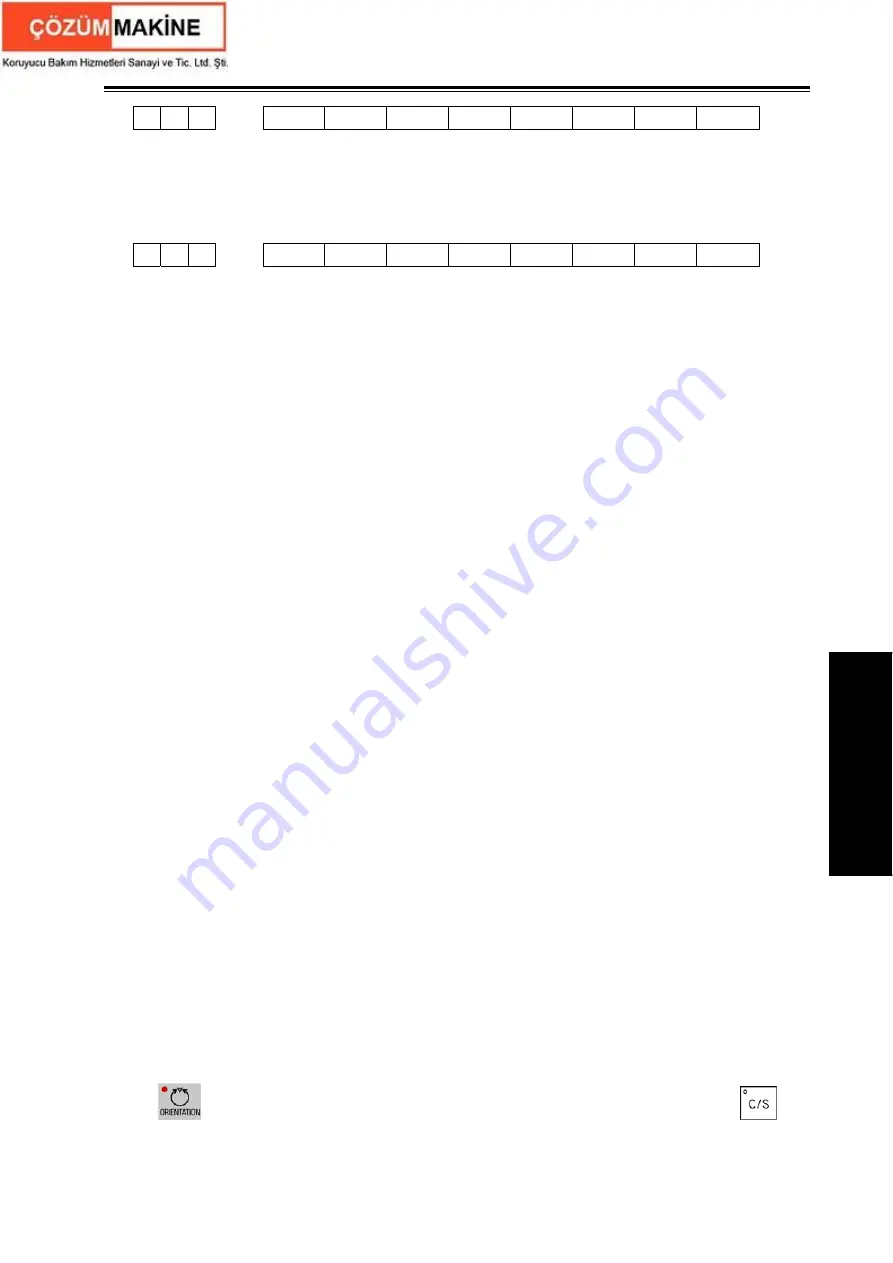
Chapter 2 Definition and Connection of Interface Signal
351
Ⅲ
C
o
n
n
e
c
tio
n
K 1 5
RCS RSCS
RCS =1: The spindle Cs function is valid;
=0: The spindle Cs function is invalid.
RSCS =1: The spindle contour control is disabled in emergency stop, reset;
=0: The spindle contour control is enabled in emergency stop, reset.
K 1 7
MSEN SALM2
MSEN =1: The multiple spindle control function is valid;
=0: The multiple spindle control function is invalid.
SALM2 =1: The system alarms when the check input signal of the 2
nd
spindle abnormality is
LOW;
=0: The system alarms when the check input signal of the 2
nd
spindle abnormality is
HIGH;
Function description(defined by the standard PLC program
)
1.1. After the multiple spindle control function setting is valid, the system defaults to the 1
st
spindle control after power-on;
1.2. When M03, M04, M05 is executed, the corresponding signal of the 1
st
spindle outputs, at
that time, the system sets the 1
st
spindle control, hereafter, the S command being executed will
change the 1
st
spindle speed. In a similar way, M63, M64, M65 is executed, the corresponding signal
of the 2
nd
spindle outputs, at the time, the corresponding signal of the 2
nd
spindle outputs, and is
switched into the 2
nd
spindle control, after that, the executed S command will change the 2
nd
spindle
speed.
1.3. The spindle switch is invalid in rigid tapping.
1.4. The manual CW, CCW, STOP, SPINDLE OVRRRIDE keys on the panel are valid only to the
1
st
spindle. When the current system is controlled by the 2
nd
spindle, the manual control key of the
spindle on the panel still controls the 1
st
spindle.
1.5. The spindle override of the 2
nd
spindle is fixed to 100%.
1.6. Cs axis control of two spindles can be separately switched and the current used spindle has
no requirements, that is, when the current is the 1
st
(2
nd
) spindle, the 2
nd
(1
st
) spindle executes the Cs
switch.
z
Cs control logic of the 2
nd
spindle
1.1. After M24 is execute, PLC
→
Drive sends the 2
nd
spindle speed/position control mode switch
signal VP2;
1.2 Drive unit starts the switch control mode. After the switch is completed, Drive
→
PLC outputs
the speed/position switch state signal VPO2;
1.3. After the PLC receives the spindle speed/position switch state signal VPO2, the 2
nd
spindle
contour control switch signal CON(G127.7) is set to 1. After the system has checked the 2
nd
spindle
contour control switch end signal FSCSL(F144.1), M24 execution is ended. The spindle control mode
switch is ended.
2. M25 execute processes are the same those of M24.
3. M25 only cancels M24 executing the speed/position switch. Executing M25 cannot switch the
system into the speed control mode when executing M29 switches the spindle into Cs contour
control.
4.
on the panel is only used to Cs switch of the 1
st
spindle. (For 980TDc-V, it is
key
on the panel)
5. Before switch, the spindle can rotate or stop. After switch, the spindle stops.
Summary of Contents for GSK980TDc
Page 17: ...I Programming ...
Page 18: ...GSK980TDc Turning CNC System User Manual ...
Page 190: ...GSK980TDc Turning CNC System User Manual 172 Ⅰ Programming ...
Page 191: ...Ⅱ Operation Ⅱ Operation ...
Page 192: ...GSK980TDc Turning CNC System User Manua Ⅱ Operation ...
Page 326: ...GSK980TDc Turning CNC System User Manual 306 Ⅱ Operation ...
Page 327: ...Ⅲ Connection Ⅲ Connection ...
Page 328: ...GSK980TDc Turning CNC System User Manual Ⅲ Connection ...
Page 470: ...GSK980TDc Turning CNC System User Manual 448 Ⅲ Connection ...