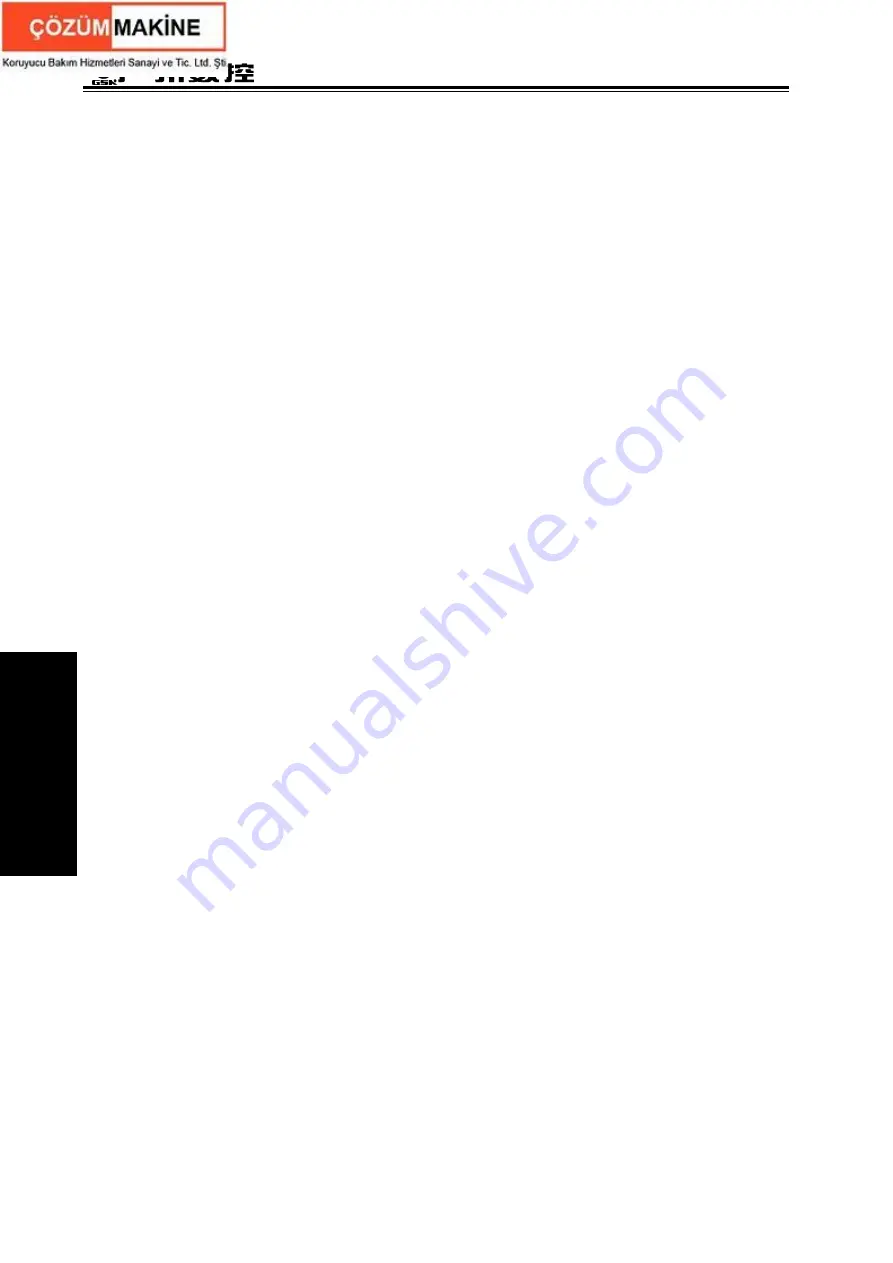
GSK980TDc Turning CNC System User Manual
414
Ⅲ
Connection
blocks
The larger the ACC&DEC time constant is, the slower the ACC&DEC is, the smaller the machine
movement impact and the lower the machining efficiency is, and vice versa.
