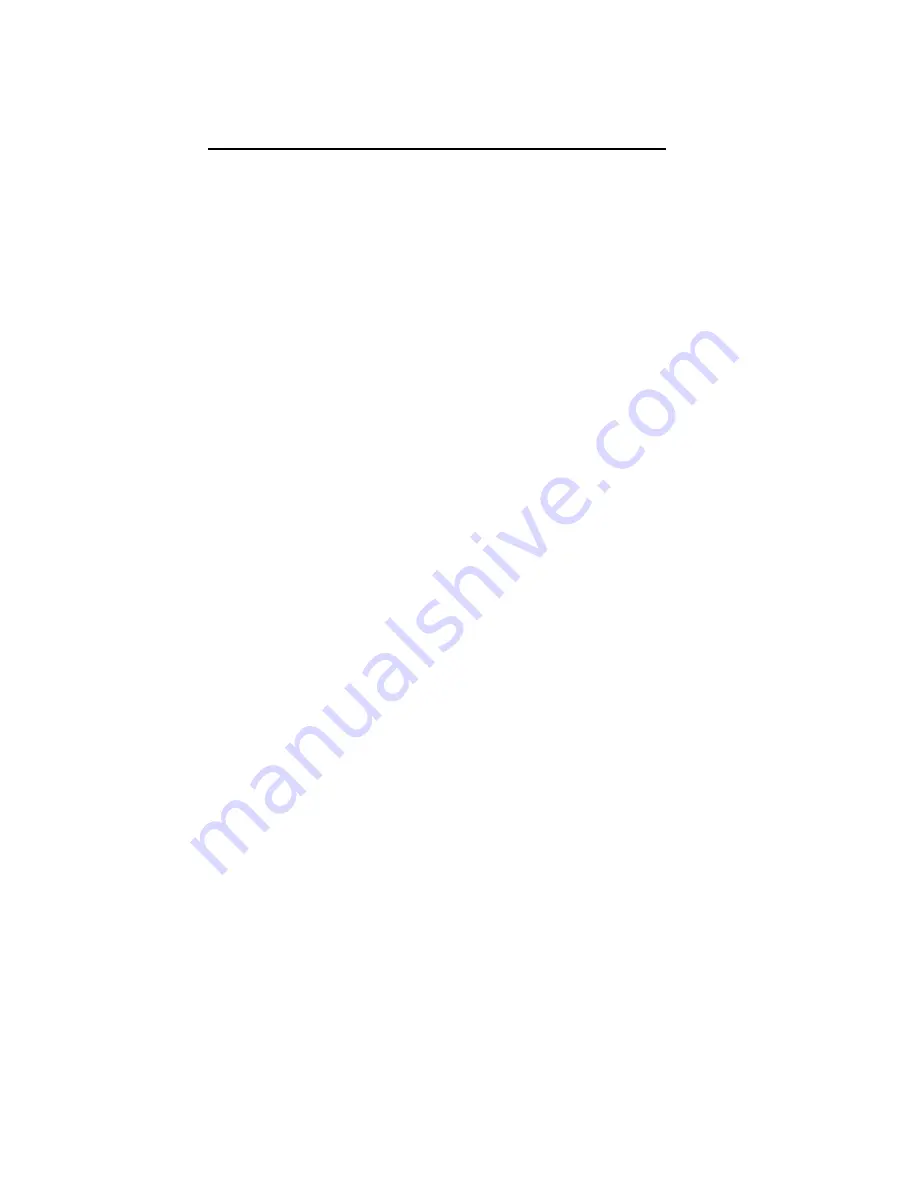
______________________________________________
HARRIS
888-9058-001
WARNING: Disconnect and lockout AC primary power prior to servicing
183
8.2.8 Protection, Control and Monitor Subsystem
(Refer to Module Control Board schematic, Tab 1000 in drawing package)
Each module is controlled and monitored by a module protection, control, and monitor
(PCM) subsystem. Drivers and PA modules utilize essentially the same PCM
subsystem. It consists of sensors and control logic within each module, and provides
protection against improper operating conditions. The heart of the module PCM
subsystem is a printed circuit assembly commonly known as the module control board.
The module control board performs protection from different detrimental operating
conditions through an essentially common scheme. It collects voltage samples that
provide indications of the operating parameters, and compares these samples to
reference voltages. Voltage comparators (U4, U6, U7, and U13) are used to compare the
samples to the references, and their outputs are digital signals which indicate either a
normal operating condition or a fault.
These digital signals drive PALs (Programmable Array Logic) (U1, U2, U3), which are
ICs consisting of hundreds of digital logic gates. The PALs perform two functions.
They send signals to the pass FETs, which are used as high-current switches to turn on
or off the 50 Volts DC supplied to the quarter modules. They also determine the
operating status indications given by the front panel LEDs.
Upon a module ENABLE signal, after the cabinet DC power supply reaches 44 Volts,
the control logic turns on the pass FETs. If a fault is detected, the control logic will turn
off the pass FETs, disabling the module.
The PCM subsystem performs several functions:
* Monitors input power level and protects the module from being overdriven. A sample
from the coupler at the input of the power divider is received at J1-9. If the sample is
above the reference established by voltage divider R20-R21, U6 pin 14 will go low,
indicating normal drive in a PA module. If the sample goes above the reference set by
R101, U6 pin 1 will go low, indicating an overdrive fault.
* Monitors output reflected power, and protects the module from elevated load VSWR.
Output reflected samples from the output directional coupler assembly are received at
J1-22. The VSWR fault threshold is established by R8. If the voltage at U6 pin 5,
determined by the reflected power, is greater than the voltage at pin 4, then pin 2 will go
low, indicating a VSWR fault.
* Monitors the DC power supply voltage, and protects the module from high and low
voltage extremes. The DC supply is sampled at J1-23, and is scaled down by R48, R47,
and R42. A maximum voltage reference is established by the +15 Volt regulated supply,
R43, and R44. If the sample exceeds the reference, U7 pin 1 will go high, indicating an
over-voltage fault.