If ACC&DEC time constants are equal, the higher the ACC&DEC start/end speed is, the faster
the ACC&DEC is, the bigger the machine movement impact and the higher the machining efficiency
is, and vice versa.
The principle for ACC&DEC characteristic adjustment is to properly reduce the ACC&DEC time
constant and increase the ACC&DEC start/end speed to improve the machining efficiency on the
condition that there is no alarm, motor out-of-step and obvious machine impact. If the ACC&DEC time
constant is set too small, and the start/end speed is set too large, it is easily to cause faults such as
drive unit alarm, motor out-of-step or machine vibration.
When the bit parameter No.007 BIT5(SMZ) =1, the feedrate drops to the start speed of the
ACC&DEC at the cutting path intersection, then it accelerates to the specified speed of the next block
to obtain an accurate positioning at the path intersection, but this will reduce the machining efficiency.
When BIT5=0, the adjacent cutting path transits smoothly by the ACC&DEC. The feedrate does not
always drop to the start speed when the previous path is finished and a circular transition
(non-accurate positioning) will be formed at the path intersection. The machining surface by this path
transition has a good finish and a higher machining efficiency. When the stepper motor drive unit is
applied, the BIT5 of the bit parameter No.007 should be set to 1 to avoid the out-of-step.
When the stepper motor drive unit is applied, the out-of-step may occur on the condition that
rapid traverse speed is too large, ACC&DEC time constant is too small, ACC&DEC start/end speed is
too large. The suggested parameter setting is as follows (the electronic gear ratio 1:1):
Data parameter No.022
≤
2500 Data parameter No.023
≤
5000
Data parameter No.155
≤
5000
Data parameter No.158
≥
350
Data parameter No.024
≥
350 Data parameter No.025
≥
350
Data parameter No.029
≥
150 Data parameter No.028
≤
100
Data parameter No.026
≥
200 Data parameter No.030
≤
50
If AC servo drive unit is applied to this system, the machining efficiency can be improved by a
larger start speed and a smaller ACC&DEC time constant setting. If optimum acc/dec characteristics
are required, the ACC&DEC time constant may be set to 0 which can be gotten by adjusting the AC
servo acc/dec parameters. The suggested settings for these parameters are as follows(electronic
gear ratio is 1:1):
Data parameter No.022
=
5000 Data parameter No.023
=
10000
Data parameter No.155
=
10000
Data
parameter
No.158
≤
60
Data parameter No.024
≤
60 Data parameter No.025
≤
60
Data parameter No.029
≤
50 Data parameter No.028
≤
500
Data parameter No.026
≤
50 Data parameter No.030
≤
400
The parameter settings above are recommended for use, please refer to the actual conditions of
the drive unit, motor characteristic and motor load for their proper setting.
4.5 Mechanical (Machine) Zero Adjustment
Adjust the relevant parameters based on the active level of the connection signal, zero return
type and direction applied:
BIT5 (DECI) of the bit parameter No.004: active level of deceleration signal in machine zero
return.
BIT0, BIT1, BIT2
,
BIT3
,
BIT4 (ZMX, ZMZ, ZMY
,
ZM4, ZM5) of the bit parameter No.006: X, Z,
Summary of Contents for GSK980TDc
Page 17: ...I Programming ...
Page 18: ...GSK980TDc Turning CNC System User Manual ...
Page 190: ...GSK980TDc Turning CNC System User Manual 172 Ⅰ Programming ...
Page 191: ...Ⅱ Operation Ⅱ Operation ...
Page 192: ...GSK980TDc Turning CNC System User Manua Ⅱ Operation ...
Page 326: ...GSK980TDc Turning CNC System User Manual 306 Ⅱ Operation ...
Page 327: ...Ⅲ Connection Ⅲ Connection ...
Page 328: ...GSK980TDc Turning CNC System User Manual Ⅲ Connection ...
Page 470: ...GSK980TDc Turning CNC System User Manual 448 Ⅲ Connection ...